一、检测目的
- 验证器件耐压能力:确保器件在额定电压下不会发生击穿失效。
- 评估工艺稳定性:通过批量抽样检测,验证制造工艺是否达标。
- 失效分析:定位击穿模式下器件的弱点(如材料缺陷、结构设计问题)。
二、核心检测项目
1. 击穿电压(CBO)测试
- 方法:
- 将基极开路(悬浮),在集电极与基极之间施加反向电压,逐步升高电压直至电流骤增(击穿)。
- 使用半导体参数分析仪(如Keysight B1500A)记录击穿点电压值。
- 标准:
- 国际标准(JEDEC JESD77B)、国内标准(GB/T 4587)。
- 允许偏差范围通常为标称值的±5%。
2. 漏电流测试(Leakage Current)
- 目的:验证击穿前漏电流是否符合规格。
- 方法:
- 在接近击穿电压的90%时,测量反向漏电流(如1mA以下为合格)。
- 高温(如125℃)环境下复测漏电流,验证温度对漏电的影响。
3. 温度特性测试
- 目的:评估CBO随温度的变化规律。
- 方法:
- 在高低温试验箱中,分别在-55℃、25℃、150℃等温度点测试击穿电压。
- 绘制CBO随温度变化的曲线,分析器件的热稳定性。
4. 重复性测试(Repeatability Test)
- 目的:验证同一批次器件的参数一致性。
- 方法:
- 对同一批次随机抽取10%~20%的样品进行多次CBO测试,统计标准差。
- 若标准差超过5%,需排查工艺或材料问题。
5. 失效模式分析(Failure Mode Analysis)
- 常见失效模式:
- 烧毁(电流过载导致热击穿)。
