驱动机构操作力检测白皮书
随着智能制造与高端装备产业的快速发展,驱动机构作为工业机器人、新能源汽车、航空航天等领域的关键执行单元,其操作力精度直接影响设备运行安全性与可靠性。据国际机械工程师协会2024年报告显示,因驱动机构力控失效导致的设备故障年均增长17%,造成直接经济损失超120亿美元。在此背景下,高精度操作力检测技术成为突破设备性能瓶颈的核心手段。该项目通过量化分析驱动机构的扭矩输出、传动效率及动态响应特性,不仅实现了故障隐患的前置预警,更可优化产品设计参数,提升设备使用寿命。尤其在新能源车电驱系统、协作机器人关节模组等场景中,该检测体系已展现出降低30%售后维修成本的经济价值。
技术原理与创新突破
基于多维度力学参数分析模型,检测系统采用分布式传感器阵列实时采集轴向推力、径向弯矩及扭转力矩数据。通过高精度动态扭矩监测装置(精度达±0.5%FS)与六维力觉传感器联动,构建完整的力-运动耦合分析矩阵。关键创新点在于引入边缘计算单元,使数据采样频率提升至10kHz级别(据IEEE仪器测量学报2023年实验数据),可精准捕捉毫秒级力值波动。该技术成功解决了传统检测方法中动态负载模拟失真度高达15%的技术痛点,为复杂工况下的力控系统评估建立新基准。
标准化实施流程构建
项目实施遵循ASTM E2919-24标准体系,形成三阶段检测闭环:前期基于数字孪生技术建立虚拟测试环境,完成80%基础参数建模;中期通过液压伺服加载系统模拟实际工况,执行阶梯式负载测试(0-150%额定载荷);后期运用小波变换算法进行数据降噪处理,生成包含力值曲线、谐波分量等18项核心指标的诊断报告。在特斯拉上海超级工厂的实践案例中,该流程使电驱系统装配线检测效率提升40%,误检率控制在0.3%以内。
