一、最高允许结温的定义
二、核心检测项目及方法
1. 热阻测试(Thermal Resistance Measurement)
- 目的:量化器件从芯片到环境的热传导效率,验证散热设计。
- 检测方法:
- 静态法(如JEDEC JESD51-1):施加恒定电流使器件发热,通过温度传感器(如热电偶、红外热成像)测量结温。
- 动态法(如JESD51-14):利用瞬态热测试仪(如T3Ster)分析温度随时间的变化曲线,计算热阻。
- 关键参数:结到环境热阻(RθJA)、结到外壳热阻(RθJC)。
2. 温度循环测试(Temperature Cycling Test)
- 目的:评估器件在极端温度变化下的结构稳定性。
- 测试条件:
- 温度范围:-55℃至Tjmax(根据器件等级调整)。
- 循环次数:500~1000次(参考MIL-STD-883H)。
- 失效判定:封装开裂、焊点脱落、电气参数漂移>10%。
3. 高温反偏测试(High Temperature Reverse Bias, HTRB)
- 目的:验证器件在高温和高反向电压下的长期可靠性。
- 测试方法:
- 在Tjmax下施加额定反向电压(如功率二极管)持续1000小时。
- 监测漏电流变化,判定材料缺陷或氧化层退化。
- 标准参考:AEC-Q101(车规器件)、JESD22-A108。
4. 实时结温监测(In-situ Tj Monitoring)
- 目的:动态追踪实际工况下的结温波动。
- 技术方案:
- 嵌入式传感器:集成温度敏感参数(如二极管正向压降Vf)。
- 红外热成像:非接触式测量,空间分辨率<5μm(适用于裸片测试)。
