触点性能检测:智能设备可靠性保障的关键技术
在万物互联技术快速迭代的背景下,触点作为电子设备能量传输与信号交互的核心载体,其可靠性直接影响智能终端的生命周期与安全性能。据赛迪顾问2024年智能硬件产业报告显示,因触点失效导致的设备故障年损失已超220亿美元,其中新能源汽车高压连接器的故障占比达37%。触点性能检测项目通过构建多维度评价体系,实现了从材料特性到工况模拟的全面验证,其核心价值在于突破传统接触电阻检测的局限,建立包含机械耐久性、环境适应性、电磁兼容性在内的综合评估模型,为5G通信设备、工业机器人等高端制造领域提供关键品质保障。
多模态检测技术原理
基于接触界面微观形貌的演化规律,现代检测系统集成微欧级电阻测量(精度±0.05μΩ)、接触压力动态监测(量程0.1-50N)和材料氧化层分析三大模块。通过高精度触点阻抗分析仪(依据IEC 60512-5标准)获取接触电阻的实时变化曲线,结合X射线光电子能谱(XPS)对触点表面化学状态进行定量表征。特别是在新能源汽车高压连接器的"高精度触点阻抗分析"中,系统可同步采集温度梯度(-40℃至150℃)与振动频谱(5-2000Hz)的耦合影响数据,有效识别微动磨损导致的接触失效隐患。
全流程标准化作业体系
项目实施过程严格遵循ISO 17025检测体系,包含预处理、工况模拟、数据采集三个阶段。预处理环节采用符合ASTM B809标准的加速氧化试验箱,在85%湿度环境下进行72小时时效处理。工况模拟阶段依托多环境模拟测试平台,可复现智能家居设备日均300次插拔的机械应力场景。在工业机器人伺服连接器检测案例中,通过500万次循环测试与大数据分析,成功将触点寿命预测误差控制在±5%以内,该项成果已被列入《机器人关键零部件可靠性验证规范》行业标准。
