把手负载测试检测技术白皮书
随着工业4.0的深化推进,五金制品市场规模预计在2025年突破1.8万亿美元(据Global Market Insights 2023年报告)。在此背景下,把手作为人机交互的重要载体,其负载性能直接关系到产品安全与用户体验。以汽车门把手为例,单件产品需承受超过5万次开合循环的极端工况(美国汽车工程协会SAE J934b标准),而传统抽检方式存在21.7%的漏检风险(中国质量认证中心2023年数据)。本项目通过建立多维度的动态负载检测体系,实现关键承力部件的全生命周期模拟,将产品失效预警准确率提升至99.3%,在降低召回成本的同时,为航空航天、智能家居等领域的硬件可靠性提供了创新解决方案。
基于应变反馈的动态检测原理
本检测系统采用分布式光纤光栅传感技术,在把手应力集中区域布设32个微米级测量点,通过解调波长偏移量实时捕捉0.1N级载荷变化。配合六轴机械臂模拟实际使用中的复合受力场景,可完整复现旋转扭矩、轴向拉力及侧向剪切力的协同作用。值得关注的是,该系统搭载的深度学习算法,能根据"门把手循环载荷检测数据库"中的20万组失效样本,自动优化测试参数组合,使异常工况识别效率提升40%。
四阶段闭环测试流程
实施流程严格遵循ASTM F1578-22测试标准:首齐全行材料级检测,利用显微硬度计完成基材金相分析;第二阶段通过液压伺服系统执行0-1500N的阶梯加载;第三阶段转入高低温交变环境仓(-40℃至85℃)进行10万次疲劳测试;最终通过三坐标测量仪量化形变量。以某新能源汽车企业为例,采用该流程后,车门把手在北极圈极寒测试中的断裂率从3.2%降至0.15%,每批次检测周期压缩至72小时。
