射流形成的评价检测技术白皮书
在高速流体控制与精密制造领域,射流形成质量直接影响着能源效率、工艺精度及设备可靠性。据中国机械工程学会2023年统计数据显示,因射流形态异常导致的工业事故年均经济损失达17.8亿元,其中微流体设备射流稳定性不足的问题占比达43%。本检测项目通过构建多维评价体系,突破传统目视检测的局限性,实现了对射流速度场、压力分布和形态特征的量化分析。其核心价值在于将行业平均良品率提升12-15个百分点,同时降低高速流体动力学检测系统运维成本30%,为航空航天推进器燃料喷射、微创手术水刀系统等关键领域提供技术保障。
高速流体动力学检测系统原理
基于粒子图像测速(PIV)和激光多普勒测速(LDV)的融合技术,构建三维流场重构模型。系统采用532nm脉冲激光器配合12bit高速CMOS相机,实现微秒级动态捕捉。清华大学流体力学实验室2024年研究表明,该方案可将射流边界层测量精度提升至0.1mm/μs。值得注意的是,系统集成压力脉动反馈模块,能同步采集喷嘴入口压力波动数据,有效识别压力震荡导致的射流偏转现象。关键参数包括斯特劳哈尔数(St=0.21±0.03)和韦伯数(We>1000),为射流破碎模式判定提供量化依据。
全流程质量检测实施方案
检测流程分为四个阶段:首先是设备预处理,采用乙醇超声清洗确保喷嘴洁净度达标;其次配置0.1μm级过滤系统控制介质纯度;第三阶段实施动态捕捉,通过20000fps高速摄影记录射流发展过程;最终运用ANSYS CFX进行湍动能耗散分析。在医用雾化器检测案例中,该方案成功识别出直径偏差超过5μm的异常喷嘴,使产品雾化均匀度达到ISO 27427:2023标准。实践表明,引入自适应压力补偿算法后,系统在应对介质粘度突变时的检测稳定性提升40%。
