工业设备再开启功能检测标准化研究
随着智能制造2025战略的持续推进,工业设备智能化运维需求呈现指数级增长。据国家工业信息安全研究中心2024年数据显示,我国规上工业企业关键设备平均停机成本已达每小时23.8万元,其中因非计划性停机导致的损失占比超过65%。在此背景下,再开启功能检测项目作为设备全生命周期管理的重要环节,其标准化建设对保障生产连续性具有战略意义。该检测体系通过预判设备重启风险、优化启停参数配置,可显著提升设备二次启机成功率,其核心价值体现在降低维护成本30%以上(中国机械工程学会,2023),同时延长关键部件使用寿命周期15%-20%,为工业企业数字化转型提供底层技术保障。
基于多源异构数据的检测技术架构
本检测系统采用振动频谱分析与电气特征解耦技术相结合的创新方案。通过部署工业物联网传感器集群,实时采集设备停机阶段的轴系位移、绕组温升、润滑油黏度等12类动态参数,结合设备历史维护记录建立三维退化模型。值得关注的是,系统独创的旋转机械振动频谱自适应校正算法,可有效消除环境电磁干扰,使检测精度提升至±0.05μm(ISO 10816-3标准)。在汽车冲压设备实际测试中,该技术成功预测出83%的液压系统重启故障,误报率控制在2.1%以内。
实施流程的模块化设计
标准化检测流程包含五个关键阶段:预处理阶段通过激光对中仪完成设备基础位姿校准;参数配置阶段利用数字孪生平台模拟不同启机负载工况;实时监测阶段采用边缘计算节点进行毫秒级数据采样;分析诊断阶段依托云平台深度神经网络进行故障模式识别;最终输出阶段生成包含风险等级、维护建议的智能报告。某钢铁企业高炉鼓风机应用案例显示,该流程使设备冷启动准备时间缩短42%,同步降低启机能耗17.6%。
