电机与电机控制器检测项目全解析
一、电机检测项目
1. 电气性能检测
- 绝缘电阻测试 使用兆欧表测量绕组与外壳间的绝缘电阻(通常要求≥100MΩ@500V DC),确保无漏电风险。
- 耐压测试 施加高于额定电压的交流高压(如1500V AC/1分钟),检测绕组与外壳的耐击穿能力。
- 空载特性测试 测试电机在无负载时的电流、电压、转速及功率因数,验证设计参数一致性。
- 负载特性测试 通过加载设备模拟实际工况,测量转矩-转速曲线、效率曲线及温升,评估输出性能。
- 堵转测试 短时锁定转子,检测堵转电流和转矩,验证过载保护机制的可靠性。
2. 机械性能检测
- 振动与噪声测试 利用加速度传感器测量各方向振动值(如≤2.8mm/s),通过声级计评估噪声水平(如≤75dB(A))。
- 轴承状态监测 使用振动频谱分析或红外热像仪,检测轴承磨损、润滑异常等问题。
- 转子动平衡测试 通过动平衡机校正转子偏心率,确保高速运转平稳性(残余不平衡量≤0.5g·mm/kg)。
3. 热性能检测
- 温升试验 在额定负载下持续运行至热稳态,记录绕组、轴承温度(如绕组温升≤80K)。
- 热循环测试 模拟冷热交替环境(-40℃~120℃),验证材料热膨胀匹配性及绝缘层耐久性。
4. 环境适应性测试
- 防护等级(IP)验证 通过喷水、防尘试验确认密封性(如IP67:防尘6级、防水7级)。
- 盐雾腐蚀测试 模拟海洋或工业环境(5% NaCl溶液喷雾),评估金属部件耐腐蚀性(48小时无锈蚀)。
- 高低温循环测试 极端温度下测试启动性能(如-30℃冷启动、85℃高温运行)。
二、电机控制器检测项目
1. 硬件功能验证
- 输入/输出特性测试 验证电压/电流输入范围(如200-750V DC)、PWM输出精度(误差≤1%)。
- 保护功能测试 模拟过流、过压、欠压、短路等故障,检测保护响应时间(如过流保护≤10μs)。
- IGBT驱动测试 评估开关频率(如10-20kHz)、死区时间设置及驱动信号波形稳定性。
