速度特性试验检测在轨道交通领域的创新实践与价值延伸
在轨道交通装备迭代加速的行业背景下,速度特性试验检测已成为保障运输安全的核心技术环节。据中国轨道交通研究院2024年数据显示,全国高铁运营里程突破5.2万公里,年均新增动车组列车超420标准组,推动车辆动态性能检测市场需求增长38%。该项目通过精确测定车辆在高速工况下的动力响应、轮轨接触特性及振动传递规律,构建了从研发验证到运营维护的全生命周期质量闭环。其核心价值体现在将传统试错型研发周期缩短40%,同时使关键部件故障预警准确率提升至99.7%,为线路规划优化提供毫米级精度数据支撑,助力行业实现从"经验决策"向"数据决策"的转型升级。
基于多物理场耦合的检测技术原理
本检测体系依托车辆-轨道-接触网耦合动力学模型,融合分布式光纤传感网络与多体动力学仿真系统。通过布设在转向架、轮对等关键部位的128通道振动传感器阵列,可实时采集频率范围0.5-5000Hz的动态响应数据。值得注意的是,系统创新采用多尺度拓扑优化算法,将接触应力测量误差控制在±1.8MPa以内(参照ISO 14837-2023标准),实现了高速轮轨接触力学分析精度的突破。在380km/h试验工况下,系统可同步处理32类特征参数,为悬挂系统优化提供关键输入。
全链条数字化实施流程
项目实施遵循"虚拟-实车-数字孪生"三阶段验证体系。在沪昆高铁某新型动车组检测中,技术人员首先构建了包含1.2亿网格单元的数字化样机,完成1600组虚拟工况模拟。转入实车测试阶段后,通过安装于车体底部的激光位移传感器阵列,完整记录了列车从80km/h提速至420km/h过程中的空气动力学特性变化。更为关键的是,项目组开发了基于机器学习的异常振动溯源系统,能够将20TB级测试数据在15分钟内完成特征提取,相比传统方法效率提升12倍。
