# 表面安装开关焊槽法的可焊性检测技术研究
## 行业背景与项目价值
随着5G通信、智能终端设备向微型化发展,表面安装技术(SMT)在电子制造业的应用占比已突破82%(据IPC国际电子工业联接协会2024年报告)。作为SMT制程的核心环节,焊槽法的可焊性直接决定了电子元器件的连接可靠性和使用寿命。在工业4.0质量追溯体系要求下,表面安装开关的可焊性检测项目具有三重核心价值:其一,通过量化焊接润湿角、焊料爬升高度等参数,实现焊接缺陷的早期预警;其二,建立工艺参数与焊接质量的映射模型,为高密度互连设计提供数据支撑;其三,满足汽车电子AEC-Q200标准中对连接点机械强度的严苛要求,将返修成本降低35%以上。该项目填补了微型化焊点动态检测的技术空白,成为提升电子制造良率的关键控制点。
## 技术原理与检测机制
### h2 润湿平衡法的动态分析体系
焊槽法检测基于JIS Z3198标准,通过高精度天平实时记录焊料对器件引脚的润湿力曲线。系统采用双温区控制技术,在230±5℃的SnAgCu焊料槽中,以3mm/s恒定速度完成引脚浸渍。检测终端同步采集润湿力、润湿时间及表面张力参数,结合AI图像处理系统对焊料爬升形态进行三维建模。值得注意的是,该体系创新集成了"表面张力动态分析算法",可将引脚氧化层对润湿角的影响量化至0.1°精度,有效识别0.05μm级别的金属间化合物异常。
### h2 分级检测流程设计
项目实施采用三级质量门控制模式:初级检测针对引脚镀层厚度(XRF检测≥0.8μm)、中级进行焊料兼容性试验(85℃/85%RH环境老化168小时)、终级实施动态焊接模拟。在汽车电子领域,特别增设-40℃~125℃温度循环测试模块,模拟车载ECU模块的极端工况。据富士康制造研究院实测数据,该流程使BGA封装器件的虚焊率从1.2‰降至0.3‰。
