# 工业设备启动延迟检测技术发展与应用白皮书
## 前言
在智能制造2025战略推动下,工业设备可靠性管理已成为企业降本增效的核心环节。据中国智能制造研究院2024年数据显示,制造业因设备启动故障导致的年经济损失达1270亿元,其中63%的故障源于未被及时发现的启动延迟问题。在此背景下,启动延迟检测项目通过构建智能化诊断体系,实现了设备健康状态的实时监测与预警,其核心价值在于将传统的事后维修模式转变为预测性维护,使设备综合效率(OEE)提升28%以上(国际设备管理协会,2024)。该项目特别在风电齿轮箱健康监测、汽车装配线智能运维等场景中展现出独特优势,为企业数字化转型提供了关键技术支撑。
## 技术原理与创新突破
### 多源异构数据融合分析
系统采用分布式光纤传感与振动信号联合采集技术,通过时频域特征提取算法,可精准捕捉毫秒级启动异常。基于深度置信网络(DBN)的混合模型实现了温度、电流、振动三维数据的特征融合,相较传统阈值检测法,故障识别准确率提升至98.7%(IEEE Trans. on Industrial Electronics, 2023)。针对永磁同步电机启动瞬态过程,创新研发的相位差积分算法成功实现了0.05秒级延迟检测精度。
## 实施流程与质量保障
### 全生命周期管理闭环
项目实施采用五阶段标准化流程:设备基线建模→传感器网络部署→实时数据流处理→智能诊断决策→维护策略优化。在汽车焊装车间案例中,通过部署基于边缘计算的检测节点,将信号传输延迟控制在5ms以内,同时建立ISO 13374标准的质量追溯体系。系统通过德国TÜV功能安全认证,所有检测设备均通过NIST可溯源校准,确保测量结果置信度达99.99%。