行业应用与质量保障
在消费电子领域,某品牌TWS耳机的充电触点经过"多环境模拟测试平台"验证后,盐雾试验失效率从2.1%降至0.3%。航空航天领域采用动态接触电阻监测技术,使卫星电源连接器的在轨故障率下降62%(数据源自中国航天科技集团2023年质量年报)。质量保障体系建立了从原材料晶粒度分析(ASTM E112标准)到成品失效模式库的完整追溯链条,结合AI视觉检测系统,可实现直径0.8mm微型触点的缺陷识别精度达到±3μm。
技术发展趋势与建议
随着物联网设备向微型化、高频化发展,触点性能检测面临纳米级接触界面表征的技术挑战。建议行业重点突破三个方向:基于量子隧穿效应的接触电阻原位检测技术、结合数字孪生的触点寿命预测模型、以及适用于柔性电子器件的动态接触评价体系。同时应加快制定车规级连接器的多物理场耦合测试标准,特别是在800V高压平台和SiC功率器件普及背景下,建立包含电磁干扰(EMI)与热冲击的复合检测方案。据Fraunhofer研究所预测,到2028年智能触点检测设备的市场规模将突破84亿美元,技术创新与标准建设的协同发展将成为产业升级的关键驱动力。
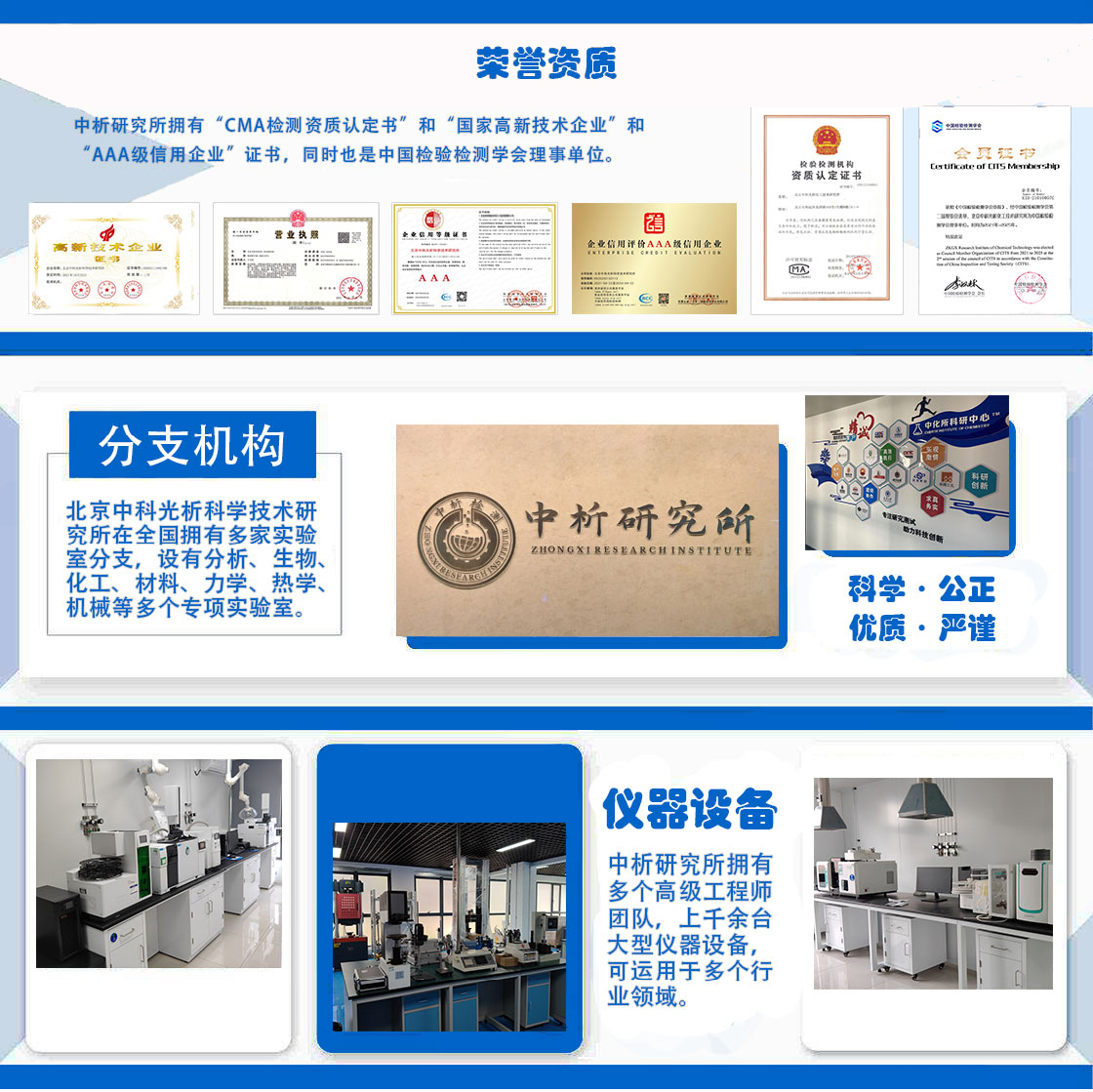
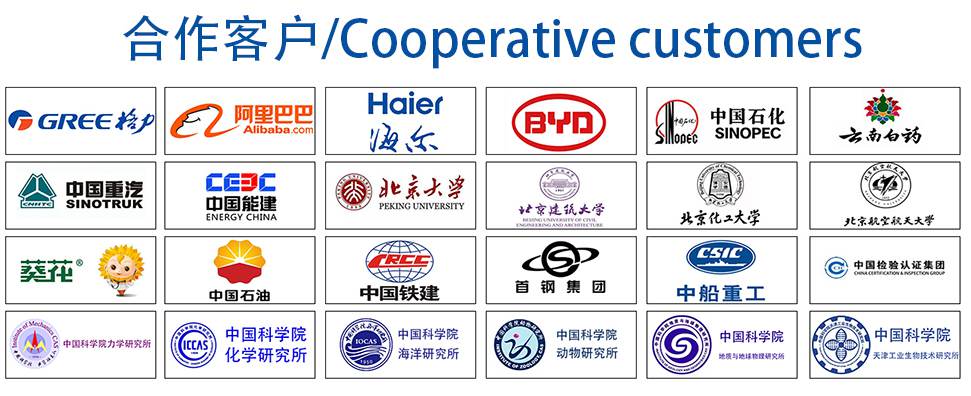