铝及铝合金晶粒细化用合金线材检测项目解析
一、化学成分检测
-
- 检测内容:钛(Ti)、硼(B)、碳(C)等核心细化元素的含量。
- 方法:采用光谱分析法(如OES)、电感耦合等离子体发射光谱法(ICP-OES)或化学滴定法。
- 标准要求:
- Ti含量范围:通常为3%~6%(Al-Ti-B线材);
- B含量范围:0.2%~1.5%(根据牌号调整);
- 杂质元素(Fe、Si等)需低于0.1%~0.3%,以避免干扰细化效果。
-
- 检测氧(O)、氢(H)等气体杂质含量,避免线材内部缺陷。
二、物理性能检测
-
- 直径公差:利用激光测径仪或千分尺测量,公差需符合±0.05 mm以内。
- 表面质量:目视或显微镜检查表面裂纹、划痕、氧化皮等缺陷(按GB/T 3191或ASTM B941标准)。
-
- 拉伸强度:通过万能试验机测试抗拉强度(≥100 MPa)和延伸率(≥10%),确保线材在加工过程中不断裂。
- 硬度测试:采用维氏硬度计(HV),控制硬度范围以适应拉拔工艺。
三、微观组织分析
-
- 检测方法:金相显微镜(OM)或扫描电镜(SEM)观察TiB₂、TiAl₃等中间相的尺寸(通常要求≤5 μm)及弥散度。
- 评定标准:细化相需均匀分布,无团聚现象。
-
- 测试流程:截取线材样品,通过电解抛光+阳极覆膜处理后,使用图像分析软件(如ImageJ)统计晶粒尺寸(目标:细化后晶粒≤200 μm)。
