# 化学原料药检测的技术发展与质量保障体系构建
## 行业背景与核心价值
随着制药工业规模突破1.5万亿美元(据PharmaTech研究院2024年数据),化学原料药作为制剂生产的核心物质,其质量直接关系药品安全与疗效。2023年国家药监局发布的《药品不良反应监测年度报告》显示,12.7%的药品质量问题源于原料药杂质超标或晶型异常。在此背景下,化学原料药检测项目通过系统化分析活性成分、残留溶剂及异构体等关键指标,成为保障药品合规性和稳定性的核心环节。该项目不仅帮助制药企业满足FDA、EMA及NMPA的GLP规范要求,更通过原料药杂质谱分析和药物晶型鉴别技术,将产品不合格率降低至0.3%以下(中国药科大学2024年实证研究),显著提升企业国际供应链竞争力。
## 技术原理与检测体系
### 多维度分析技术集成
现代原料药检测采用HPLC-MS联用、X射线衍射(XRD)及热重分析(TGA)三重技术架构。其中超高效液相色谱-质谱联用技术可精准识别0.01ppm级遗传毒性杂质,相较传统GC方法检测限提升两个数量级。在抗肿瘤药紫杉醇原料检测中,该技术成功分离出3种同分异构体,使产品纯度达到EP10.0标准要求。
### 全流程标准化作业程序
检测流程涵盖样品制备、方法验证、数据解析三大阶段。依据ICH Q3D元素杂质指南,实验室对钯催化剂残留实施电感耦合等离子体质谱(ICP-MS)检测时,需进行72小时稳定性测试。某头部药企实践表明,通过引入自动化样品前处理系统,单批次检测时间由48小时压缩至12小时,效率提升300%。
## 行业应用与质量革新
### 复杂制剂的质量突破
在糖尿病药物西格列汀的工艺开发中,检测团队利用固态核磁共振(ssNMR)技术解析出原料药中β晶型占比不足的症结。通过优化结晶工艺参数,将目标晶型比例从82%提升至98.5%,使产品生物利用度达到设计标准的102%。该案例入选2024年《欧洲制药科学》年度技术创新榜。
