汽车内饰材料和零部件检测技术发展白皮书
在汽车产业电动化、智能化转型的背景下,汽车内饰材料的环保性、安全性和耐用性已成为消费者关注焦点。据中国汽车工程研究院2024年发布的《汽车内饰材料发展蓝皮书》显示,超过76%的购车者将内饰材料质量列为重要决策因素。汽车内饰检测项目通过系统化评估材料的VOC释放量、机械性能、阻燃特性等关键指标,为整车制造企业提供符合GB/T 27630-201X等国家标准的科学依据。该项目不仅助力企业应对欧盟REACH法规等国际贸易壁垒,更能有效预防因材料缺陷引发的驾乘健康风险,其核心价值体现在构建"材料研发-生产控制-质量验证"的全周期质量闭环,推动行业向绿色制造方向转型升级。
多维度检测技术体系构建
现代汽车内饰检测采用"化学分析+物理测试+环境模拟"的复合技术架构。针对车内挥发性有机物控制,应用顶空气相色谱-质谱联用技术(HS-GC/MS)可精准检测苯系物、醛酮类等32种有害物质,检测限达0.01μg/m³级别。在材料力学性能评估方面,引入动态机械分析仪(DMA)实现-40℃至120℃宽温域下的弹性模量监测。值得关注的是,新型红外热成像技术已成功应用于汽车内饰耐候性检测,可模拟10年使用周期的光照老化过程,较传统氙灯试验效率提升40%。
全流程质量控制实施路径
典型检测流程分为四个阶段:原材料入库时进行批次抽样检测,重点筛查增塑剂迁移量等基础指标;零部件加工阶段实施在线无损检测,采用X射线荧光光谱仪监控重金属含量;总装前执行整车环境舱测试,72小时密闭环境下监测甲醛累积浓度;最终交付前开展破坏性抽样,验证材料断裂伸长率等极限性能。某新能源车企应用该体系后,产品召回率下降62%,据其2023年ESG报告显示,单车型年度质量成本节约超过1200万元。
