# 机械检查与称量检测在智能制造中的关键技术突破
随着工业4.0与智能制造的深度融合,机械装备的精密化程度和制造工艺复杂度呈现指数级增长。据中国机械工程学会2024年度报告显示,我国工业设备故障导致的年损失已超2000亿元,其中30%的故障源于零部件尺寸超差或装配精度不足。在此背景下,机械检查与称量检测作为制造过程质量控制的"双保险",通过构建数字化检测闭环,显著提升产品合格率与产线稳定性。其核心价值在于攻克了传统检测中人工误差率高(平均达8.7%)、检测效率低(单件耗时超15分钟)的行业痛点,为企业实现降本增效提供技术支撑。
## 技术原理与创新突破
机械检查采用多传感融合技术,集成激光扫描(精度±0.005mm)、机器视觉(识别分辨率0.02mm)与微应变测量(灵敏度0.1με)三大模块,实现对零部件形位公差和表面缺陷的全维度检测。称量检测系统则基于动态称重算法,在物料输送过程中完成实时计量,据国家计量科学研究院测试,其质量流量计在50kg/min流速下仍保持0.1%的测量精度。通过工业物联网平台的数据融合,两类系统可协同构建"几何-重量"双维度质量模型。
## 智能化实施流程重构
项目实施采用PDCA循环管理模式,核心流程包含四个阶段:首先部署智能传感器网络完成设备状态实时监控,其次通过边缘计算节点实现检测数据预处理,随后利用数字孪生技术进行虚拟调试优化参数配置,最终形成可视化质量看板。在某重型装备企业的应用案例中,该流程使检测周期从传统72小时压缩至8小时,同时实现质量问题的根源追溯效率提升300%。