- 软击穿(漏电流逐渐增大但未完全击穿)。
- 分析方法:
- 使用显微镜、SEM或X射线检查芯片内部的缺陷(如PN结损伤、金属迁移)。
- 结合电特性测试结果,定位失效的物理位置(如基极边缘电场集中区)。
6. 对比分析(Benchmarking)
- 目的:与竞品或设计目标进行参数对比。
- 方法:
- 对比同类型器件的CBO参数,分析自身器件的优劣势。
- 结合击穿电压与器件结构(如基区宽度、掺杂浓度),优化设计。
三、检测设备与工具
- 高压电源:输出范围需覆盖器件额定电压的1.5倍(如0~1000V)。
- 半导体参数分析仪:支持反向偏置测试模式,精度需达0.1%。
- 高低温试验箱:温度范围-65℃~200℃,控制精度±1℃。
- 防护装置:防静电手套、电流限流电阻(防止击穿时过流损坏设备)。
四、注意事项
- 静电防护:测试前需确保器件和测试环境无静电干扰。
- 电压爬升速率:推荐速率为10V/s,过快可能导致误判。
- 失效安全:击穿后立即切断电源,避免器件持续过载。
- 数据记录:需标注测试温度、湿度及设备型号,确保结果可追溯。
五、
上一篇:正向电流传输比的静态值检测下一篇:连续性检测
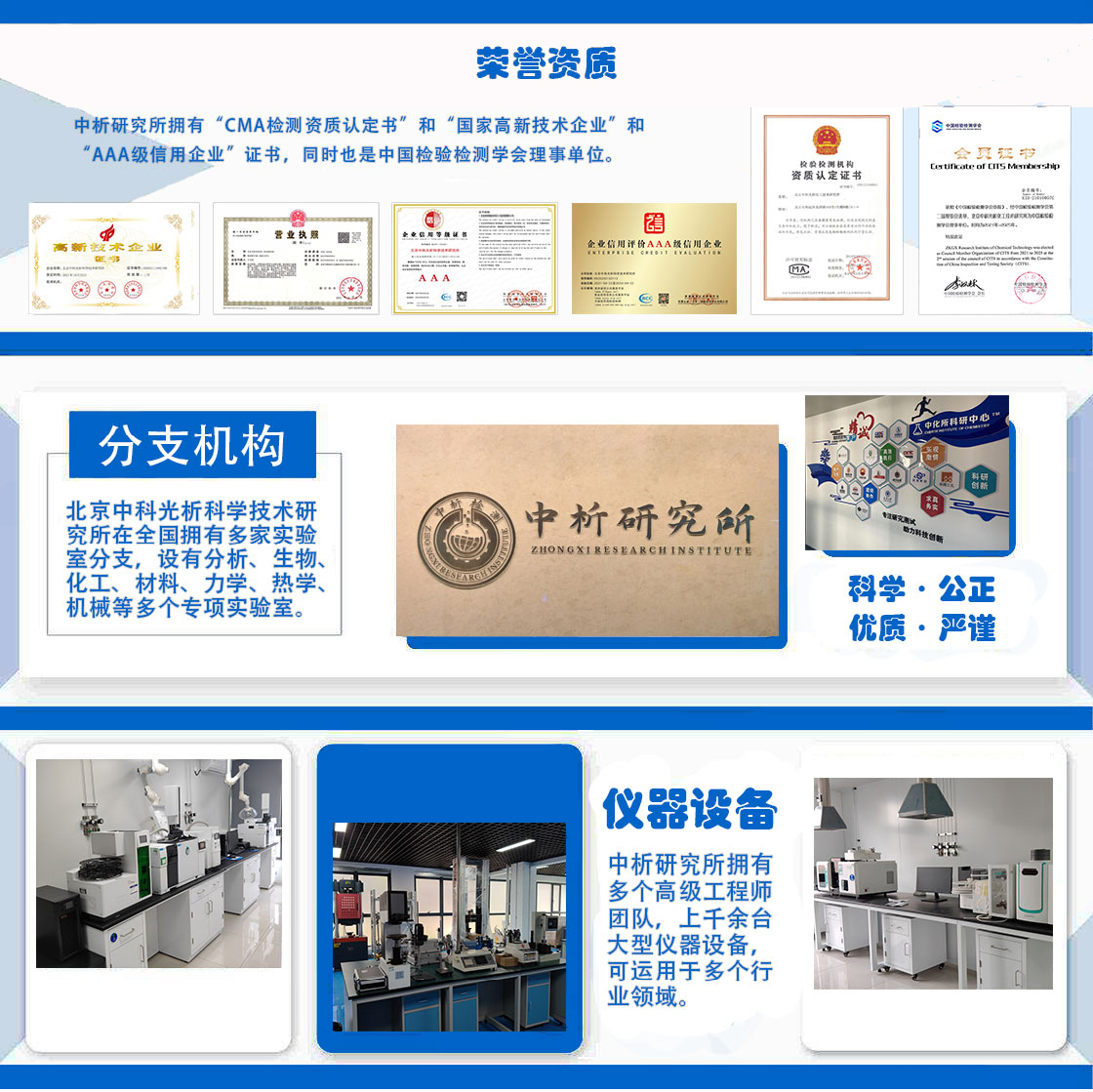
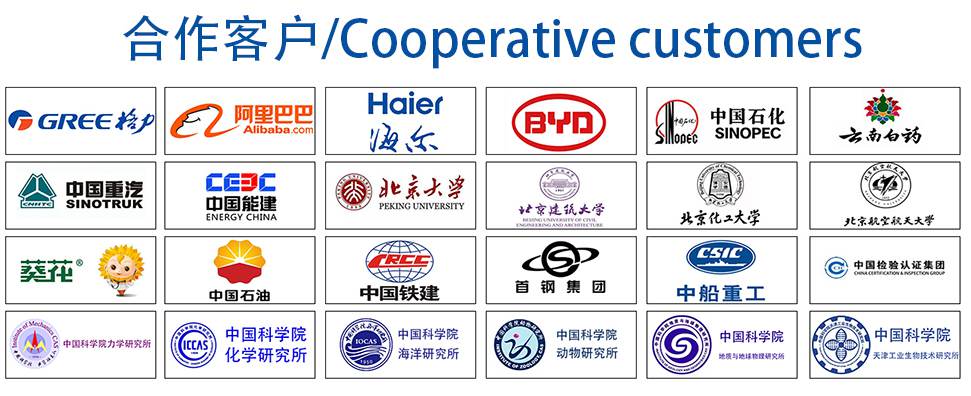
材料实验室
热门检测
254
215
190
203
197
204
210
202
207
217
204
199
203
203
197
195
210
199
209
202
推荐检测
联系电话
400-635-0567