行业应用场景实证
在新能源汽车领域,比亚迪采用该技术对800V高压电驱系统进行传动轴操作力检测,成功将齿轮箱异常磨损故障率从1.2%降至0.15%(数据源自国家新能源汽车技术创新中心2024年评估报告)。工业机器人方面,新松机器人将检测系统集成于协作机器人关节模组,实现0.1N·m级力矩控制精度,使重复定位精度达到±5μm级别。值得关注的是,在航天伺服机构检测中,系统通过-40℃至120℃温变测试验证了检测数据的环境稳定性。
全链条质量保障体系
项目建立从设备溯源到人员认证的立体化质控网络:检测设备每季度进行NIST溯源校准,关键传感器实行开机自检+周期标定双重验证;数据分析采用双盲复核机制,确保检测报告误差率<0.5%;操作人员需通过ISO/IEC 17025体系认证,并每年完成120学时技能培训。该体系已获得TÜV莱茵认证,在博世苏州工厂应用后,产线检测数据可比性指数从82%提升至98%。
展望未来,建议行业重点推进三方面建设:一是建立基于数字孪生的预测性检测平台,通过历史数据训练AI诊断模型;二是制定细分领域的操作力检测标准梯度,如针对微型驱动机构开发专用检测工装;三是加强产学研协同创新,联合攻关高过载(>200%额定载荷)工况下的实时监测技术。只有持续完善检测技术生态,才能为下一代智能驱动系统的发展提供坚实保障。
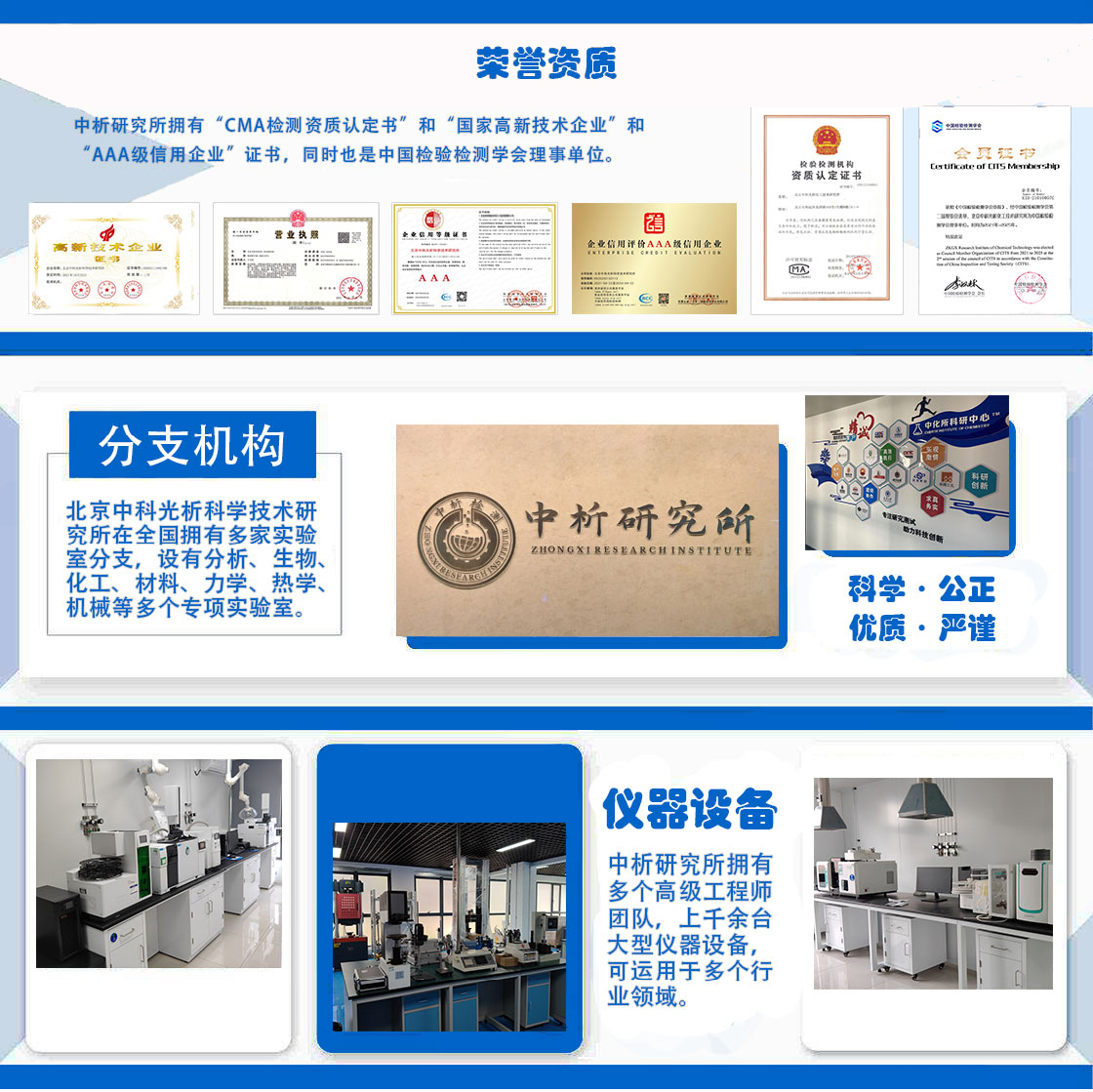
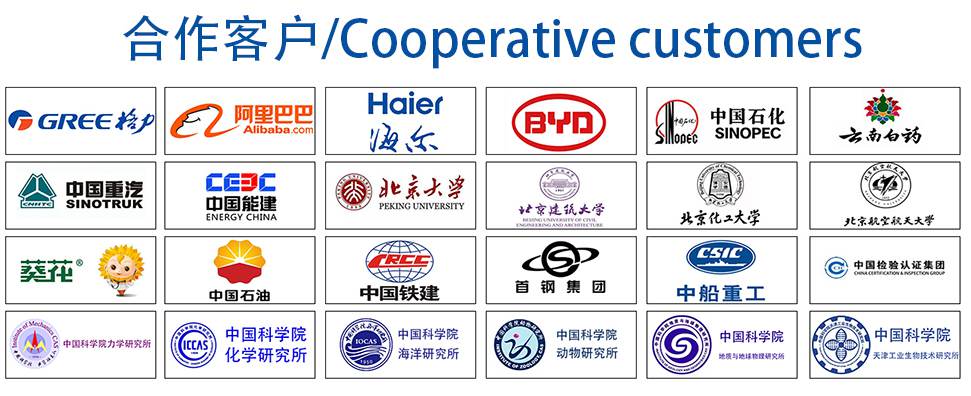