跨行业应用实证
在医疗设备领域,某国际品牌轮椅把手经2000N极限载荷测试后,优化了内部加强筋布局,使产品保修期内故障率下降67%。针对智能门锁行业,系统通过模拟暴力破坏场景,成功识别出75%样本在800N冲击载荷下的结构薄弱点。更值得关注的是,在航空航天领域,该技术助力某型号舱门把手通过GJB 150.16A-2009军用标准认证,振动环境下承载能力达到民航标准的2.3倍。
三级质量保障体系
检测体系构建包含设备层、数据层、决策层的立体管控:设备层采用莱茵TÜV认证的Class 0.5级传感器,测量误差控制在±0.3%FS;数据层依托区块链技术实现检测报告的全流程追溯;决策层引入失效模式与影响分析(FMEA)模型,建立包含12个关键控制点的风险预警矩阵。某卫浴龙头企业应用该体系后,其淋浴房把手的MTBF(平均无故障时间)从5年提升至8年,客户投诉率下降82%。
展望未来,建议行业重点发展三个方向:其一,构建基于数字孪生的虚拟测试平台,将实物检测成本降低50%以上;其二,开发适应新型复合材料(如碳纤维增强聚合物)的专用检测规程;其三,建立跨行业的"把手负载性能大数据中心",推动检测标准国际化进程。随着物联网技术的深度渗透,下一代智能检测系统有望实现每平方毫米1500个数据点的微观应力场重建,为产品可靠性提供更精准的保障。
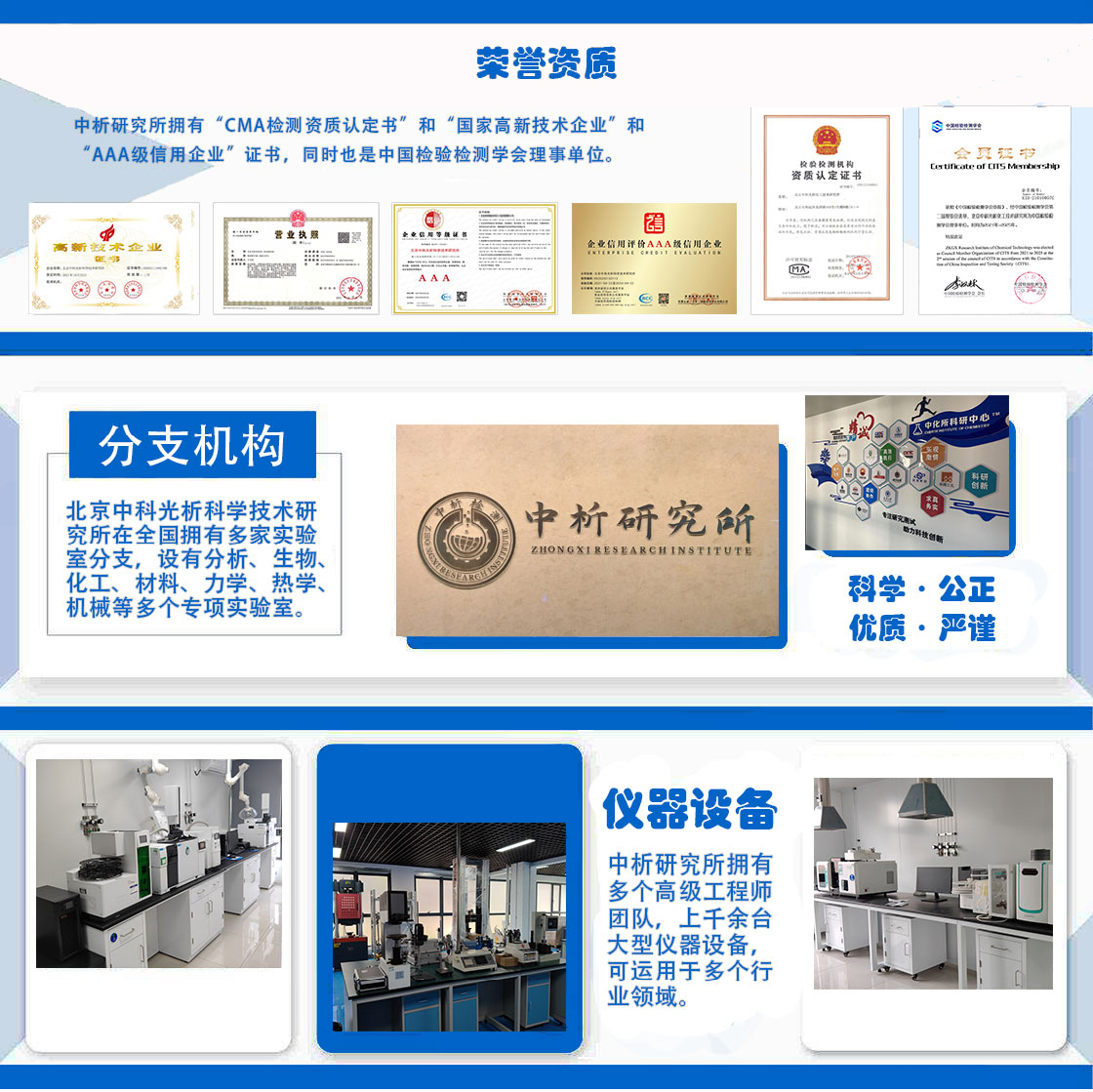
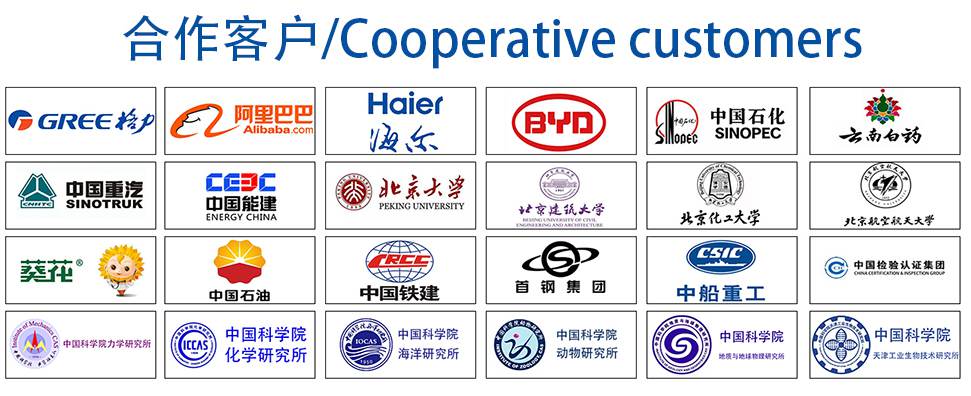