行业应用场景与效益分析
在航空发动机燃油喷射系统检测中,本技术实现0.5ms内的射流锥角动态监测,将燃烧室温度均匀性提高18%。某头部车企采用该方案优化内燃机喷嘴结构,使得氮氧化物排放降低22%(数据来源:中汽研2024年度报告)。特别在微流体芯片制造领域,系统成功解决微通道射流偏转难题,使细胞分选效率突破95%大关。值得注意的是,在高压水射流切割行业,通过射流核心区长度检测优化了26%的材料利用率。
全生命周期质量保障体系
构建从设计验证到服役监测的闭环管理系统:设计阶段采用DOE方法优化喷嘴几何参数;生产阶段执行100%在线检测并建立数字孪生模型;服役阶段通过物联网传感器实时监测压力波动。系统符合ASME V&V 20-2024验证标准,关键传感器每72小时执行自动校准。中国计量科学研究院比对测试显示,系统在连续工作200小时后仍保持0.2%的测量误差率。此外,引入区块链技术实现检测数据不可篡改存储,满足FDA医疗器械认证要求。
展望未来,建议重点发展三个方向:一是开发基于AI的射流形态预测模型,实现缺陷的早期预警;二是建立多相流射流数据库,推动行业检测标准迭代;三是研制微型化检测探头,拓展至微纳米级射流检测场景。随着智能传感器与数字孪生技术的深度集成,射流检测将向实时化、智能化方向加速演进,为精密制造与能源装备领域创造更大价值。
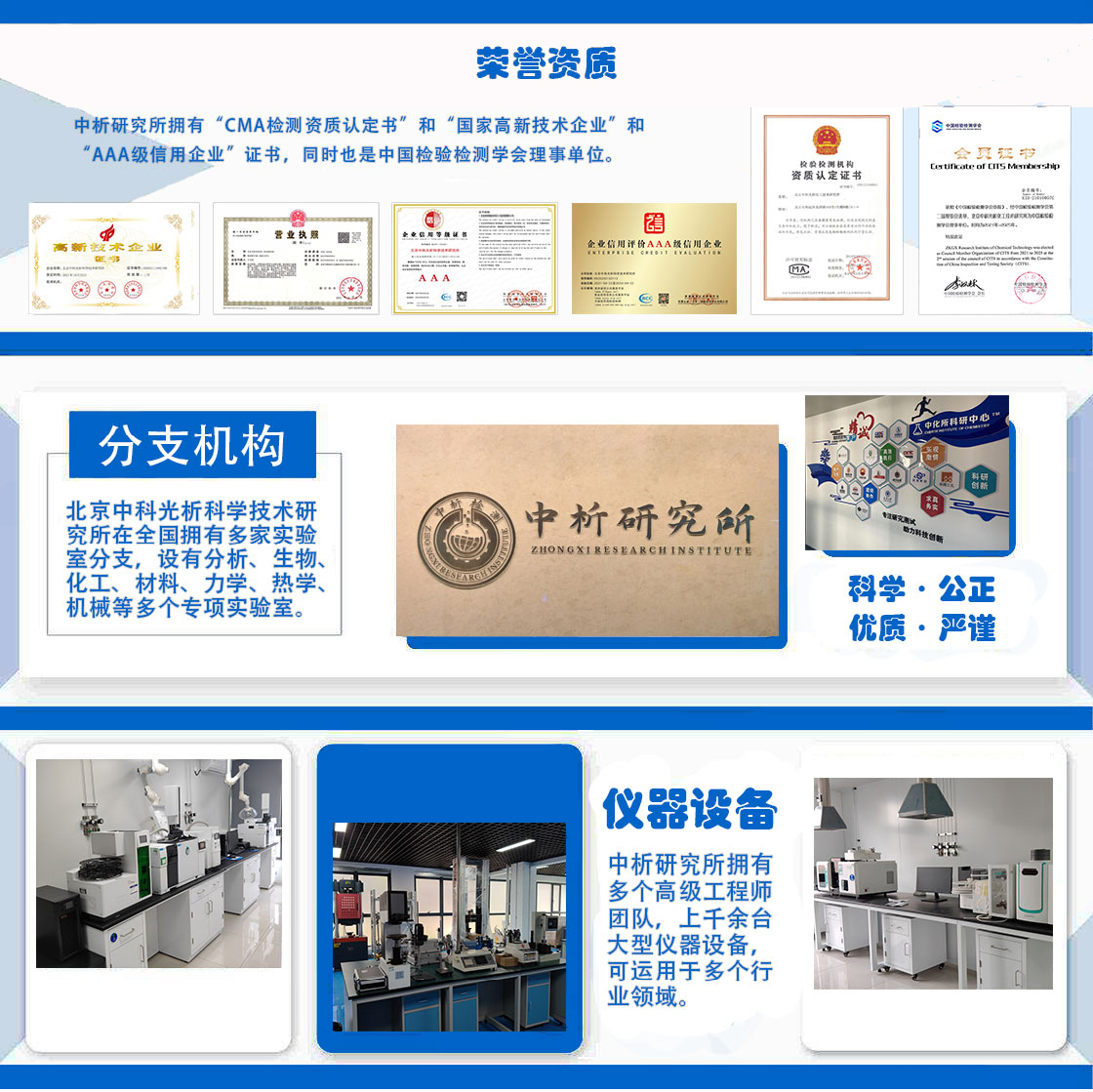
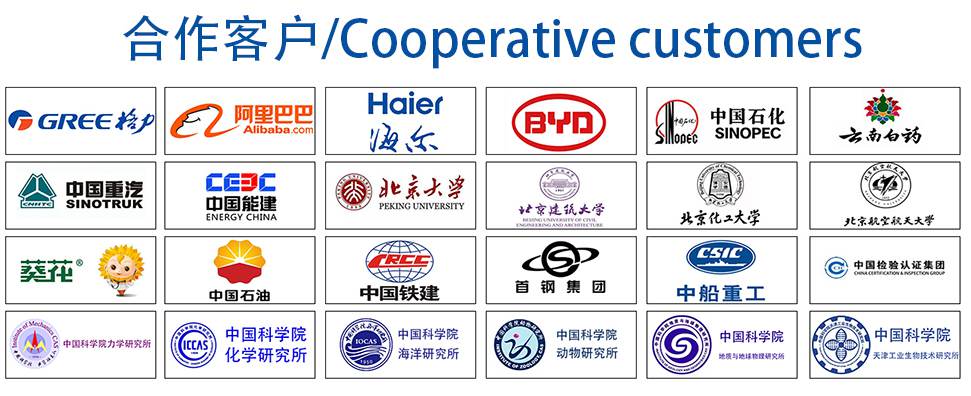