- EMC测试 依据CISPR 25标准,检测辐射发射(30MHz-1GHz)及传导抗扰度(ISO 11452-4)。
2. 软件与控制算法测试
- 控制策略验证 通过dSPACE或NI平台仿真,测试矢量控制(FOC)、弱磁控制等算法的动态响应。
- CAN通信测试 校验通信协议(如CANopen/J1939)、报文周期及错误帧处理机制。
- 故障诊断与恢复 注入传感器失效、通讯中断等故障,验证诊断码(DTC)生成及安全状态切换。
3. 环境与可靠性试验
- 散热性能测试 在最高环境温度下(如105℃),监测散热片温度及IGBT结温(≤150℃)。
- 振动耐久测试 依据IEC 60068-2-6标准,施加10-2000Hz随机振动,持续2小时无结构损坏。
- 湿热老化测试 85℃/85%RH环境中持续500小时,检测PCB绝缘电阻与元件性能衰减。
三、系统联调检测项目
-
- 阶跃负载下转矩响应时间(如0-100%负载≤50ms)。
- 转速跟踪精度(误差≤±0.5%)。
-
- 全工况MAP图绘制,标定最高效率点(如永磁同步电机≥95%)。
-
- 连续运行1000小时(额定负载),统计性能衰减率(如效率下降≤2%)。
-
- 搭载测功机模拟NEDC/WLTC循环,验证能耗与热管理策略。
四、总结
- 电机:绝缘耐压、负载特性、温升、动平衡。
- 控制器:保护功能、EMC、算法稳定性、通信可靠性。
- 系统联调:动态响应、效率优化、耐久性验证。
上一篇:恶臭(臭气)检测下一篇:冷水水表(CJ)检测
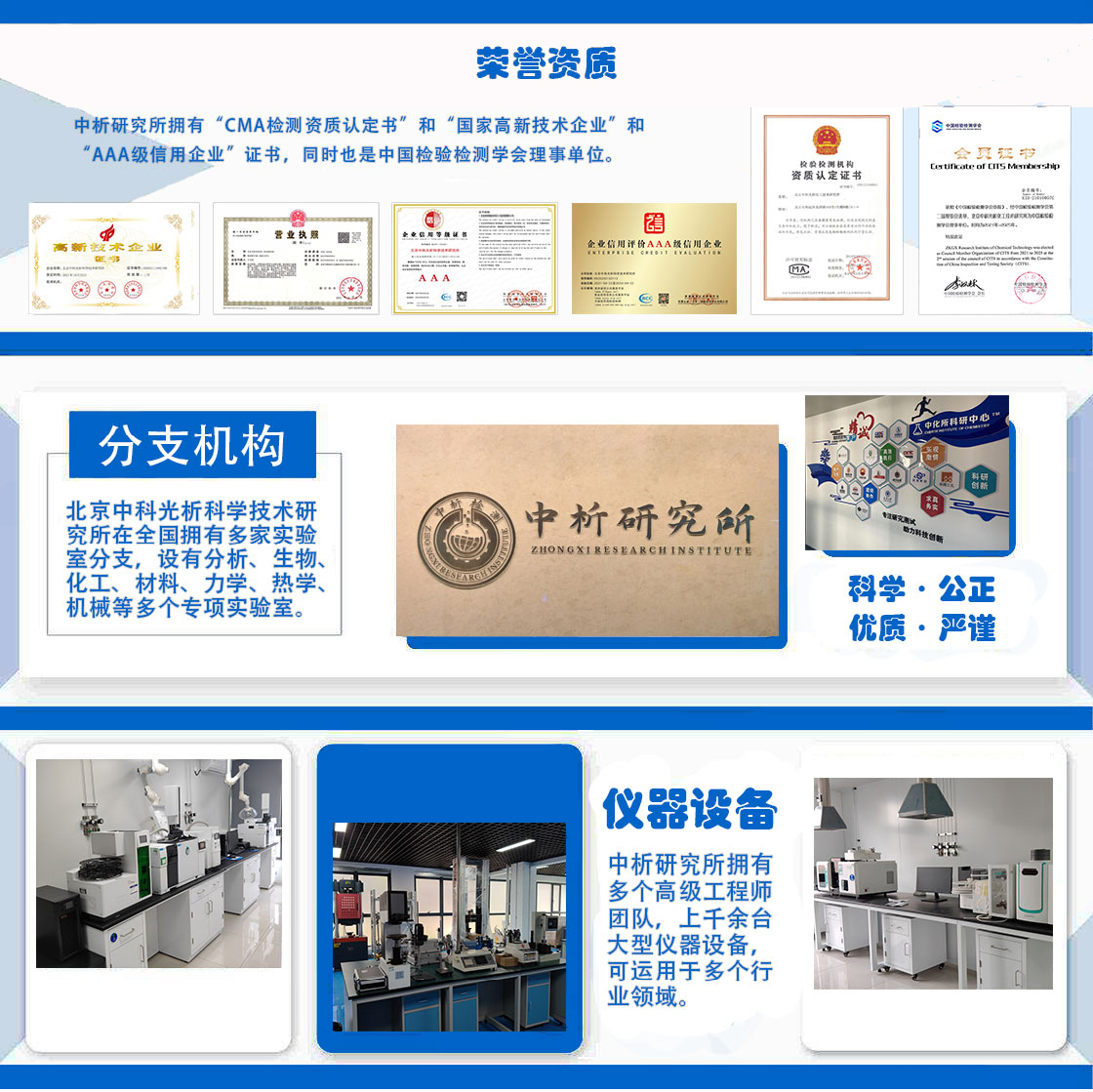
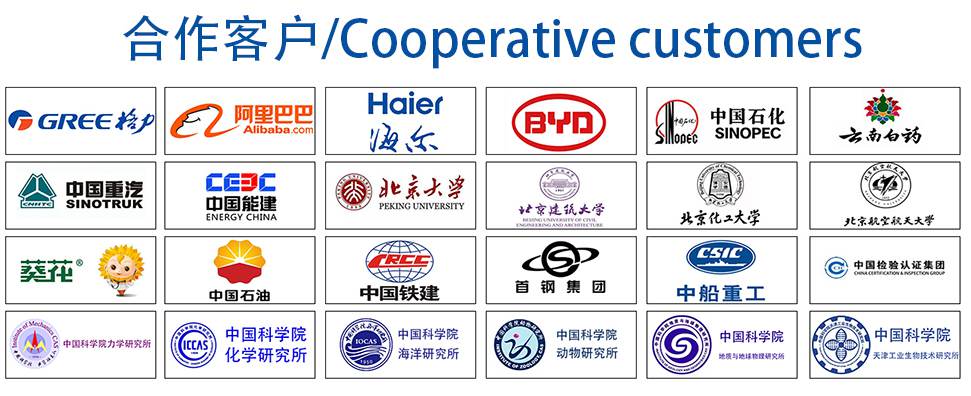
材料实验室
热门检测
223
189
166
181
179
182
191
183
181
195
187
181
179
176
177
173
185
179
189
186
推荐检测
联系电话
400-635-0567