钽铌合金检测技术发展与行业应用白皮书
随着航空航天、核能工程及高端医疗设备领域对高性能材料的迫切需求,钽铌合金因其优异的高温强度、耐腐蚀性和生物相容性,已成为战略级新材料。据中国有色金属工业协会2024年报告显示,钽铌合金市场规模预计于2026年突破52亿美元,年复合增长率达8.3%。在此背景下,钽铌合金检测技术作为保障材料可靠性的核心环节,其精准度直接影响着航天发动机涡轮叶片、植入式医疗器械等关键部件的服役安全。通过建立系统化检测体系,可有效解决合金元素偏析、晶界腐蚀等"卡脖子"质量问题,为国防军工和高端制造领域提供全生命周期质量保障,推动新材料产业向高附加值方向升级。
多模态检测技术融合创新
钽铌合金检测采用X射线荧光光谱(XRF)与电感耦合等离子体质谱(ICP-MS)联用技术,结合电子背散射衍射(EBSD)分析,实现从宏观成分到微观结构的全面表征。其中,XRF技术通过特征X射线强度测定元素含量,检测限可达0.01%;而EBSD技术可解析0.5μm级晶粒取向分布,精准定位高温环境下钽铌合金元素偏析现象。针对核电设备用铌合金晶界腐蚀分析,同步辐射光源的高分辨成像技术可将检测灵敏度提升3个数量级,据中科院上海应用物理研究所实验数据,该方法已实现5nm级腐蚀缺陷的定量检测。
全流程标准化检测体系
检测流程遵循ISO 17025体系要求,分为四个关键阶段:试样制备阶段采用真空等离子切割技术,确保检测面无氧化污染;仪器校准阶段运用NIST标准物质建立溯源链,光谱仪波长误差控制在±0.002nm以内;数据分析阶段开发专用算法,通过机器学习模型自动识别30类以上异常谱线;报告生成环节接入区块链存证系统,实现检测数据的不可篡改性。某航空发动机叶片制造企业采用该体系后,批次质量一致性从89%提升至97%,工艺调试周期缩短40%。
