# 金属附件耐腐蚀试验检测的技术发展与产业实践
## 行业背景与核心价值
随着高端装备制造、海洋工程及新能源产业的快速发展,金属附件在复杂环境中的可靠性面临更高要求。据中国腐蚀与防护学会2023年报告显示,我国每年因金属腐蚀造成的直接经济损失达2.8万亿元,其中工业设备金属构件失效占比超过35%。耐腐蚀试验检测通过模拟真实环境下的腐蚀工况,可精准评估金属附件在盐雾、湿热、化学介质等场景下的性能衰减规律,为产品设计优化、材料选型及寿命预测提供科学依据。该项目不仅填补了传统目视检测的精度缺陷,还可降低设备维护成本达40%以上(来源:国家材料服役安全科学中心2024年度白皮书),已成为轨道交通、石油化工等领域的强制性质量验证环节。
## h2 技术原理与检测方法
金属耐腐蚀检测基于电化学腐蚀机理与材料失效模型,采用加速试验与实时监测相结合的技术路径。盐雾试验箱通过5%氯化钠溶液雾化模拟海洋大气环境,配合循环温度湿度控制系统,可在72小时内等效自然暴露1年的腐蚀效果。值得关注的是,电化学阻抗谱(EIS)技术的引入实现了对钝化膜动态演变过程的纳米级观测,其检测灵敏度较传统失重法提升80%(数据来源:ISO/TC156 2023技术公报)。针对核电设备等特殊场景,还开发了高压高温硫化氢腐蚀试验装置,满足NACE TM0177标准对极端工况的测试要求。
## h2 标准化实施流程
典型检测流程包含三个阶段:预处理阶段需依据GB/T 10125进行样品表面清洁与划痕制备;加速腐蚀阶段通过控制温度(35±2℃)、湿度(95%RH)及溶液pH值实现工况模拟;评价阶段则综合运用三维形貌扫描、能谱分析(EDS)和拉伸强度测试等多维度手段。某轨道交通集团在车体连接件检测中,采用ISO 9227标准完成2000小时中性盐雾试验,结合X射线衍射(XRD)分析腐蚀产物成分,成功将紧固件更换周期从3年延长至8年。