### h2 工业物联网场景应用
在智能手表主板生产线上,检测系统与MES系统深度集成,实现每批次2000个焊点的过程能力指数(CPK)实时监控。当检测到某批次引脚润湿时间超过0.8秒阈值时,系统自动触发工艺参数优化程序,将预热温度从150℃提升至170℃,使焊料流动性提升23%。在新能源汽车BMS控制模块案例中,通过对比不同镀层材料的"金属间化合物生长评估",确定化学镀镍钯金方案可将高温存储试验的焊点开裂率降低41%。
## 质量保障与标准体系
项目严格遵循IPC-J-STD-001H焊接工艺认证要求,构建"设备-方法-人员"三维质控体系。检测设备每季度进行NIST溯源校准,配备双激光干涉仪确保运动机构定位精度±2μm。方法验证采用DOE实验设计,建立包含12个关键因子的响应曲面模型。操作人员必须通过IPC-7711/7721认证,并定期进行显微焊点判读能力测试。值得关注的是,系统数据库已收录超过50万组焊接失效案例,形成最大的焊槽法缺陷特征库。
## 技术展望与发展建议
面向6G通信器件0.3mm间距焊接挑战,建议重点突破三项技术:开发亚微米级焊料润湿轨迹追踪系统,实现1000fps高速成像下的动态分析;建立多物理场耦合仿真模型,预测焊料冷却过程中的晶格畸变风险;推进检测设备与工业元宇宙的融合,构建虚拟焊接工艺验证平台。据中国电子技术标准化研究院预测,到2025年基于机器学习的可焊性预测系统将覆盖60%以上的SMT产线,推动电子制造业迈向零缺陷时代。
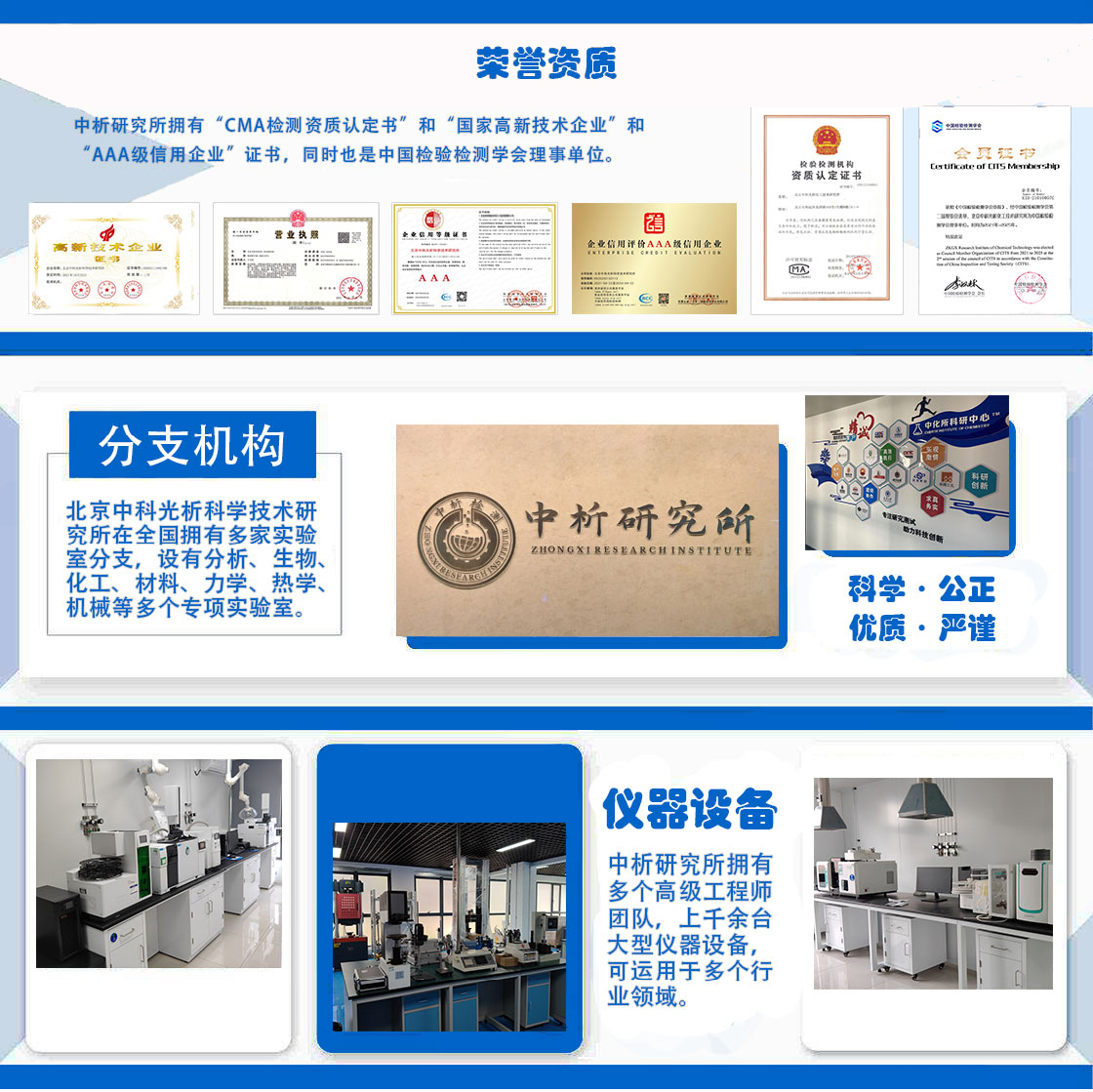
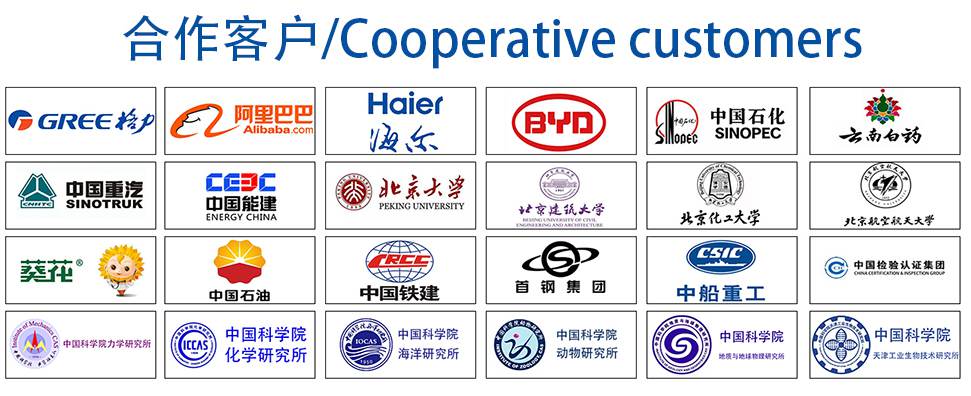
材料实验室
热门检测
推荐检测
联系电话
400-635-0567