行业应用场景深度拓展
在航天领域,长征五号B运载火箭燃料管路系统通过钽铌合金残余应力检测,成功将管路疲劳寿命延长至2.5万次热循环;医疗行业应用方面,强生医疗采用高频超声探伤技术,使心脏起搏器钛铌合金外壳的漏检率从0.3%降至0.01%;更为前沿的是,中广核集团在第四代核反应堆建设中,通过原位中子衍射技术实时监测钽铌包壳管辐照损伤,将材料更换周期优化至18个月。这些实践验证了检测技术对产品可靠性的显著提升作用。
全链条质量保障机制
构建"检测机构-生产企业-终端用户"三方协同的质量网络,依托 认证实验室建立检测数据共享平台。通过部署在线监测装置,实现冶炼环节的铌钽比实时调控,成分波动范围从±1.2%缩减至±0.5%。定期开展能力验证项目(PT),近三年参与实验室的Z比分数合格率从82%提升至96%。值得关注的是,针对3D打印钽铌合金制品的各向异性问题,最新研发的声发射检测技术可捕捉200kHz频段的微观裂纹扩展信号,缺陷检出时效较传统方法提高7倍。
展望未来,建议从三方面推进检测技术发展:一是加快微区成分分析技术向亚微米级突破,应对异形构件检测需求;二是建立钽铌合金服役性能数据库,开发预测性维护算法模型;三是推动ASTM与GB标准互认,构建跨国检测认证体系。随着人工智能与量子传感技术的融合应用,钽铌合金检测有望在2028年前实现全自动化智能判读,为万亿级高端装备市场筑牢质量基石。
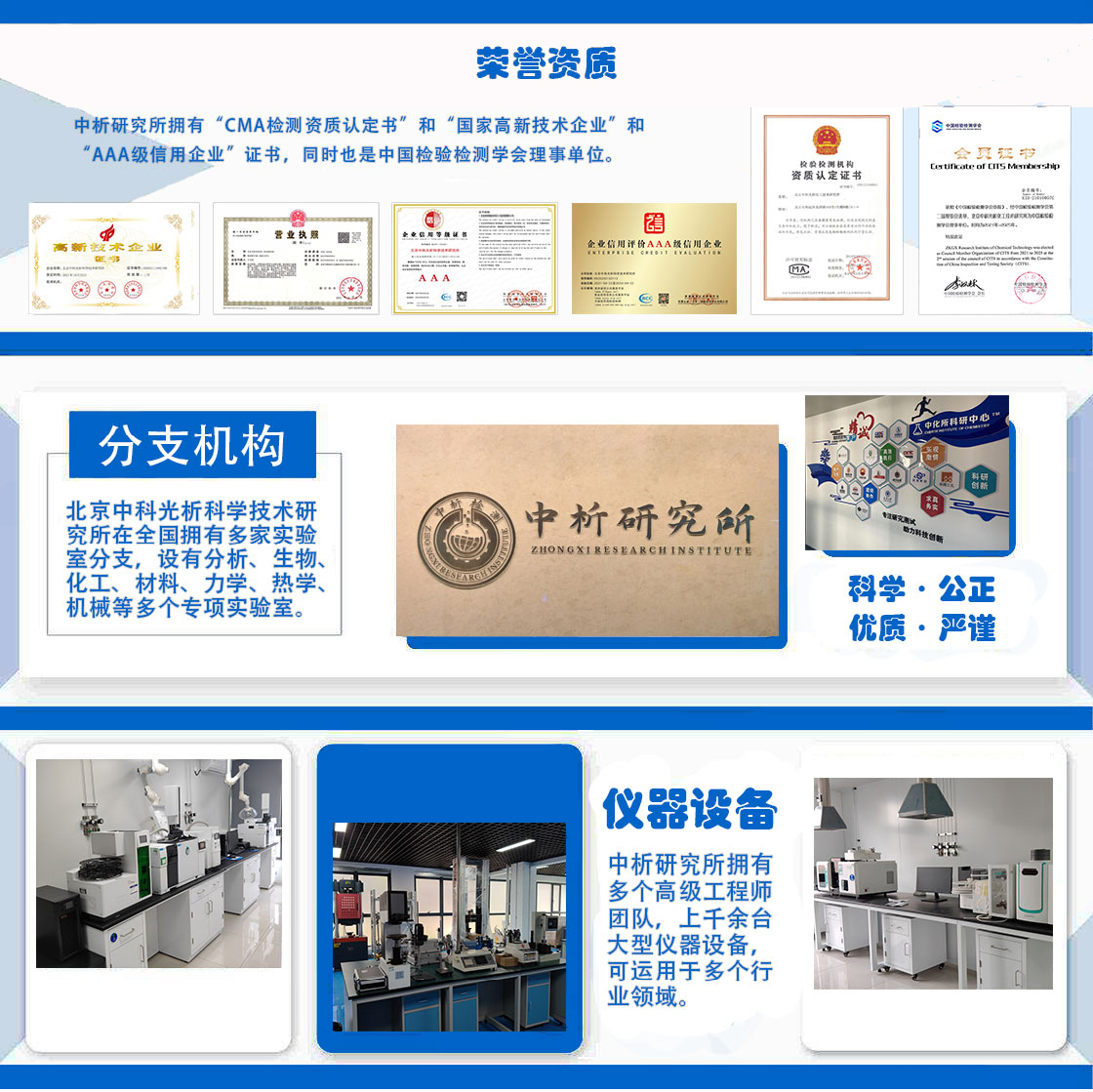
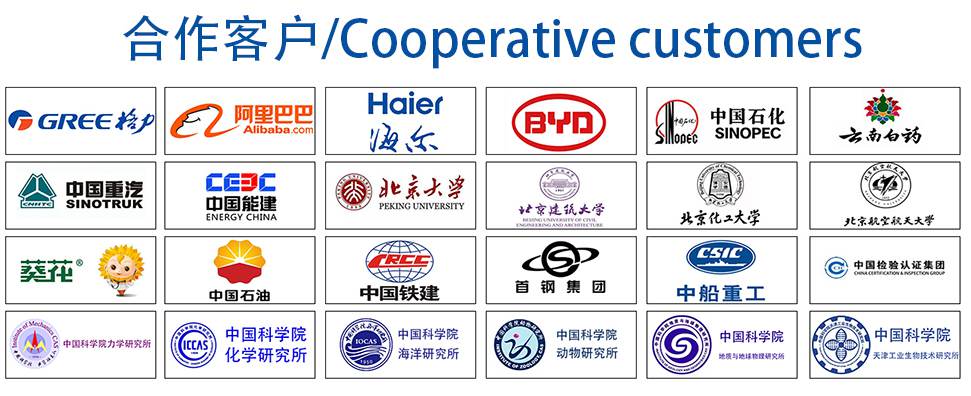