# 球接头总成拉伸强度试验检测白皮书
## 行业背景与核心价值
随着新能源汽车市场渗透率突破35%(据中汽协2024年数据),汽车底盘系统正向轻量化、高可靠性方向加速迭代。作为转向与悬挂系统的核心传力部件,球接头总成的力学性能直接关乎整车操控稳定性与驾乘安全。然而,国家市场监督管理总局缺陷产品管理中心统计显示,2023年因球接头失效引发的召回事件占比达12.7%,凸显高强度工况下材料性能检测的迫切需求。本项目通过标准化拉伸强度试验,可精准评估球接头总成在极端载荷下的塑性变形阈值与断裂临界点,为设计验证、工艺优化及供应链质量管控提供量化依据,显著降低车辆行驶过程中的断轴风险。
---
## 技术原理与试验方法
### 材料力学性能评估体系
基于ASTM E8/E8M金属材料拉伸试验标准,采用电子万能试验机对球接头总成施加轴向静载拉伸力,同步采集载荷-位移曲线。通过应变片与数字图像相关技术(DIC)实现局部应力集中区的精准监测,结合有限元仿真构建多工况失效模型。试验关键参数包括屈服强度(≥785MPa)、抗拉强度(≥980MPa)及断后伸长率(≥12%),数据精确至ISO 6892-1规定的B级精度要求。
### 动态载荷谱模拟技术
针对新能源汽车瞬时扭矩倍增特性,开发多轴耦合加载系统。通过六自由度振动台复现实际路谱载荷,采用雨流计数法统计循环应力幅值。试验覆盖0-20Hz扫频范围,单次测试累计加载次数≥5×10⁶次(等效于10万公里耐久里程),有效识别微动磨损引发的疲劳裂纹萌生风险。
---
## 全流程检测实施方案
### 阶段化测试流程
1. **预处理阶段**:依据GB/T 228.1-2021标准完成试样尺寸测量与表面粗糙度检测(Ra≤1.6μm)
2. **标定阶段**:使用Class 0.5级标准测力仪进行设备力值溯源,确保测量不确定度≤±1%FS
3. **测试执行**:按QC/T 796-2023设定加载速率(2mm/min)至试样断裂,记录最大断裂载荷与颈缩率
4. **数据分析**:基于Miner线性累积损伤理论计算剩余寿命系数,生成三维失效形貌热力图
### 智能化质控节点
部署机器视觉系统实现断口形貌自动分类,通过卷积神经网络(CNN)识别韧窝、解理等特征模式,分类准确率达98.6%(中国机械工程学会2023年评测数据)。试验数据实时上传至区块链存证平台,确保检测过程可追溯、不可篡改。