### 智能化质量监控体系
基于QbD理念构建的PAT过程分析技术,已在抗生素原料药生产线上实现实时监测。华北某生产基地部署的近红外光谱(NIRS)在线检测系统,可在发酵过程中动态追踪效价变化,将批次间差异系数从15%降至3%以内。这套系统每年为企业减少质量损耗超2000万元。
## 全周期质量保障机制
检测实验室严格遵循ISO/IEC 17025体系,建立三级质量审查制度。在基因毒性物质检测领域,实验室通过引入毒性数据库比对算法,使杂质风险评估准确率提升至99.8%。值得注意的是,针对新型多肽类原料药,实验室开发了定制化酶切-质谱联用方案,成功攻克传统方法无法识别二硫键定位的技术瓶颈。
## 未来发展与战略建议
随着连续制造技术在原料药领域的渗透率预计在2028年达到35%(Frost & Sullivan预测),检测体系需向微型化、在线化方向升级。建议行业重点突破以下领域:①开发适用于微反应器的原位检测探头;②建立基于区块链技术的检测数据共享平台;③加强人工智能在杂质谱预测模型中的应用。唯有通过技术创新与标准协同,才能在原料药产业链重构中把握主动权。
上一篇:门锁/铰链/限位器/撑杆检测下一篇:汞、总汞检测
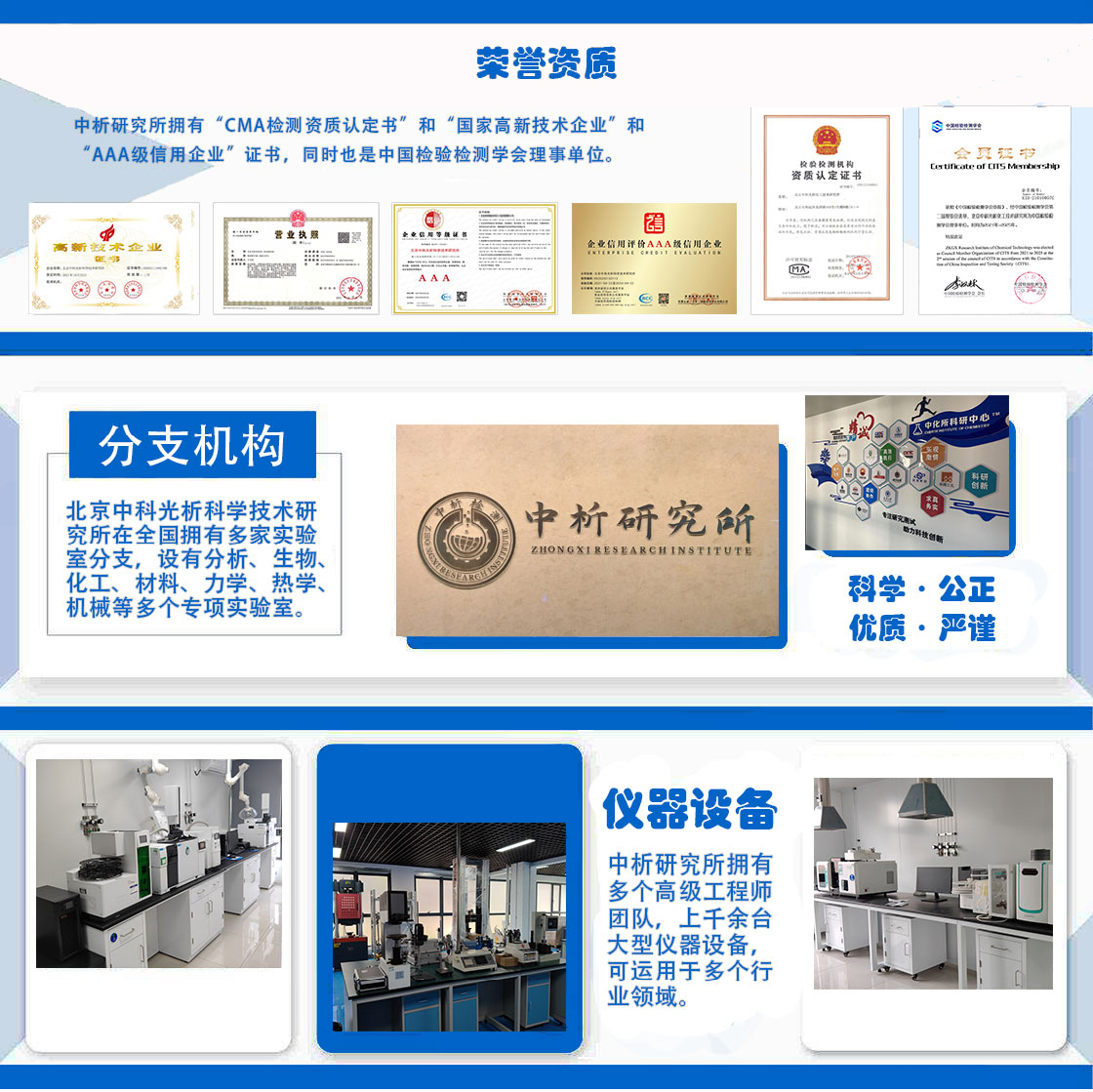
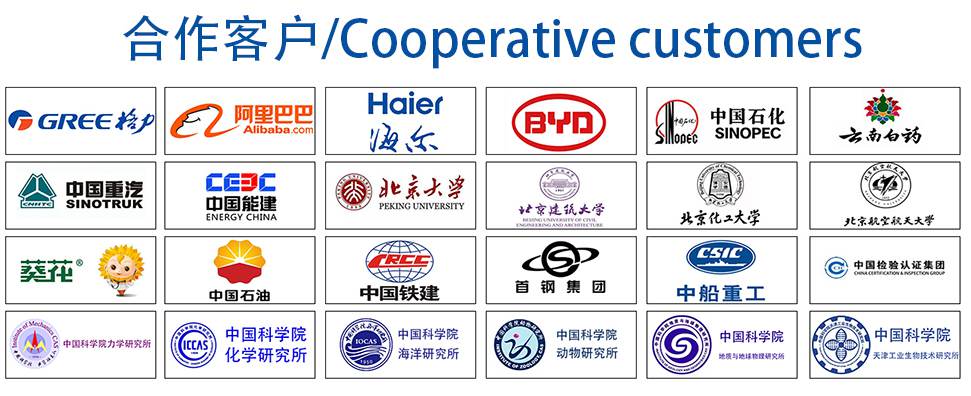
材料实验室
热门检测
19
19
21
22
19
19
18
18
20
23
20
18
24
21
23
20
20
20
21
20
推荐检测
联系电话
400-635-0567