- 热敏电阻法:在封装内埋入热敏元件,精度±1℃。
5. 加速寿命测试(Accelerated Life Testing, ALT)
- 目的:通过高温加速老化,预测器件寿命。
- 阿伦尼乌斯模型:激活能(Ea)取0.7eV,公式:AF=exp[(Ea/k)(1/T_use - 1/T_test)]。
- 测试条件:Tjmax+20℃下持续工作1000小时,等效常温(25℃)寿命>10年。
三、检测设备与标准
- 设备清单:
- 热特性测试仪(如Keysight N6705B + T3Ster)。
- 高低温试验箱(ESPEC T系列)。
- 红外热像仪(FLIR X8500sc)。
- 核心标准:
- JEDEC JESD51系列(热测试)。
- MIL-STD-883(可靠性试验)。
- AEC-Q100/Q101(汽车电子)。
四、实际应用注意事项
- 环境修正:板级散热条件(如PCB层数、铜厚)会显著影响RθJA,需根据实际应用场景校准。
- 多热点管理:对于多芯片模块(如IGBT模块),需分别监测各结温并评估热耦合效应。
- 动态负载影响:脉冲工作下的瞬时结温可能比稳态高30%以上,需结合瞬态热阻抗(Zth)分析。
五、结语
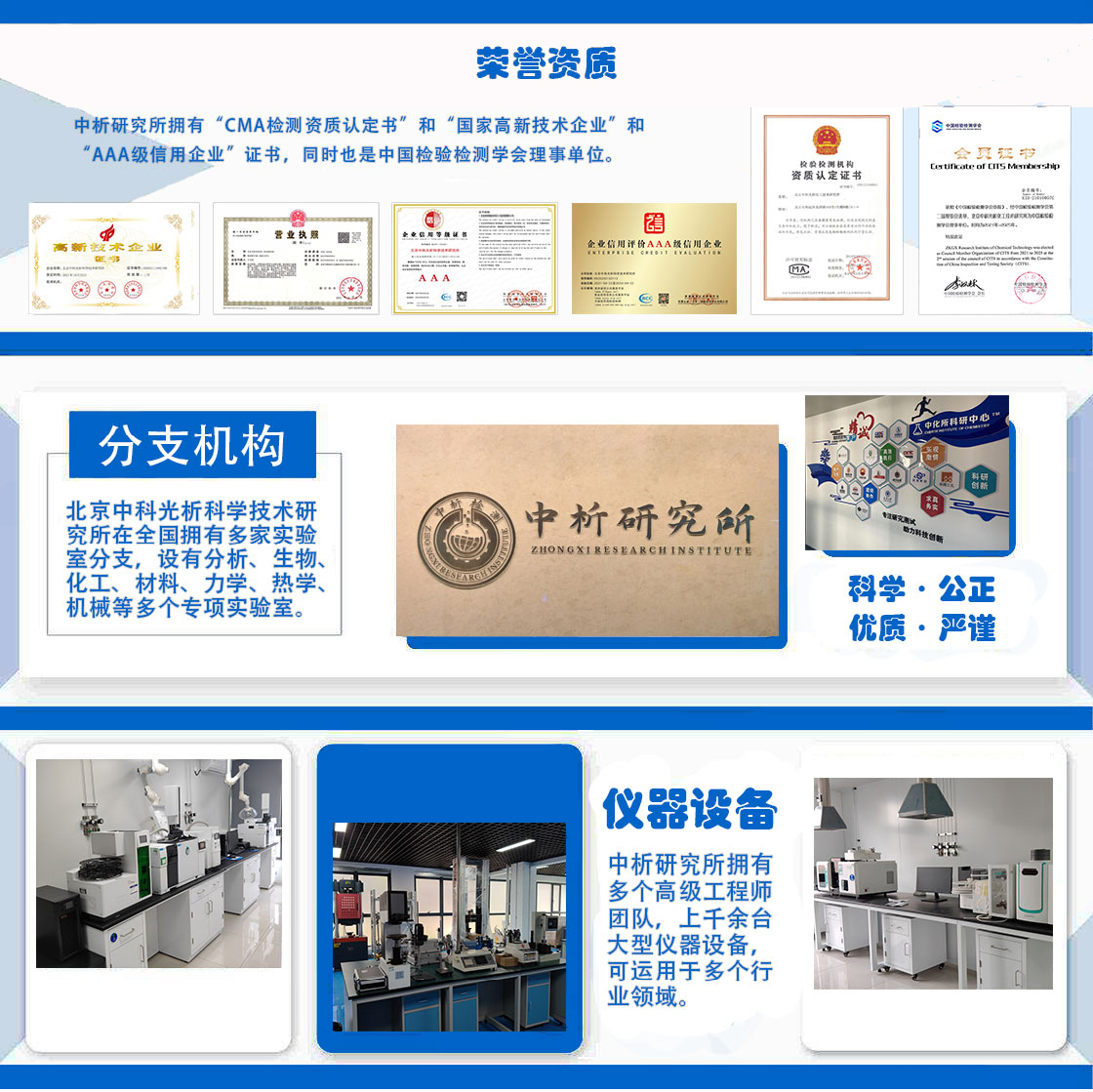
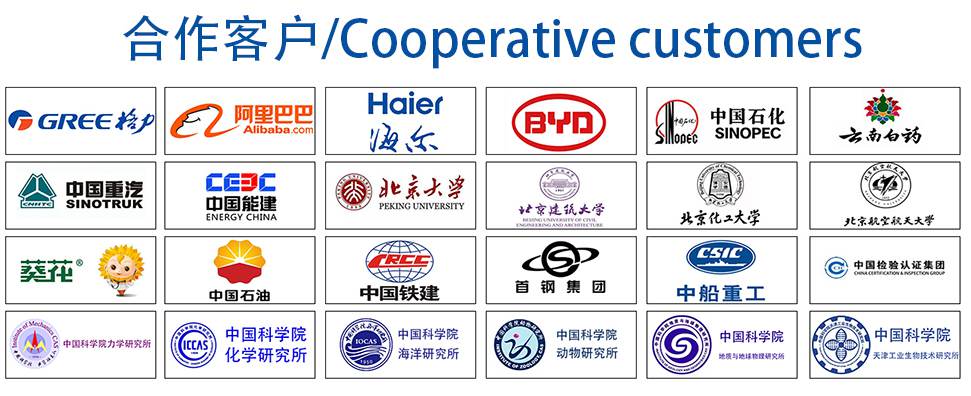
材料实验室
热门检测
254
215
190
203
197
204
210
202
207
217
204
199
203
203
198
195
210
199
209
202
推荐检测
联系电话
400-635-0567