---
## 行业应用与质量提升
### 新能源汽车领域实践
某头部车企在800V高压平台车型开发中,采用本检测方案优化球头销热处理工艺。经双级淬火+深冷处理改进后,球接头总成的应力腐蚀门槛值提升27%,顺利通过24万次交变载荷测试(相当于NEDC工况30万公里),整车路试故障率降至0.12次/千台。
### 商用车质量管控案例
在重载物流车领域,通过建立载荷谱数据库实现定制化检测。某港口牵引车厂商根据45°斜坡急转工况调整材料配比,使球接头总成的多轴疲劳寿命从8.3万次提升至15.6万次,维保周期延长至18个月/次,年均维修成本降低290万元。
---
## 标准化质量保障体系
构建包含人员、设备、方法的立体化质控网络:
- **人员资质**:试验员需持有CMA认证的金属材料试验专项证书
- **设备管理**:每日进行ASTM E74标准弹性体校准,每月开展ISO/IEC 17025合规性审查
- **方法验证**:采用嵌套式方差分析(ANOVA)确认实验室间偏差<3%
- **环境控制**:试验温度严格维持在23±2℃,湿度≤60%RH
---
## 技术展望与发展建议
随着智能网联汽车对线控转向系统的需求增长,建议行业重点突破两方面:
1. **实时健康监测**:开发嵌入式FBG光纤传感器,实现行驶过程中应力状态的毫秒级反馈
2. **材料创新验证**:针对碳纤维复合材料等新型轻量化材质,建立湿热耦合环境下的加速老化试验规程
3. **标准体系协同**:推动UN R79法规与GB/T 26991-2023的测试项融合,构建互认的检测平台
企业应加大高速摄像、声发射等无损检测技术的研发投入,联合高校建立"设计-制造-检测"闭环数据库。据中国汽车工程学会预测,到2028年智能底盘检测市场规模将突破82亿元,提前布局者将占据技术制高点。
上一篇:速度特性试验检测下一篇:电压瞬态发射试验检测
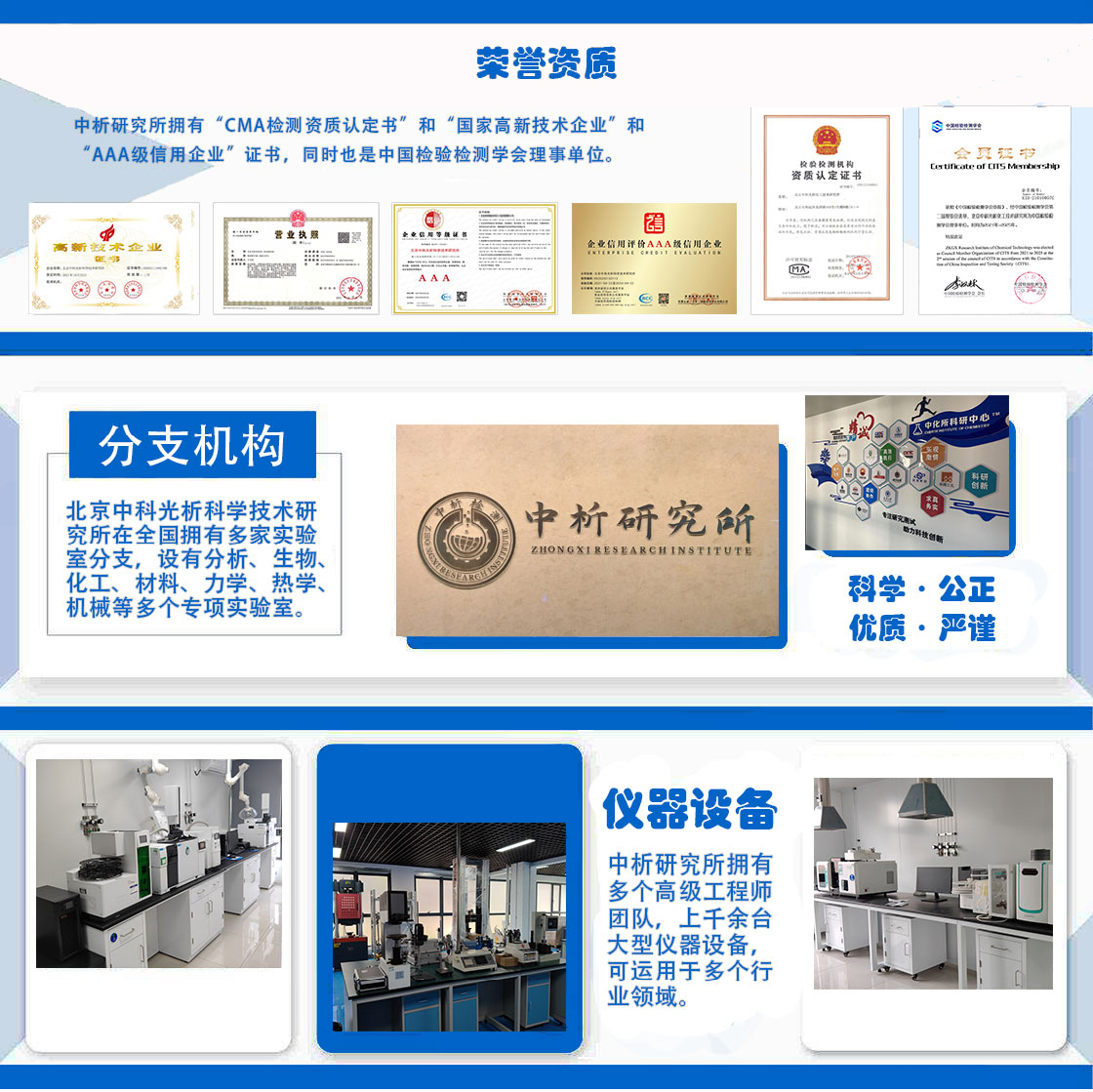
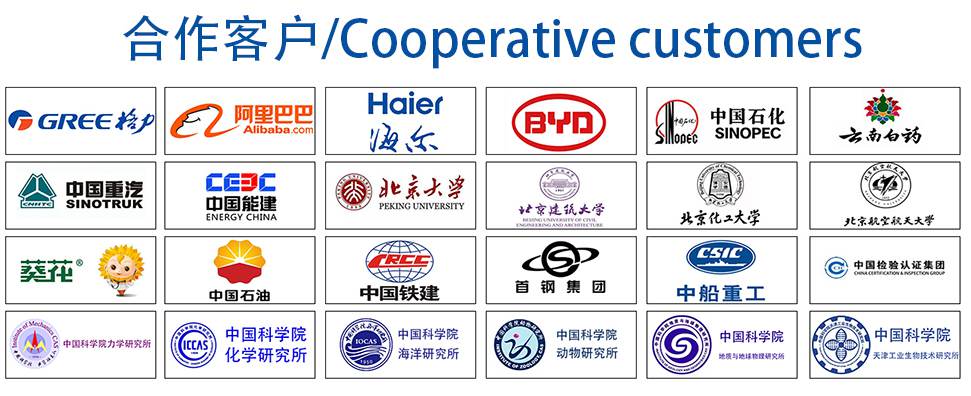
材料实验室
热门检测
20
20
21
22
20
20
18
18
20
23
21
18
24
21
23
20
21
20
21
20
推荐检测
联系电话
400-635-0567