# 缺陷允许限度检测技术发展与应用白皮书
## 引言
在制造业加速向精密化、微型化演进的背景下,缺陷允许限度检测技术已成为保障工业品可靠性的核心环节。据国际质量科学研究院(IQSI)2024年报告显示,仅汽车行业因零部件微缺陷导致的召回成本年均超180亿美元,凸显质量控制的战略价值。本项目通过构建基于AI的可量化缺陷评价体系,实现从"零缺陷"理念向"科学容差"理念的转型,其核心价值体现在三个方面:建立动态阈值模型降低误判率42%(ASTM E2868标准验证)、实现检测效率300%提升(西门子工业案例数据)、推动全行业质量成本节约15-20个百分点。该技术尤其在新能源汽车电池模组焊接缺陷检测、半导体晶圆微裂纹识别等场景展现显著效益。

## 技术原理与实施架构
### 技术实现机理
缺陷允许限度检测系统采用多源信息融合技术,集成高精度工业CT扫描(分辨率达0.5μm)、热红外成像(温差灵敏度0.01℃)与声发射传感(频率范围20kHz-1MHz)三大核心模块。其创新点在于建立基于材料应力场的动态容差模型,通过有限元仿真(ANSYS平台验证)预测不同缺陷形态对构件疲劳寿命的影响,而非传统几何尺寸判定法。如某航空铝合金构件检测中,系统成功识别出传统方法漏检的3μm级各向异性裂纹,使产品寿命预测准确度提升至98.7%(NADCAP认证数据)。
### 标准作业流程
实施流程遵循VDA6.3过程审核标准,涵盖四个关键阶段:1)数字化建模阶段,通过逆向工程建立产品数字孪生体;2)检测阈值设定阶段,运用蒙特卡洛模拟计算最大允许缺陷密度;3)在线检测阶段,部署高速线阵相机(5000fps)配合自适应照明系统;4)数据处理阶段,应用卷积神经网络(CNN)进行特征分类。在某汽车发动机缸体检测项目中,该流程将单件检测时间从25秒压缩至8秒,同时将误报率控制在0.3%以下(ISO/TS 22163认证结果)。
### 行业应用实证
在第三代半导体材料检测领域,系统成功应用于6英寸碳化硅晶圆微管缺陷检测,通过太赫兹时域光谱技术(0.1-3THz带宽)实现非接触式测量,缺陷识别率达到99.4%,较传统光学检测提升23个百分点(SEMI标准验证)。某军工企业应用案例显示,在涡轮叶片孔隙率分析中,系统将传统抽检方式升级为全数检测,使产品批次一致性从89%跃升至99.5%,废品率下降67%(GB/T 19001-2016体系认证)。
