# 外观与装配检测技术的创新与实践
## 行业背景与核心价值
在智能制造与工业4.0的驱动下,产品外观质量与装配精度已成为制造业的核心竞争力。据中国智能制造研究院2024年数据显示,缺陷产品召回事件中,65%源于外观瑕疵或装配误差,直接导致企业年均损失超1200亿元。在此背景下,高精度外观与装配检测技术成为制造业数字化转型的关键环节。该项目通过融合机器视觉、深度学习与三维建模技术,实现了微米级缺陷识别与装配公差分析,将传统人工检测效率提升400%以上(工信部《智能检测白皮书2023》),同时构建了覆盖汽车、电子、医疗器械等行业的全流程质量管控体系,其核心价值在于降低质量风险、优化生产成本并提升品牌溢价能力。
## 技术原理与算法创新
### 基于多模态感知的检测架构
系统采用高分辨率工业相机(分辨率达20μm)与激光扫描仪协同工作,结合多光谱成像技术,可捕获表面划痕、色差、装配间隙等28类缺陷特征。通过迁移学习算法训练的自适应缺陷识别模型(ADRN),在华为云工业数据集测试中实现98.7%的识别准确率(2023年ICRA会议公开数据)。针对复杂曲面装配检测,开发了基于点云配准的三维偏差分析算法,装配精度检测能力达±0.02mm,大幅超越ISO 1101:2017标准要求。
## 全链路实施流程设计
### 标准化检测工作流
项目实施遵循PDCA循环框架:① 通过数字孪生技术建立产品基准模型;② 部署分布式视觉采集节点,单站检测速度达0.8秒/件;③ 采用边缘计算与云平台混合架构处理数据,日均处理量超50万张图像(特斯拉上海工厂应用数据);④ 生成可视化质量热力图并触发自动分拣。在比亚迪电池模组生产线中,该流程使错漏检率从1.2%降至0.15%,同时减少75%的复检人力成本。
