热轧硼合金盘条检测的重要性
热轧硼合金盘条作为一种重要的金属材料,广泛应用于汽车制造、机械加工、建筑结构等领域。其核心优势在于通过添加硼元素提升材料的淬透性和强度,同时保持较好的焊接性能。然而,生产过程中的高温轧制工艺、合金成分波动以及表面处理技术等因素,可能导致盘条出现化学成分不均、力学性能不稳定、表面缺陷等问题。为确保产品质量满足工业需求,必须对热轧硼合金盘条进行系统化、多维度的检测,以验证其化学成分、物理性能及工艺适应性。
核心检测项目与技术要求
1. 化学成分分析
硼元素含量是检测的核心指标之一,需采用光谱分析法(如ICP-OES)精确测定硼及其他合金元素(如Mn、Si、Cr)的配比是否符合GB/T 3077或ASTM A29标准。同时需严格控制碳含量和硫磷杂质,避免影响材料的延展性与韧性。
2. 力学性能测试
通过万能材料试验机进行拉伸试验,检测抗拉强度、屈服强度、断后伸长率及断面收缩率,要求结果满足GB/T 228.1标准。硬度测试(布氏或洛氏)可辅助验证材料强度分布的均匀性。
3. 尺寸与形貌检测
使用卡尺、千分尺及光学投影仪测量盘条直径、椭圆度及直线度公差,需符合YB/T 4162规范。表面缺陷(如折叠、裂纹、氧化皮残留)需通过目视检测和磁粉探伤(MT)排查,确保无深度超过0.1mm的损伤。
