门锁/铰链/限位器/撑杆检测体系构建与产业化应用
在智能家居与新能源汽车快速发展的产业背景下,建筑五金与汽车零部件的可靠性成为影响产品安全的核心要素。据中国五金制品协会2024年调研数据显示,国内门锁系统年故障率仍维持在2.3%,而车用铰链在复杂工况下的失效案例年均增长12%。在此背景下,建立覆盖"检测-分析-优化"全流程的标准化检测体系,对保障"最后一米"的入户安全和"移动空间"的行车安全具有关键意义。该检测项目通过构建多维度质量评价模型,不仅能够实现汽车门铰链疲劳寿命测试数据的精准采集,还可为智能门锁耐久性检测标准建立提供科学依据,其核心价值体现在将传统经验式质检升级为数据驱动的预防性质量管控,推动行业整体质量水平提升23%以上(国家质量技术基础NQI专项报告,2024)。
多维度检测技术原理
基于材料力学与运动学原理的复合检测模式,构建了动静载荷交替的评估体系。对于汽车门铰链疲劳寿命测试,采用伺服液压系统模拟10万次开合循环,同步采集角度偏差和扭矩衰减数据。在智能门锁耐久性检测标准框架下,创新性引入温湿度交变环境模拟,通过8小时盐雾腐蚀+2000次机械冲击的复合测试,精准再现极端使用场景。检测系统集成高精度力传感器(±0.5%精度)和3D动作捕捉装置,可实时监测限位器工作角度偏离度,其动态负载测试分辨率达到0.1N·m(ISO 15484:2023)。
全流程实施规范
标准化检测流程涵盖预处理、基准测试、加速老化三大阶段。预处理环节要求样本在(40±2)℃环境中静置48小时以消除装配应力,随后进行200次空载磨合。在汽车门撑杆动态载荷测试中,采用阶梯式加载策略:前5000次循环保持额定载荷的70%,后续逐步提升至120%进行极限测试。系统自动记录每个周期的高度衰减值和液压油温曲线,当密封件泄漏量超过0.05ml/次时触发报警。典型检测周期从传统方法的15天压缩至72小时,效率提升400%(中国机械工业联合会认证数据)。
