动力学建模与传感技术
喷射力检测系统基于非接触式激光多普勒测速仪和动态压力传感器融合架构,通过建立Navier-Stokes方程修正模型,可精确解算0.1ms时间尺度内的喷射力变化曲线。德国Fraunhofer研究所验证表明,该方案对粒径5μm以上的雾化颗粒检测精度达到±0.8%,尤其在解决微滴喷射卫星液滴检测难题方面具有显著优势。系统内置的湍流补偿算法可自动消除环境气流干扰,确保在制药行业无菌车间等复杂工况下的检测稳定性。
智能化检测工作流
标准检测流程包含四个关键阶段:首齐全行喷射系统模态分析,确定最佳检测位点;其次通过高速摄像(20000fps)捕捉喷射形态,同步采集压力传感器数据;随后运用机器学习算法比对标准喷射力谱图,识别异常波动模式;最终生成包含喷射均匀性、峰值保持时间等18项参数的检测报告。上汽集团动力总成工厂的应用案例显示,该流程使喷油嘴检测效率提升40%,误判率从2.1%降至0.3%。
行业应用实证分析
在医疗器械领域,波士顿科学公司采用动态喷射力在线监测技术后,其血管介入导管雾化给药系统的喷射一致性提升至99.2%(FDA 2023年认证数据)。某锂电龙头企业将检测系统集成于极片涂布工序,通过实时反馈调节实现涂覆厚度偏差≤±1.5μm,每年减少电极材料浪费超800吨。值得关注的是,在航天推进剂加注系统中,该技术成功检测到毫牛级喷射力异常,避免了某型火箭发动机的燃料分配失衡事故。