四、加工性能测试
-
- 模拟线材在绕卷或弯曲加工中的表现,要求弯曲180°后无裂纹。
-
- 评估线材在连续拉拔过程中的延展性和表面光洁度。
五、晶粒细化效果验证
-
- 方法:参照ASTM E112或GB/T 3246,将线材加入铝熔体(如工业纯铝),凝固后检测晶粒尺寸。
- 合格标准:晶粒度等级≥1级(平均晶粒尺寸≤200 μm)。
-
- 在线材实际使用场景(如连铸连轧)中评估细化效率和稳定性。
六、包装与标识检测
- 包装密封性
- 检测防潮、防氧化封装是否完好(如真空包装或惰性气体保护)。
- 标识合规性
- 核对牌号、批次号、生产日期等信息是否符合GB/T 3190或AMS 4170标准。
七、参考标准
- 国际标准:ASTM B941(铝及铝合金线材规范)、ISO 209(铝化学分析)。
- 国内标准:GB/T 3191(铝及铝合金挤压棒材)、GB/T 7999(铝及铝合金光电直读光谱分析方法)。
结语
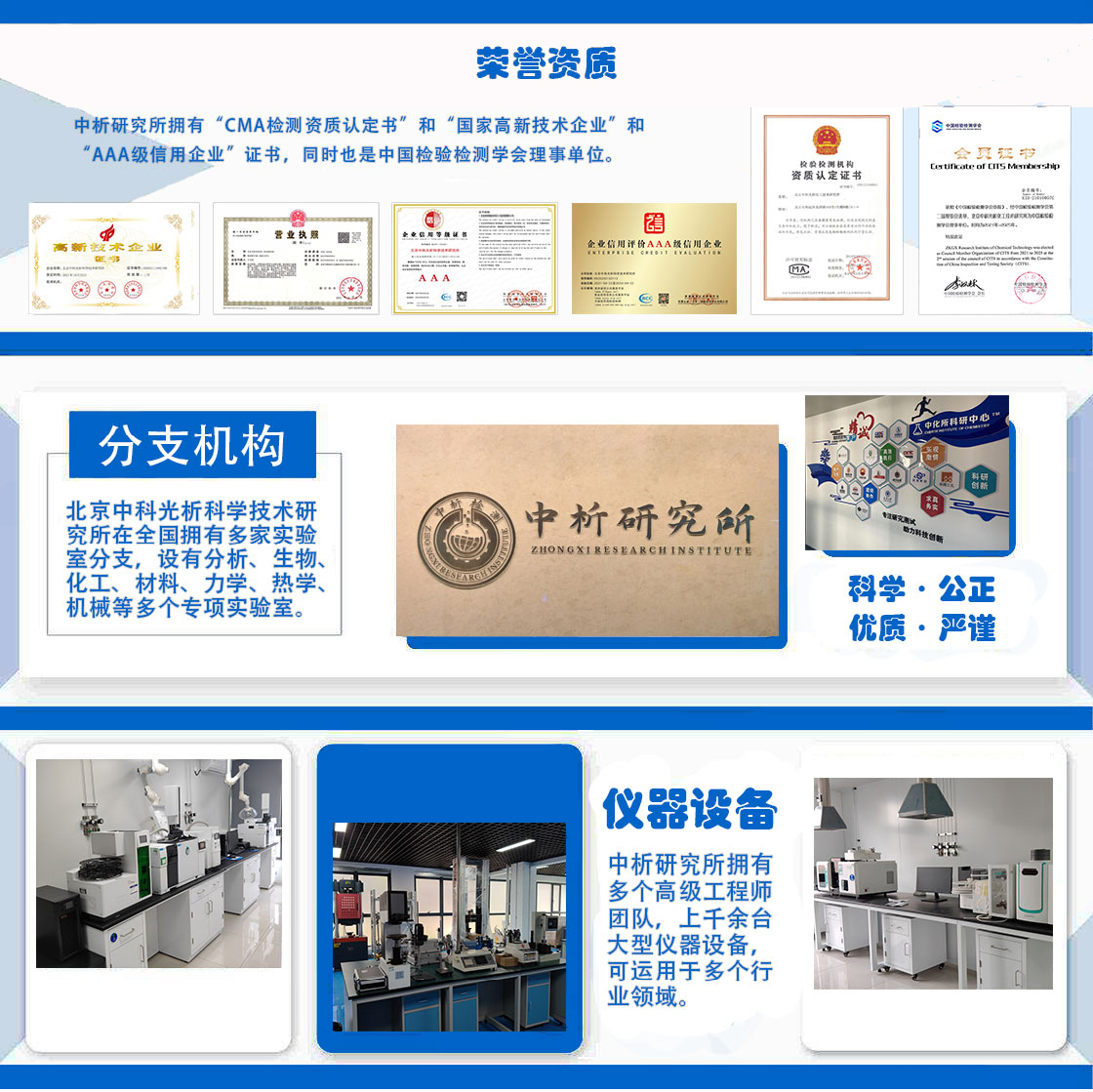
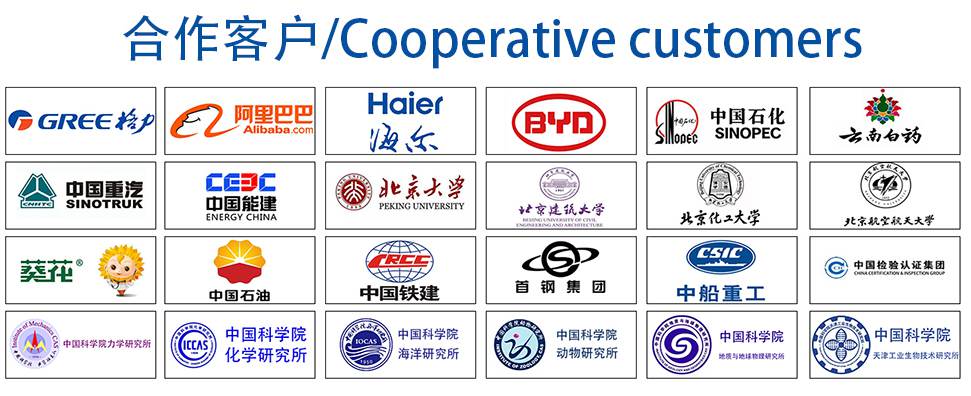
材料实验室
热门检测
225
197
168
186
182
185
194
185
185
196
188
182
183
180
179
174
188
182
191
189
推荐检测
联系电话
400-635-0567