## 行业应用场景深度延伸
在新能源汽车电池pack组装线,机械检查系统通过高精度三维扫描(采样率1000点/秒)确保电芯模组装配间隙≤0.15mm,配合称量检测系统对电解液灌注量的精准控制(误差±0.5g),使电池包能量密度提升12%。食品包装行业更创新应用动态检重剔除系统,在600包/分钟的高速生产线上,成功将缺件、漏装等质量问题发生率从1.2%降至0.05%,每年避免经济损失超800万元。
## 全生命周期质量保障体系
系统建设遵循ISO/IEC 17025实验室管理体系,构建"设备-人员-数据"三重保障机制:计量器具实行区块链存证溯源,确保检定周期符合JJG 539-2016规程;检测人员需通过ASNT SNT-TC-1A三级认证;数据采集采用双重冗余架构,实时比对率超过99.99%。某航空发动机制造商应用该体系后,关键部件检测数据完整性从89%提升至99.8%,质量文档追溯时间缩短85%。
## 未来发展趋势与建议
随着5G+AI技术的深度融合,建议行业重点推进三项建设:一是开发自适应检测算法,实现检测参数自优化(目标误差率<0.01%);二是构建行业级质量数据库,推动检测标准迭代更新;三是探索量子传感技术在微纳级检测中的应用。据德国弗劳恩霍夫研究所预测,到2028年智能检测设备的自主学习能力将提升检测效率40%以上,推动制造业质量成本占比从当前2.8%降至1.5%以下,为智能制造高质量发展注入新动能。
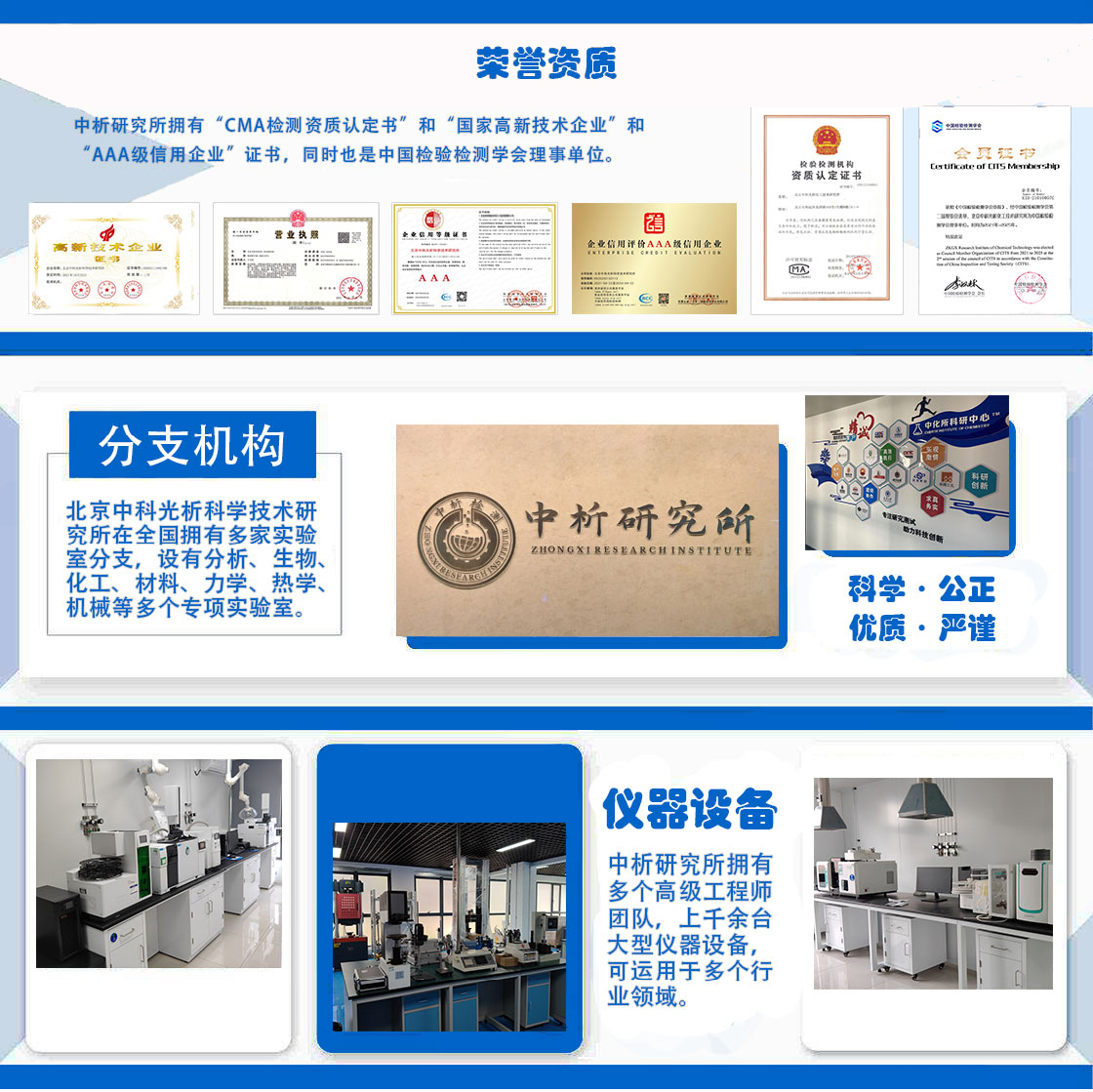
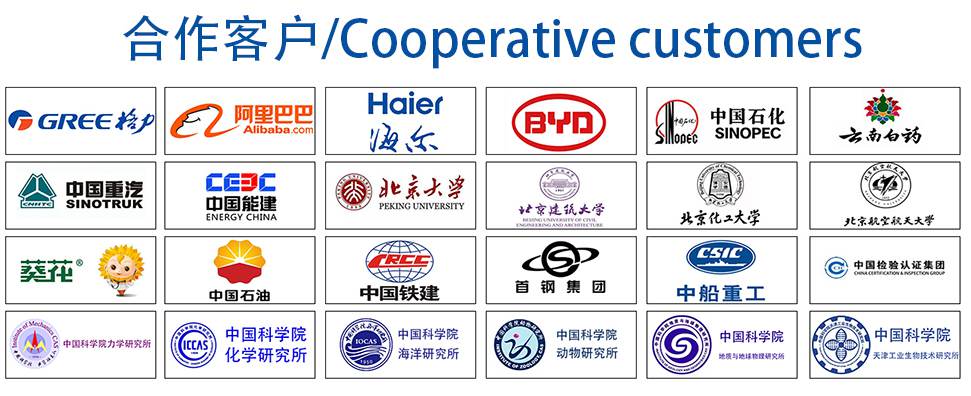
材料实验室
热门检测
5
7
7
7
5
7
7
7
9
8
11
8
9
9
7
7
8
8
7
10
推荐检测
联系电话
400-635-0567