4. 金相组织分析
采用金相显微镜观察材料的显微组织,评估晶粒度、珠光体/铁素体比例及夹杂物分布。根据ISO 643标准,晶粒度级别需达到6-8级,且夹杂物级别不超过B类2级,避免局部应力集中。
5. 工艺性能试验
通过冷弯试验(GB/T 232)和扭转试验验证盘条的冷加工性能,要求弯曲180°无裂纹,扭转次数达到标准圈数。焊接试样需进行焊缝冲击试验,评估热影响区韧性是否达标。
6. 耐腐蚀性检测
针对特殊应用场景(如海洋环境),需进行盐雾试验(ASTM B117)或电化学腐蚀测试,测定材料的耐蚀等级,确保硼元素未因偏析导致局部腐蚀风险。
检测流程与质量控制
企业需建立从原材料入厂到成品出厂的全流程检测体系,包括批次抽样规则、实验室比对验证及第三方复检。结合数字化检测设备与MES系统,实现数据实时追溯,确保每批盘条的检测报告完整可查。
结语
热轧硼合金盘条的检测体系需覆盖“成分-性能-工艺-寿命”全维度,通过精准的检测数据为企业优化生产工艺、降低质量风险提供依据。选择具备 或CMA资质的专业检测机构,可有效提升产品合规性及市场竞争力。
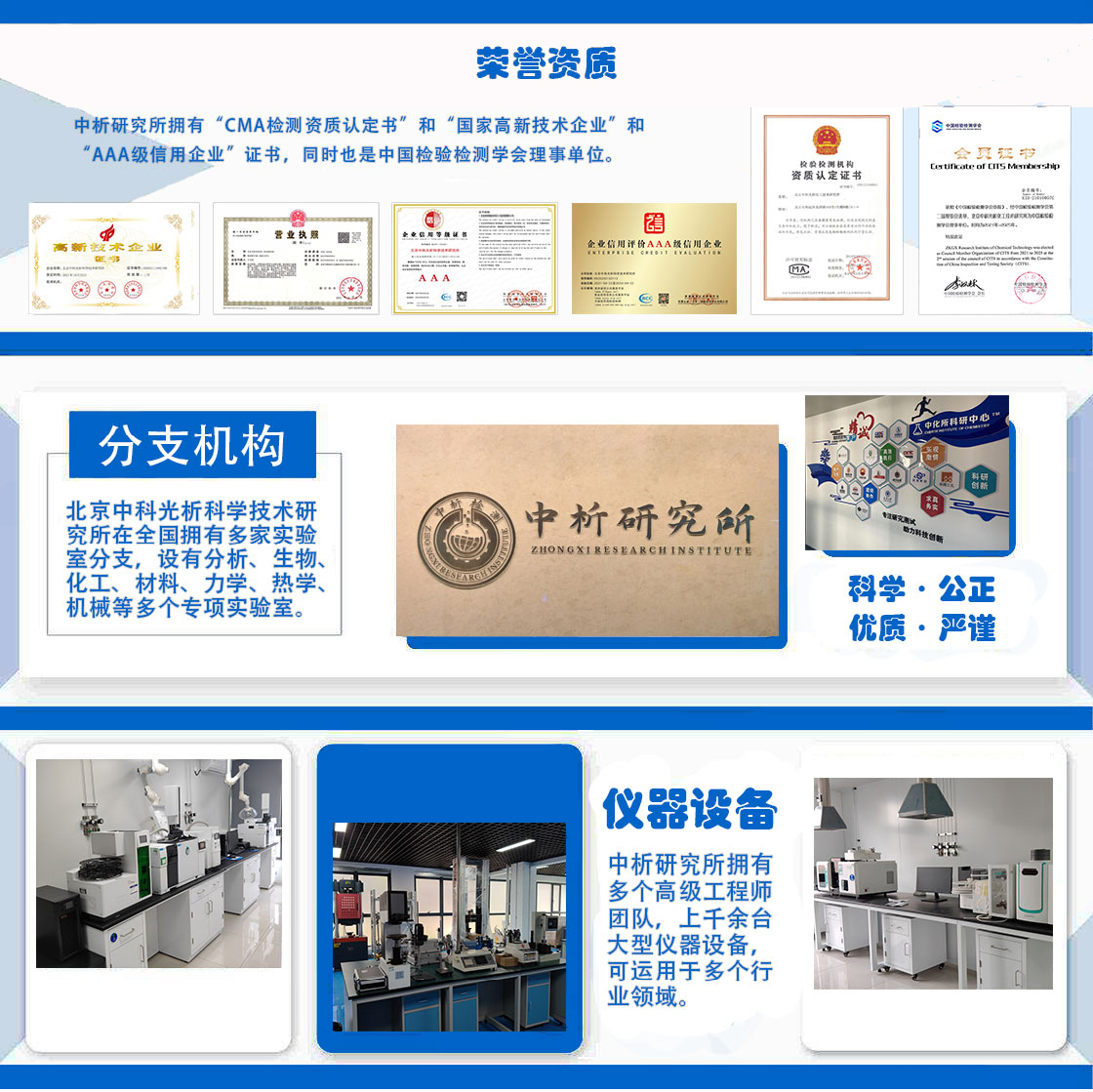
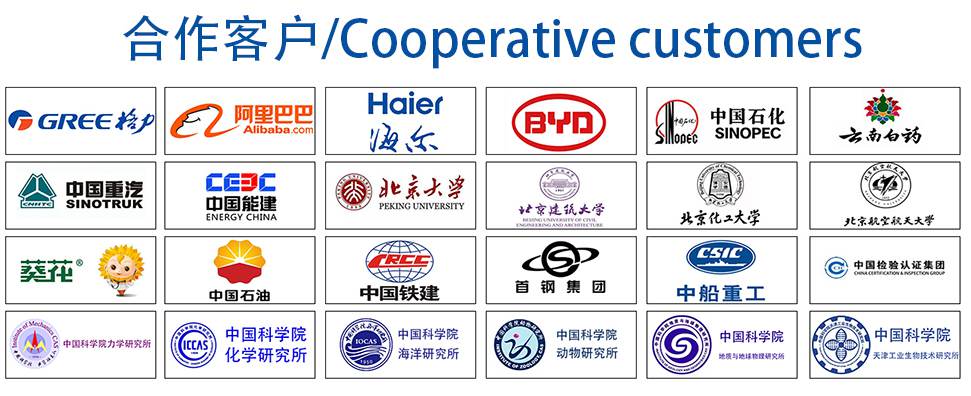