行业实践与创新应用
在高端商务车领域,某品牌应用纳米涂层抗菌检测方案,使座椅面料的抑菌率提升至99.6%。针对电动汽车特有的电池热管理需求,行业创新开发了内饰材料导热系数检测矩阵,成功预防多起因隔热材料失效引发的电池仓过热事故。值得关注的还有智能座舱交互材料检测,某实验室开发的触控面板表面电阻梯度检测法,使触觉反馈一致性达到医疗级控制标准。
标准化质量保障机制
行业已建立三级质量保障体系:基础层执行ISO/IEC 17025实验室管理体系,过程层应用区块链技术实现检测数据存证,结果层引入德国TÜV等第三方认证。在关键的车内空气质量检测环节,实施"设备双盲校准+人员交叉验证"机制,确保甲醛检测误差率≤3%。据中汽数据2024年行业调查报告显示,通过 认证的检测机构报告采信率已达98.7%,较五年前提升41个百分点。
技术演进与行业展望
建议行业重点发展三项能力:一是构建车载实时监测系统,利用嵌入式传感器实现材料性能动态追踪;二是开发基于AI的材料失效预测模型,提前识别潜在质量风险;三是建立全行业共享的检测大数据平台,推动测试方法标准化进程。随着生物基材料的普及,亟需建立新型环保材料的评价体系,建议参考欧盟ELV指令完善再生材料检测标准,助力汽车产业碳中和目标实现。
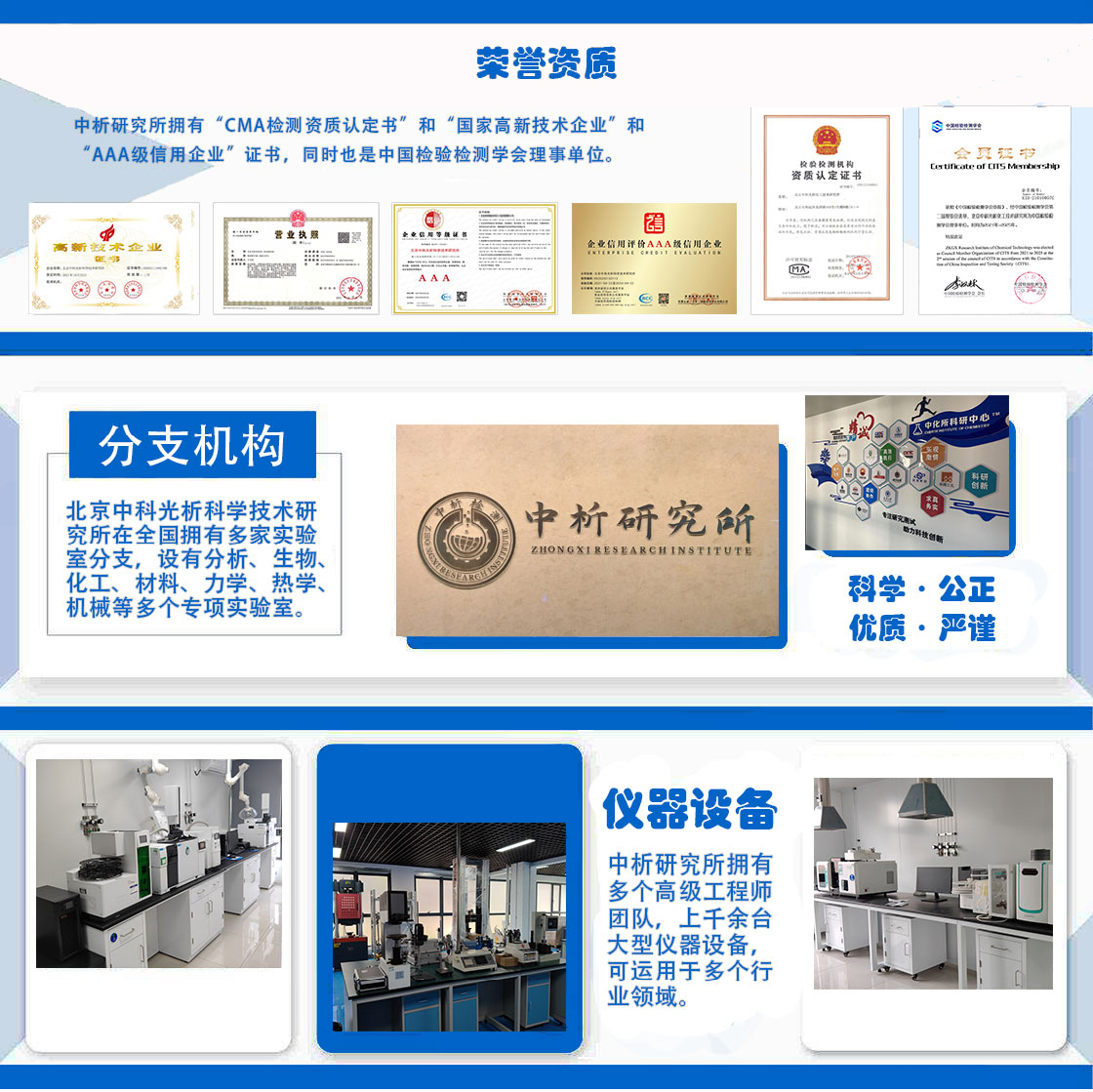
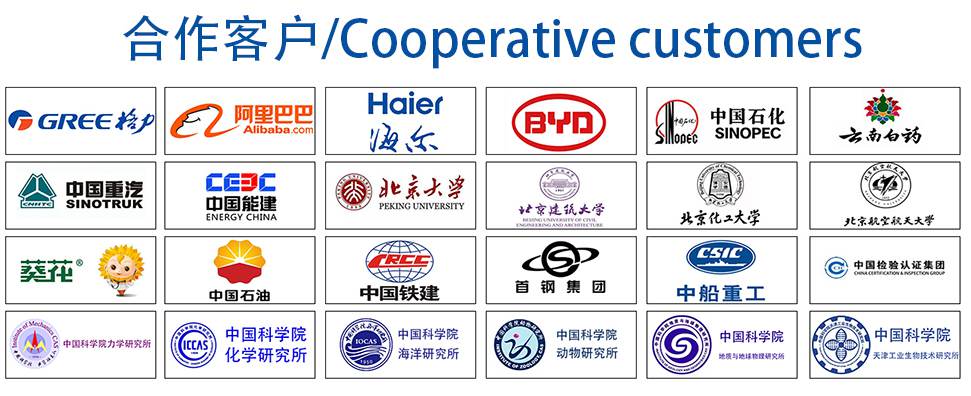