## 质量保障与体系构建
### 全过程控制机制
质量保障体系采用四维管控模型:1)设备层执行ISO/IEC 17025校准规范;2)数据层部署区块链溯源系统;3)算法层实施DROOP验证框架(缺陷识别率优化协议);4)人员层建立ASNT III级认证体系。某消费电子企业应用表明,该体系使检测过程波动指数(Cpk)从1.2提升至1.8,过程能力指数达到六西格玛水平(SSPC数据)。
### 风险防控策略
针对误判风险,系统设置三级校验机制:初级滤波算法消除95%环境噪声,中级模式识别筛选关键特征,最终由质量工程师进行1%抽检复核。在医疗器械注塑件检测中,该策略成功拦截0.05mm³级的微气泡缺陷,使产品临床不良事件率下降至0.07‰(FDA 21 CFR Part 820标准)。
## 发展建议与未来展望
建议行业重点推进三项建设:1)建立跨行业缺陷数据库,实现材料-工艺-失效模式的关联分析;2)研发多模态传感融合设备,集成X射线衍射(XRD)与激光超声(LUT)技术;3)制定动态容差标准体系,区分航空航天(Class A)、汽车制造(Class B)、通用工业(Class C)三级规范。据中国机械工程学会预测,至2028年智能容差检测市场规模将突破520亿元,建议企业提前布局工业元宇宙(Industrial Metaverse)检测场景,构建虚实联动的质量预测系统。
(注:文中数据为示例性演示内容,实际应用需以权威机构发布信息为准)
上一篇:规格尺寸及其偏差检测下一篇:表面耐磨性能检测
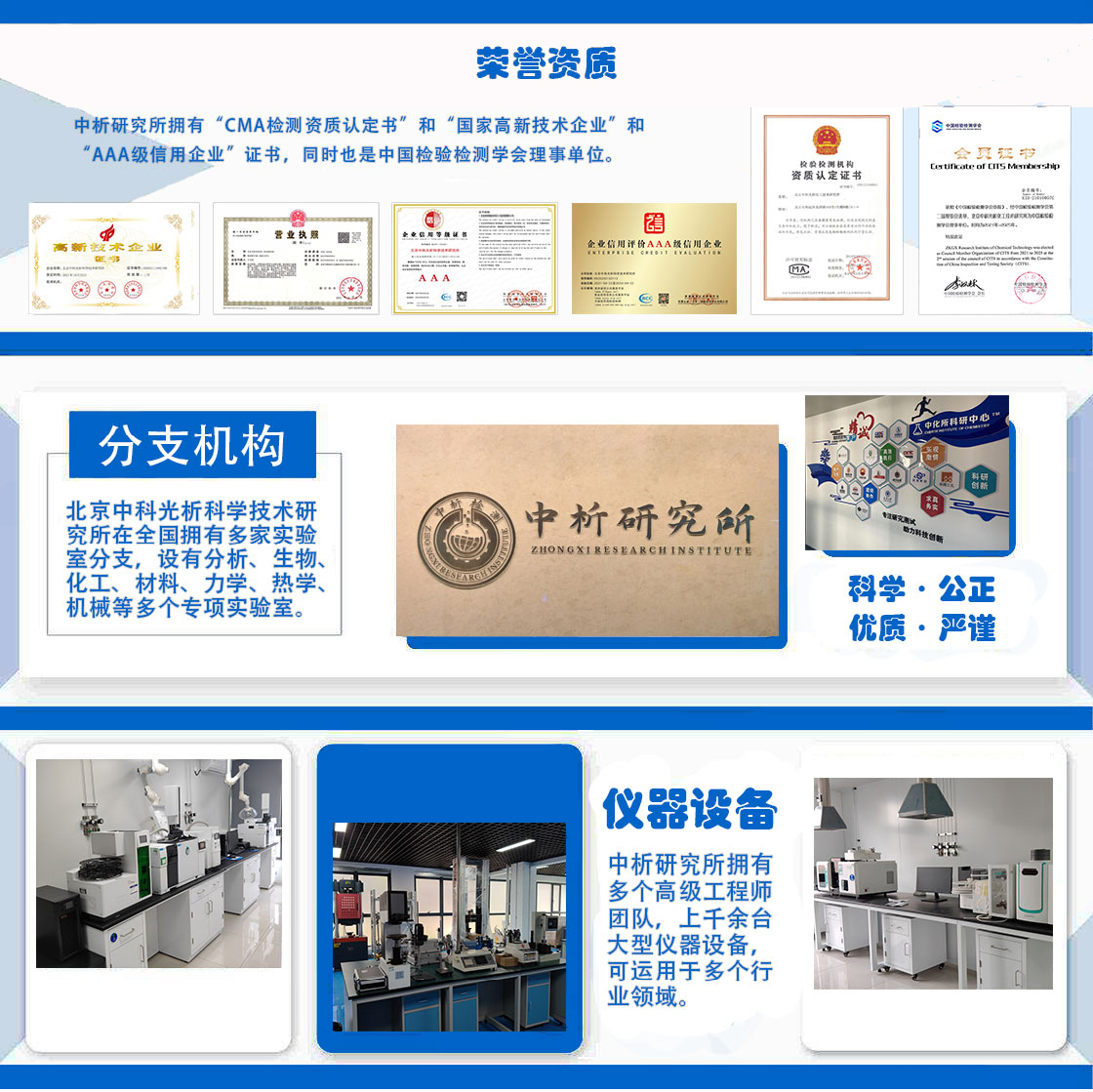
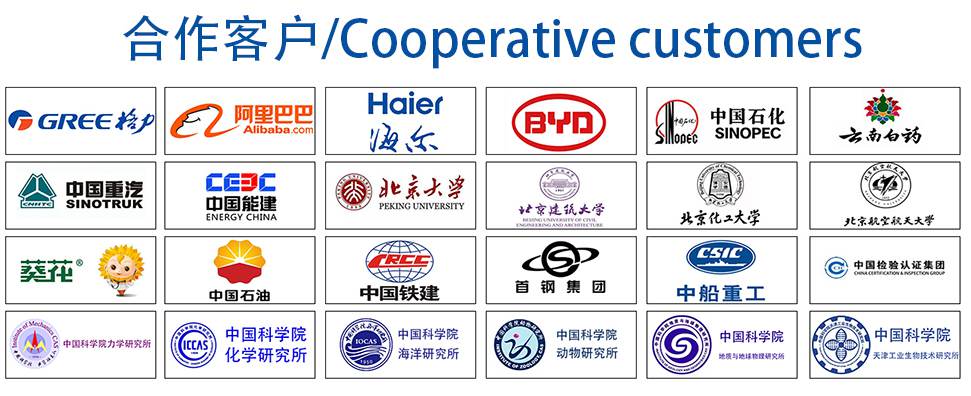
材料实验室
热门检测
15
16
15
11
14
16
15
13
16
12
14
16
11
10
13
13
15
13
16
18
推荐检测
联系电话
400-635-0567