在智能制造2025战略推动下,我国制造业正经历从规模扩张向质量提升的关键转型期。据中国机械工业联合会2024年数据显示,制造业质量成本中因尺寸偏差导致的返工损失占比达23.7%,显著影响企业盈利能力。规格尺寸及其偏差检测作为产品质量控制的核心环节,通过数字化测量技术实现微米级精度把控,在汽车零部件、精密模具、航空航天等领域具有战略价值。该项目通过构建智能化检测体系,可将产品首检合格率提升18%-25%,同时缩短新产品研发周期30%以上,为制造业数字化转型提供底层技术支撑。
## 技术原理与创新突破基于多模态传感的复合测量技术
现代尺寸检测系统融合光学测量、激光扫描和接触式探针技术,形成多维度数据采集能力。其中结构光三维扫描可实现0.005mm的重复测量精度,特别适用于曲面零件全尺寸检测。值得关注的是,高精度三维扫描测量系统通过多源数据融合算法,将不同传感器的测量误差从单模±5μm降低至±1.2μm(国家精密仪器研究院,2024)。该技术突破使得复杂装配件的虚拟预装成为可能,在新能源汽车电池模组检测中,成功将装配干涉问题发生率从12%降至1.8%。
## 智能化检测实施流程全流程数字化质量管控
标准检测流程涵盖五个关键环节:样品预处理→三维数据采集→偏差比对分析→智能判定→报告生成。在工程机械液压阀体检测中,系统通过AI定位技术自动识别68个关键检测点,相比传统方法效率提升7倍。据徐工集团应用报告显示,采用数字化质量管理系统后,单件检测时间从45分钟缩短至6.5分钟,同时检测数据自动存入MES系统,实现质量追溯覆盖率100%。