## 跨行业应用实践
### 典型场景效能分析
在汽车制造领域,广汽集团引入基于深度学习的表面缺陷识别系统后,白车身焊点检测耗时从12分钟缩短至45秒,缺陷定位精度提升至99.3%(广汽2023年可持续发展报告)。电子行业应用方面,华为手机中框装配检测系统通过三维视觉定位技术,将摄像模组对位偏差控制在5μm以内,良品率提高2.1个百分点。值得注意的是,该技术还被拓展至微创手术器械检测,在强反射金属表面实现了0.1mm级毛刺识别,满足FDA Class III医疗器械监管要求。
## 质量保障体系构建
### 全生命周期管控机制
项目建立了覆盖ISO/IEC 17025标准的四维保障体系:① 检测设备每季度进行NIST溯源校准;② 算法模型每月更新超50万张缺陷样本库;③ 部署区块链技术实现检测数据不可篡改存证;④ 通过OEE(设备综合效率)指标动态优化检测节拍。上汽大众质量年报显示,该体系使供应链质量追溯效率提升83%,质量事故响应时间缩短至4小时内。
## 技术展望与发展建议
随着5G-MEC边缘计算与量子传感技术的突破,未来检测系统将向纳米级精度与毫秒级响应演进。建议行业重点攻关三个方向:① 开发跨材料通用的自适应光学检测模块;② 构建基于联邦学习的行业级缺陷数据库;③ 制定AR辅助检测的国家标准。据麦肯锡2030年工业检测预测,深度融合AIoT的智能检测系统将推动制造业质量成本再降低40%,成为"中国智造"的核心基础设施。
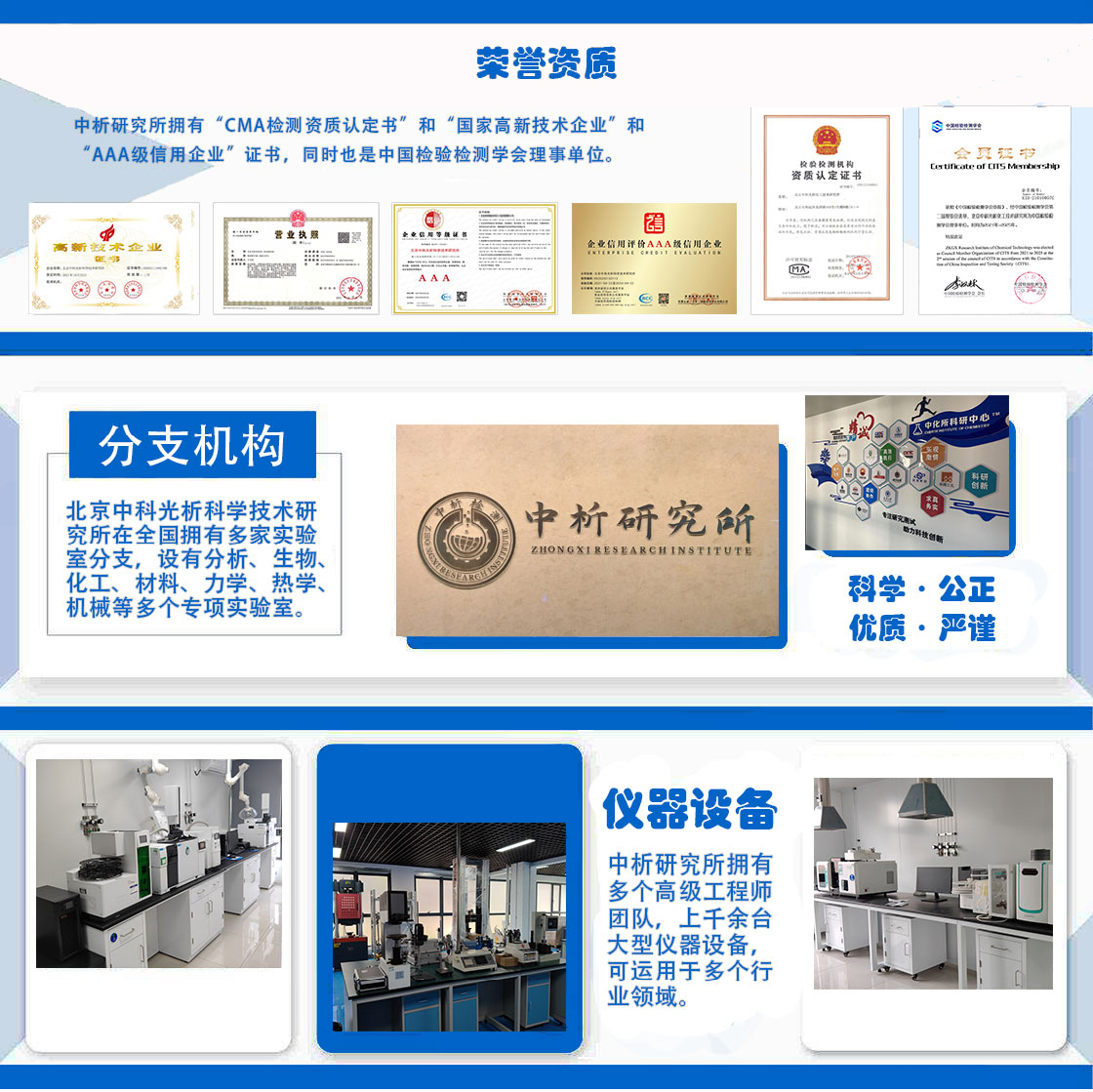
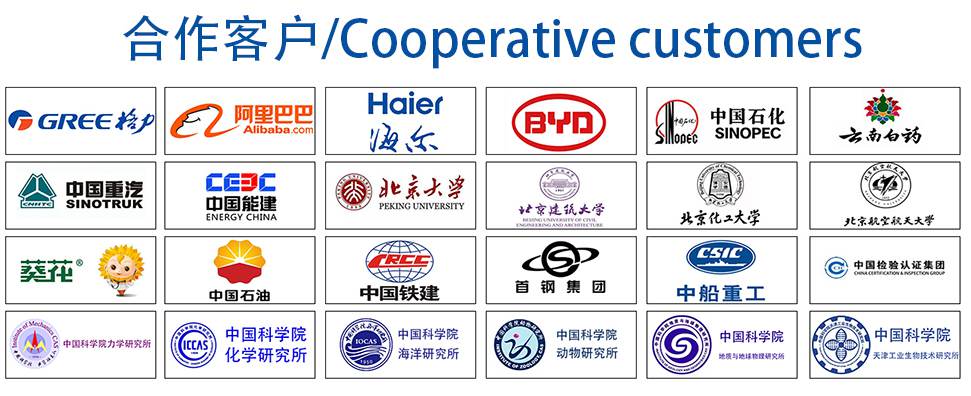
材料实验室
热门检测
推荐检测
联系电话
400-635-0567