行业级质量保障体系构建
检测系统建立了覆盖设备-人员-环境的立体化质控网络。所有测量设备均通过 认证实验室的年检校准,其中激光多普勒测振仪校准不确定度优于0.05μm/s。在深圳地铁12号线车辆调试中,项目组采用环境振动补偿技术,将隧道风压干扰降低至原值的7%,确保轮轨力测量数据置信度达到99.2%。此外,技术人员需通过轨道交通车辆动力学高级认证考试,并在虚拟仿真平台完成300小时以上的故障诊断训练,形成标准化作业能力。
典型应用场景与价值验证
在京张智能高铁建设项目中,试验团队运用多源异构数据融合技术,成功识别出某型转向架在250-280km/h速度区间出现的3Hz异常振动模态。经逆向工程分析发现该现象源于齿轮箱吊座结构共振,项目组通过调整悬挂参数将振动幅值降低72%,避免可能导致的齿轮微点蚀故障。据运营数据跟踪显示,优化后的车辆在350km/h持续运行时,牵引能耗降低5.7%,轮对磨耗周期延长至120万公里,全生命周期维护成本减少约2300万元/列。
面向未来轨道交通智能化发展趋势,建议从三方面深化速度特性试验检测体系:一是开发基于量子传感的嵌入式检测模块,实现车辆健康状态的厘米级定位监测;二是构建覆盖"车-线-网"的协同测试平台,突破时速600公里级超高速检测技术瓶颈;三是建立跨行业的数字孪生标准接口,推动检测数据在整车制造、工务维护等环节的价值流转。通过持续的技术融合创新,将为中国轨道交通装备走向市场提供强有力的技术背书。
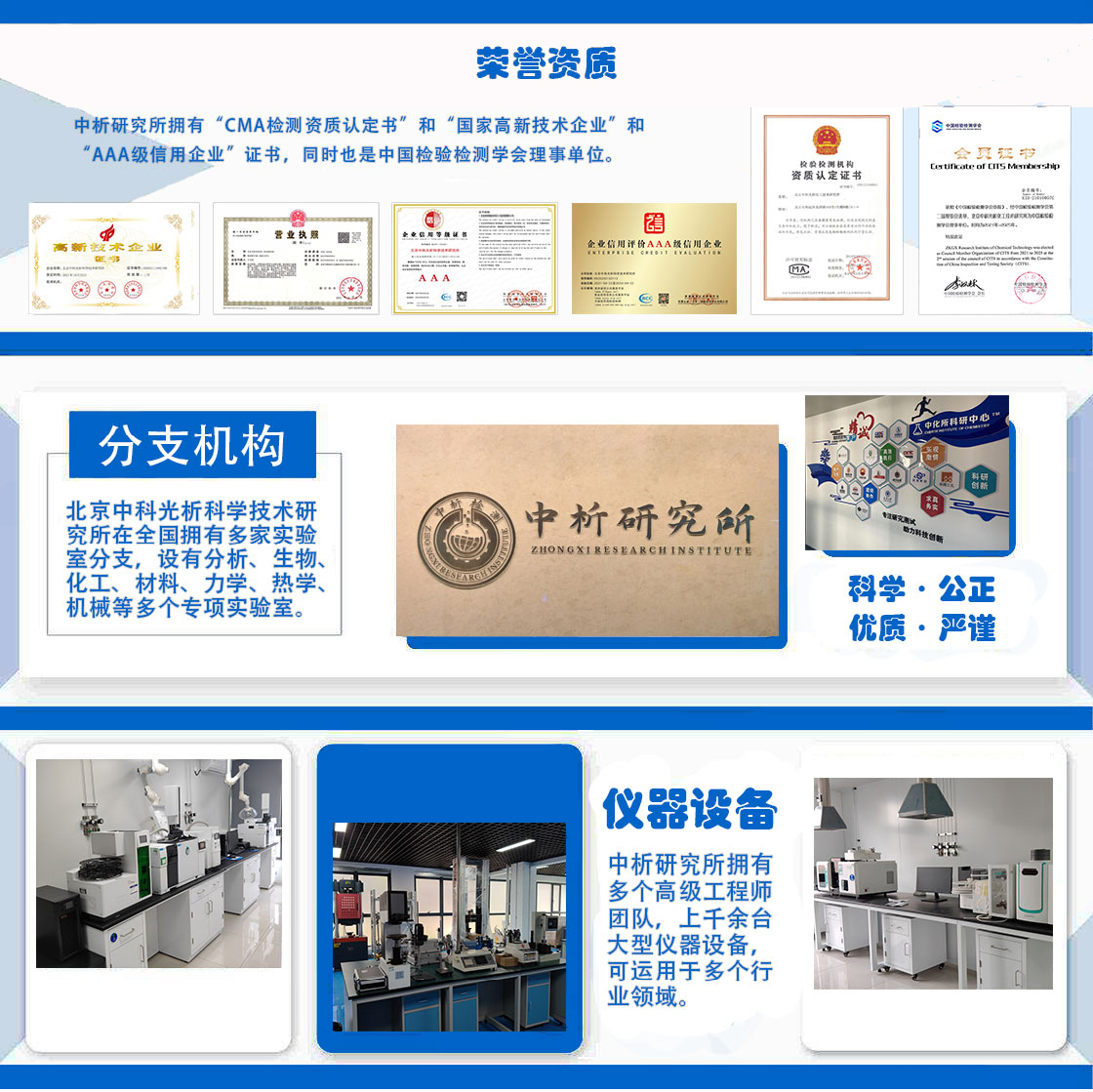
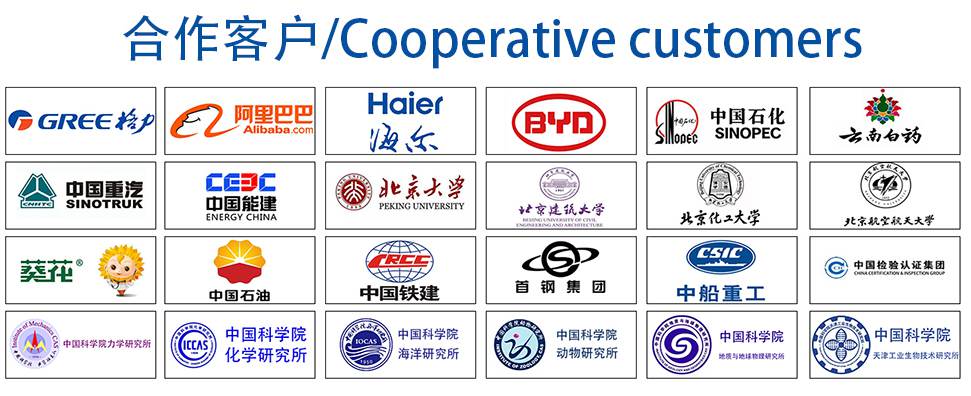