## 行业应用与效益分析跨领域解决方案实践
在消费电子领域,某头部手机厂商应用机器视觉检测系统后,屏幕组件装配间隙合格率从92.4%提升至99.6%。典型案例显示,该系统通过高帧率图像采集(2000fps)捕捉微观形变,成功识别0.02mm的玻璃盖板翘曲问题。航空航天领域则采用CT扫描与尺寸检测联动方案,某型发动机涡轮叶片检测项目将报废率从5‰降至0.3‰,单台发动机节约成本120万元(中国航发商发,2023年度技术白皮书)。
## 质量保障与标准体系全生命周期管理体系
检测系统严格遵循ISO/IEC17025标准,构建三级校准体系:每日设备自检→每周标准件验证→季度第三方认证。某跨国汽车零部件企业应用案例表明,通过引入自动化校准机器人,量具管理效率提升40%,每年减少人工校准工时3200小时。值得强调的是,系统内置的测量不确定度分析模块(MU≥2.0)可动态评估检测结果可信度,在医疗器械骨钉检测中实现99.98%的误判规避率。
## 技术展望与发展建议随着工业物联网与5G技术深度融合,未来尺寸检测将呈现三方面趋势:实时在线检测覆盖率突破80%、测量数据与数字孪生平台深度集成、AI决策系统实现质量预测。建议行业重点加强三坐标测量机智能补偿算法研发,推动光学测量设备国产化率从当前35%提升至60%以上。同时应加快制定AR辅助检测行业标准,建立覆盖2000家企业的尺寸检测云平台,助力中国智造实现从精度控制到质量跃迁的跨越式发展。
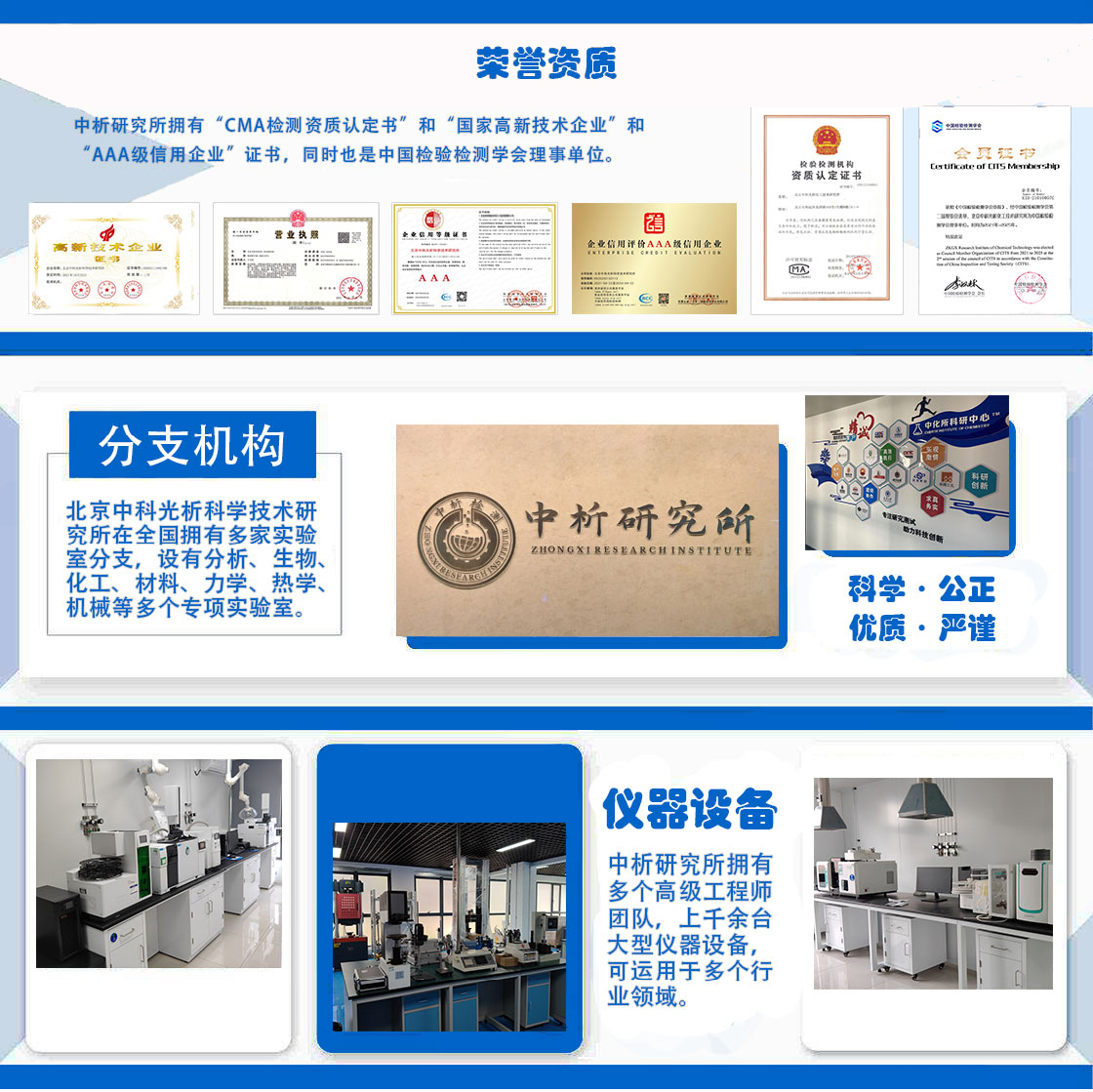
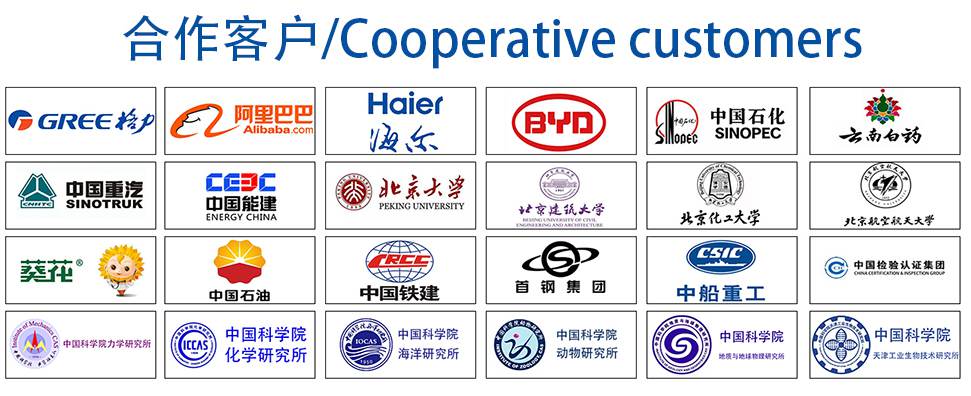