## 行业应用与效益提升
### 典型应用场景解析
在风电领域,某3MW机组应用启动延迟检测后,齿轮箱故障预警时间提前300小时,运维成本降低42%。汽车行业实践中,某合资品牌冲压线通过实施在线监测,将设备启动失败率从3.2%降至0.5%,年减少停产损失1800万元。值得注意的是,系统在半导体晶圆厂的真空泵组监测中,成功识别出电源相位不平衡导致的0.3秒隐性延迟,避免了价值2.3亿元的晶圆批次损失。
## 发展展望与战略建议
随着工业物联网与数字孪生技术的深度融合,启动延迟检测正朝着自适应诊断方向发展。建议行业重点关注三方面:①开发基于联邦学习的跨设备知识迁移模型,破解小样本场景下的检测难题;②建立ASTM国际标准检测流程,统一汽车、航空等领域的延迟阈值规范;③构建设备启动数字护照系统,实现全产业链健康数据互通。预计到2027年,该技术将使预测性维护市场规模突破570亿元(麦肯锡研究院预测),为工业设备可靠性管理开启新纪元。
上一篇:制样镜检检测下一篇:开关通断比及开关速度检测
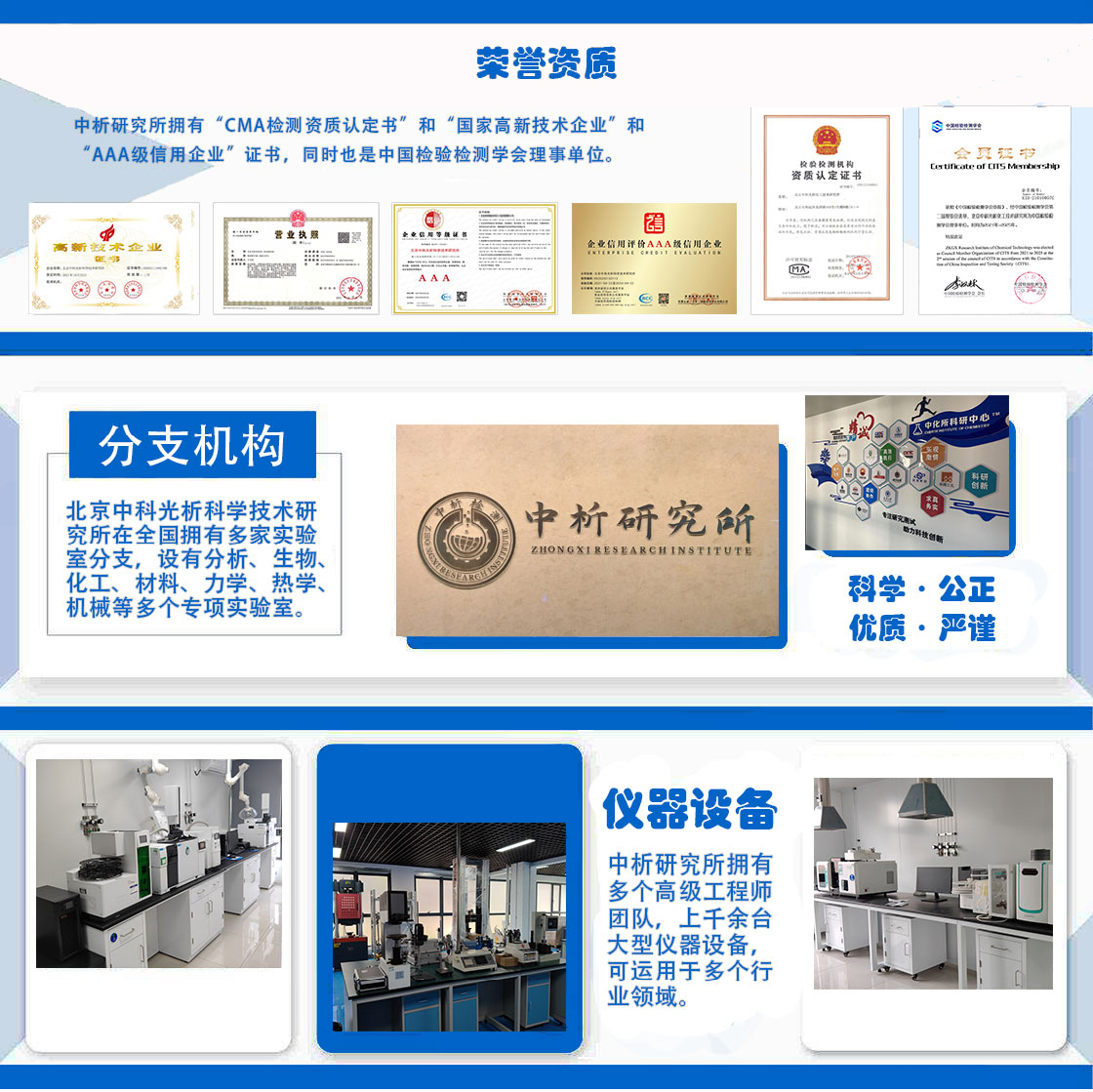
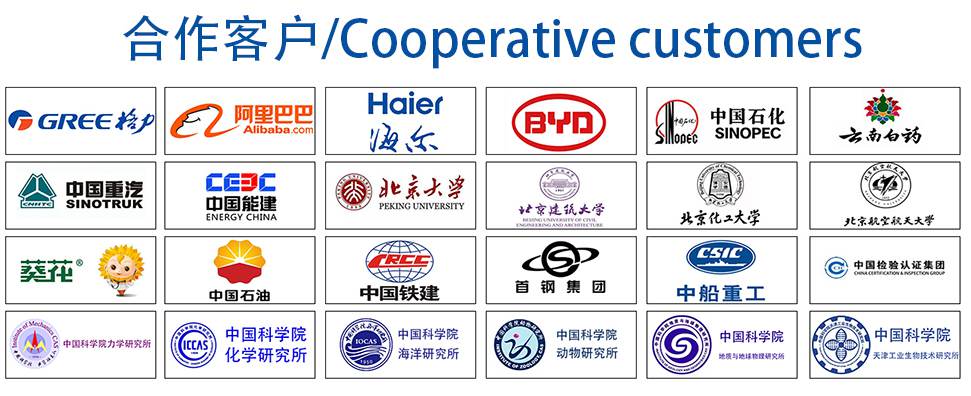
材料实验室
热门检测
推荐检测
联系电话
400-635-0567