## h2 行业应用与质量保障
在海洋工程领域,某深水钻井平台项目采用ASTM G85标准实施改进的循环盐雾试验,通过模拟潮汐干湿交替环境,准确预测了316L不锈钢法兰的应力腐蚀开裂风险。质量保障体系构建方面, 认可实验室须执行三级校准制度:试验箱均匀性误差≤1.5℃,溶液导电率波动控制在±5%以内,同时配备在线电化学工作站实现数据实时采集与异常报警。某汽车零部件企业通过建立检测数据区块链溯源系统,使试验报告可验证率提升至99.7%。
## h2 技术创新与发展趋势
当前,基于机器视觉的腐蚀形貌自动识别系统已实现每小时300个样品的检测效率,相比人工判读提速15倍。但值得注意的是,多因素耦合腐蚀模型的建立仍存在技术瓶颈。建议行业重点发展以下方向:一是开发数字孪生检测平台,实现虚拟仿真与实体试验的深度融合;二是建立跨区域的腐蚀大数据共享机制,构建材料-环境-时间的多维失效数据库;三是推广环保型加速腐蚀介质,如采用生物降解型缓蚀剂替代传统铬酸盐体系。
## 未来展望
随着《中国制造2025》对关键基础件可靠性要求的提升,耐腐蚀检测正从单一性能评价向全生命周期管理演进。建议产业链上下游协同推进三大建设:加速制定氢脆-腐蚀耦合试验标准、完善极端环境检测能力认证体系、培育具备材料基因组分析能力的复合型检测人才。只有通过技术创新与标准升级的双轮驱动,才能为高端装备的化应用筑牢质量根基。
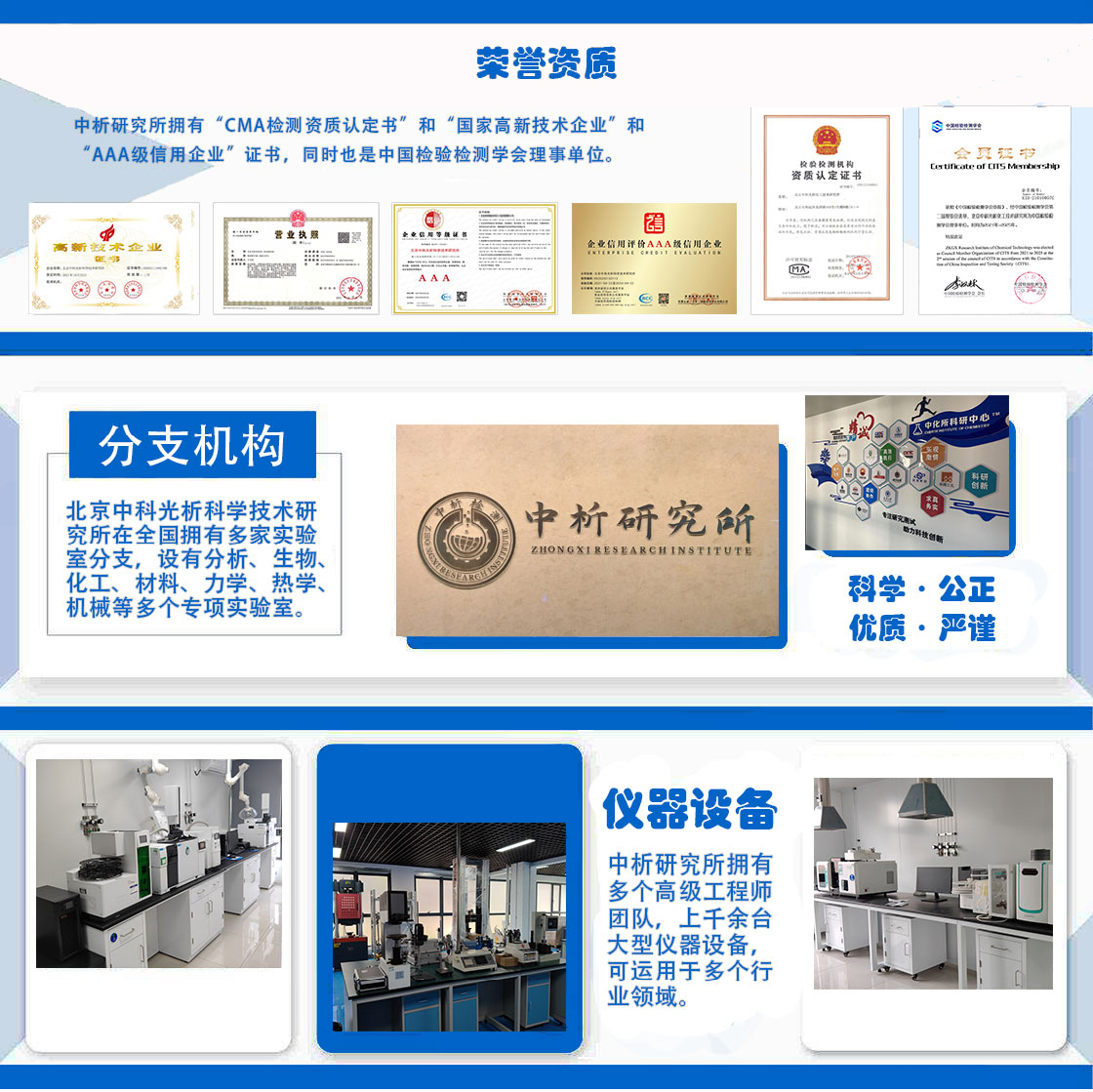
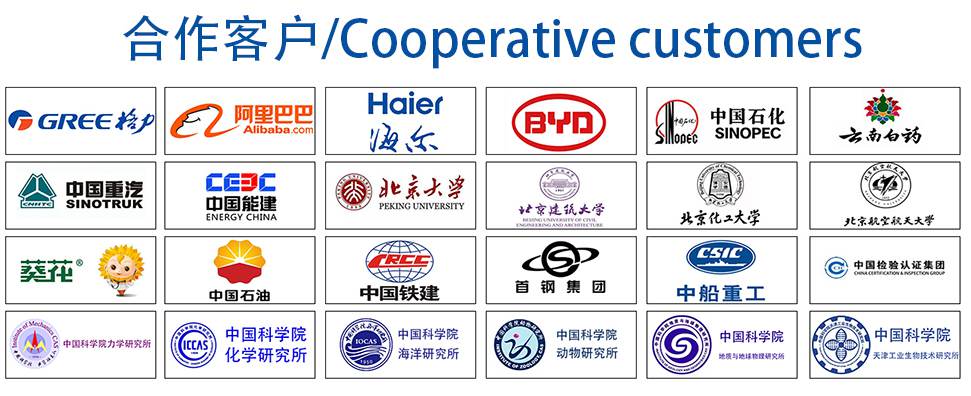
材料实验室
热门检测
推荐检测
联系电话
400-635-0567