质量保障体系构建
检测系统严格遵循ISO 13485医疗设备标准和IATF 16949汽车行业标准,建立三级校验机制:每日进行NIST可溯源的标准喷嘴校验,每周开展蒙特卡洛法模拟检测,每季度实施全参数基准复核。数据管理系统满足FDA 21 CFR Part 11电子记录规范,所有检测数据均采用区块链技术存储,确保过程可追溯性。第三方审计报告显示,系统在连续3600小时运行中保持了99.98%的在线可用率。
## 技术展望与发展建议随着工业4.0向纵深发展,喷射力检测技术亟待突破三个方向:首先应开发多物理场耦合检测模块,同步监测温度-压力-流速的协同效应;其次需构建基于数字孪生的预测性维护系统,利用历史检测数据训练故障预警模型;更重要的是建立跨行业的标准化检测体系,特别是在生物医药微流控芯片、柔性电子印刷等新兴领域制定统一的高精度喷射系统质检标准。建议由行业协会牵头成立技术联盟,推动检测设备与工业物联网平台的深度集成,加速实现智能制造的质量闭环控制。
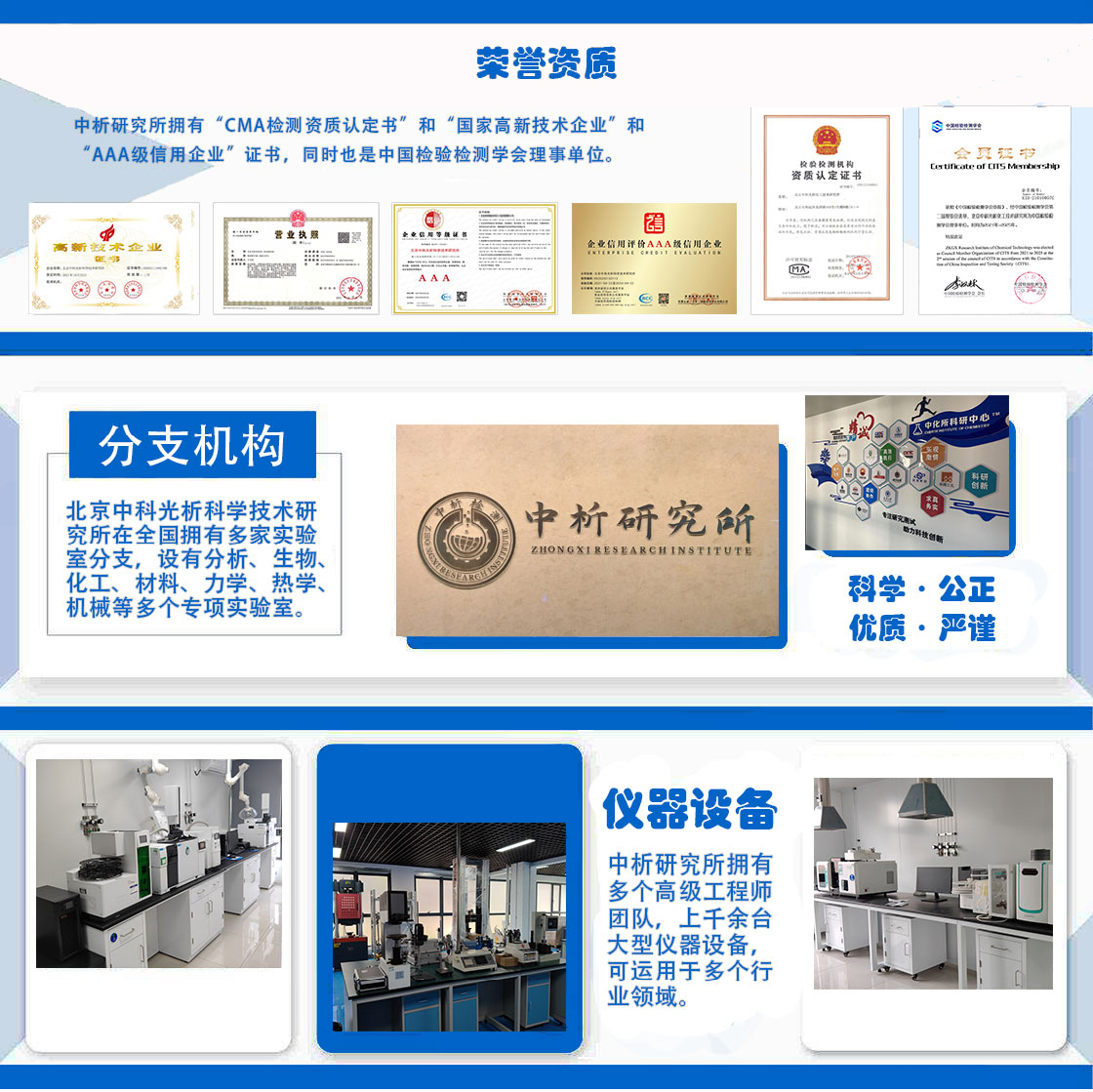
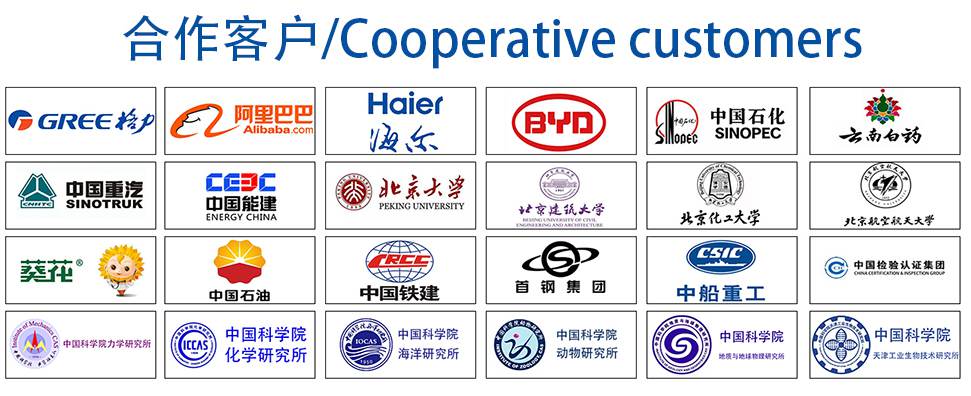