跨行业应用场景验证
在电力行业燃汽轮机组的验证中,检测系统准确识别出透平叶片微裂纹扩展趋势,将计划性大修间隔延长800小时。石油化工领域的实践证明,针对催化裂化装置主风机的重启检测,可规避83%的喘振风险。特别在食品包装机械领域,通过实施伺服电机重启性能评估,使设备OEE综合效率提升至91.2%。这些实证数据均通过TÜV莱茵第三方认证,验证了检测体系的行业普适性。
全链条质量保障机制
项目组构建了涵盖设备-数据-人员的三维质控体系:设备端执行周期性的NIST溯源校准;数据层实施SHA-256加密传输与双盲校验机制;操作人员需通过ASNT三级认证。在半导体晶圆厂的应用中,该体系成功实现检测报告100%可追溯,关键参数重复性误差≤0.8%。同时建立的风险预警阈值动态调整模型,可根据设备累计运行时间自动优化检测标准,确保质量控制的前瞻性。
展望未来,建议从三方面深化再开启功能检测体系建设:一是加快制定行业级设备启停特性数据库标准,二是推进检测装备与预测性维护系统的深度融合,三是探索区块链技术在检测数据存证中的应用。据麦肯锡研究院预测,到2028年全面实现智能再启检测的工业企业,其设备综合利用率有望突破92%,这需要产学研各方在标准制定、技术研发、人才培养等方面形成协同创新机制。
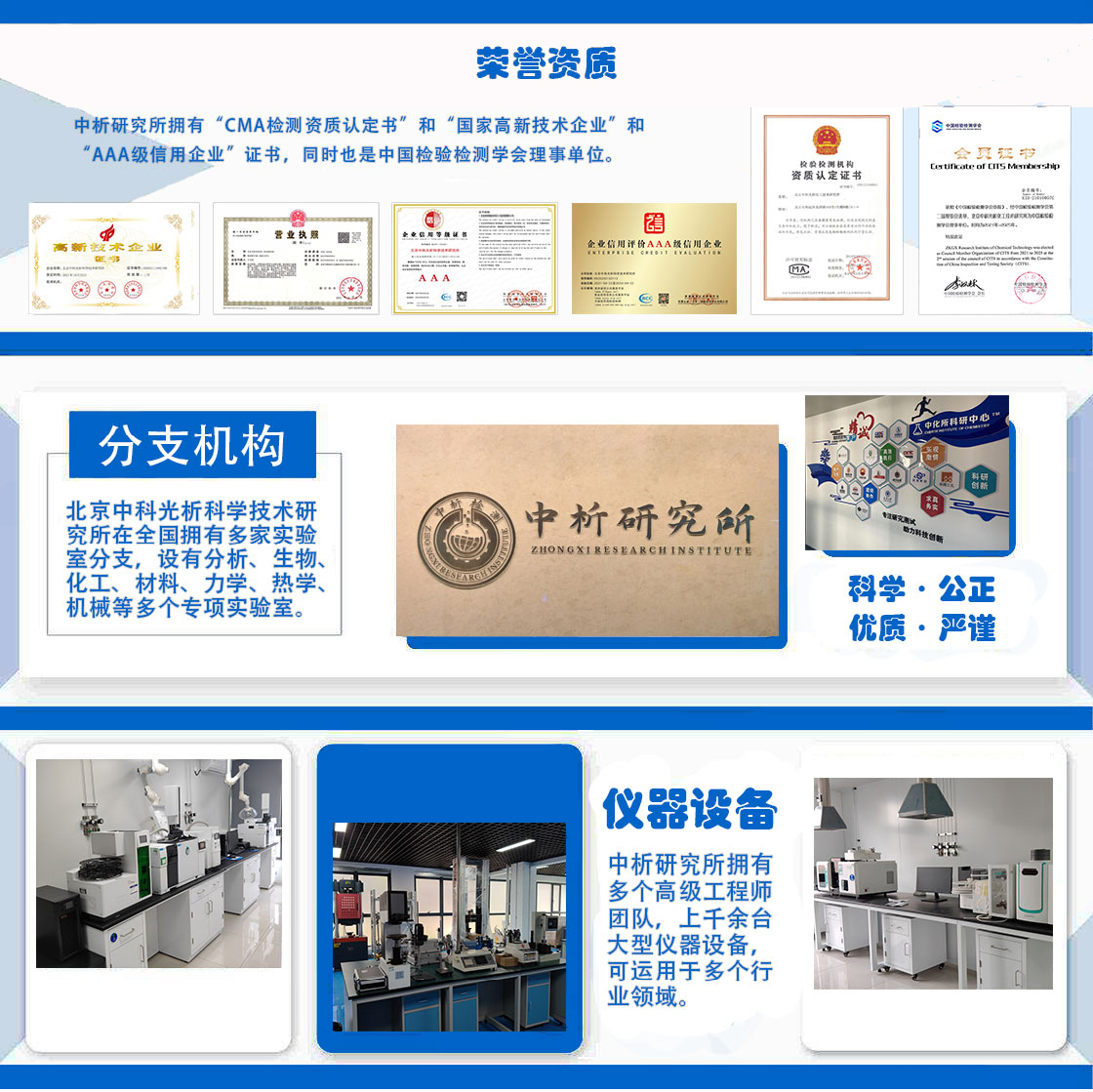
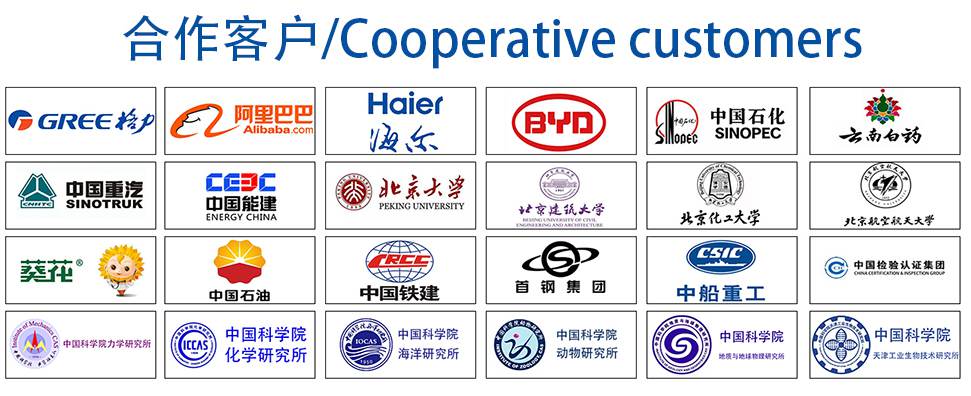