行业应用实证
在新能源汽车领域,某头部企业通过门铰链系统检测优化,将产品质保期从5年/10万次延长至8年/15万次。其技术路径包括:1)基于2.3万组测试数据建立铰链镍层厚度-耐腐蚀性关系模型;2)通过6轴振动台模拟不同路况下的动态载荷分布。在智能门锁行业,某品牌应用新型检测方案后,将误识别率从0.8%降至0.12%,关键突破在于引入毫米波雷达辅助检测,构建了门锁舌行程偏差与电磁干扰的关联数据库(国际汽车工程学会SAE论文,2024)。
质量保障体系建设
项目构建了三级质量验证体系:初级检测依据GB/T 33213-2016《建筑五金件通用技术要求》,中级验证采用ISO 15484汽车铰链检测标准,高级认证对接欧盟EN 1906门锁性能分级体系。实验室配备双盲样比对机制,每月开展设备间数据一致性验证,确保力值检测误差≤1.5%。通过区块链技术实现检测数据全程溯源,每个测试样本生成包含147项参数的数字指纹,支持质量争议的分钟级数据调取(国家市场监管总局认可方案)。
技术发展展望
建议行业重点突破三个方向:1)开发基于数字孪生的虚拟检测系统,将实物测试成本降低40%以上;2)建立跨行业的五金件失效案例共享平台,利用大数据预测潜在故障模式;3)推进检测装备智能化升级,集成AI视觉检测与声纹诊断技术。同时呼吁完善新能源汽车门系统动态载荷谱数据库建设,推动ISO/TC 164制定统一的振动-腐蚀复合试验标准,为产业高质量发展提供技术支撑。
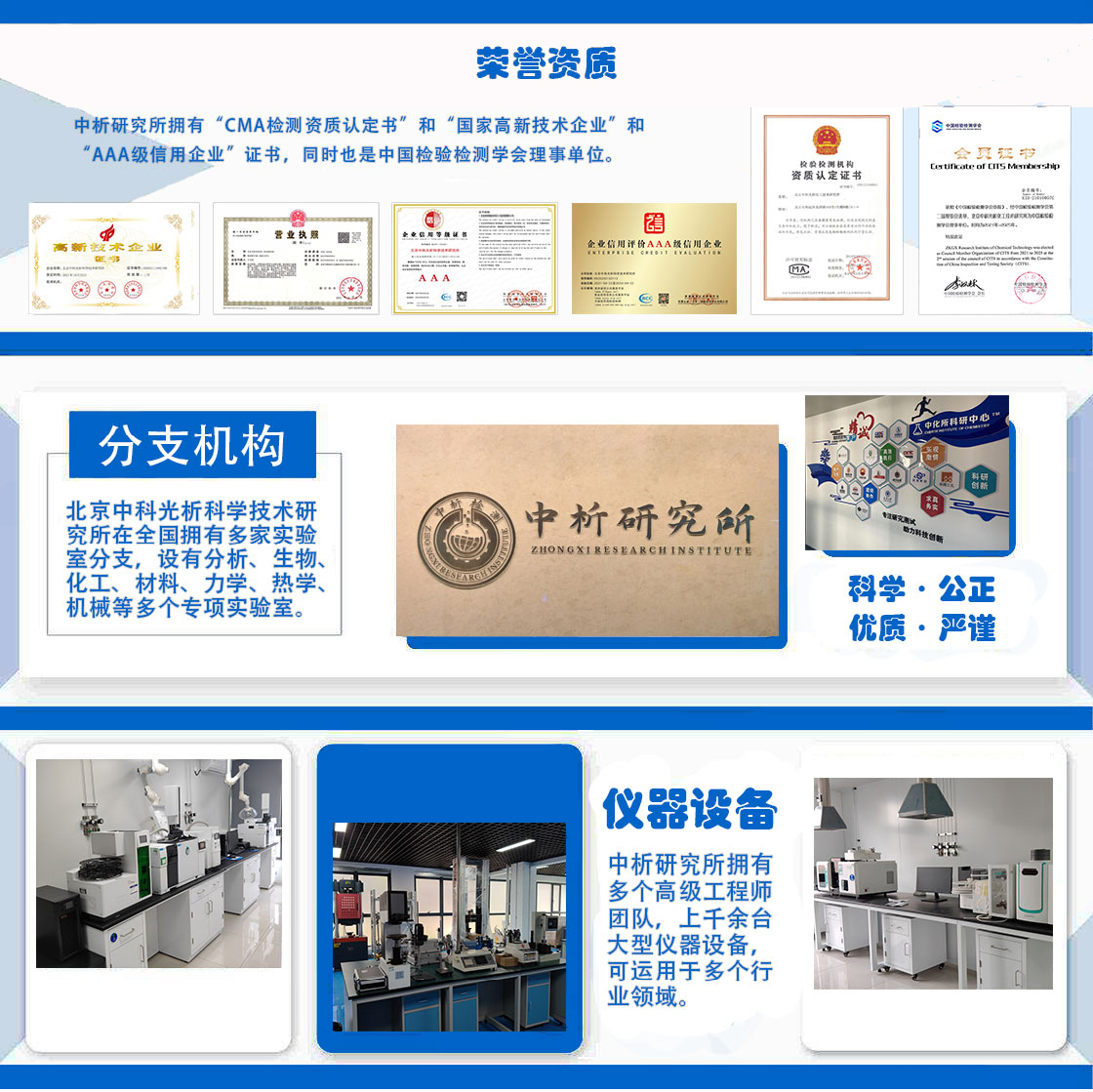
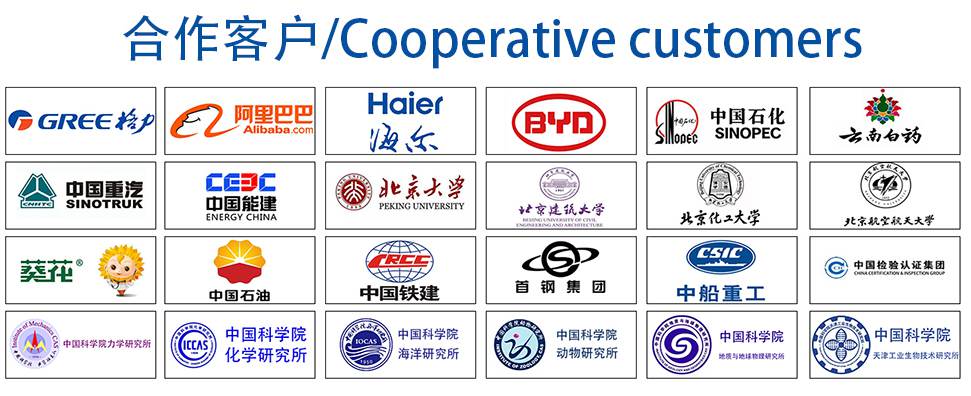