热阻检测的核心项目与技术解析
一、基础材料热阻测试
1. 热导率(Thermal Conductivity)检测
- 测试方法:
- 稳态法(如热板法、护板法):通过稳定温度梯度下的热流测量计算热导率。
- 瞬态法(如激光闪射法、热线法):利用脉冲热源快速测定材料热扩散率。
- 标准参考:ASTM E1461(激光闪射法)、ISO 22007-2(瞬态热线法)。
- 应用场景:评估金属、陶瓷、塑料等材料的导热性能,指导散热器或隔热材料选型。
2. 热阻值(R-value)测定
- 定义:单位面积材料在单位温差下的热阻,计算公式 �=Δ�/�R=ΔT/Q(ΔT为温差,Q为单位面积热流)。
- 检测设备:热流计、防护热板仪。
- 标准参考:ASTM C518(建筑材料)、ISO 8301(稳态热阻测试)。
- 应用场景:建筑墙体、玻璃、保温棉的热阻认证。
二、界面接触热阻测试
1. 接触热阻(Contact Thermal Resistance)
- 定义:两接触表面因粗糙度或间隙导致的热传递效率下降。
- 测试方法:
- 双试样法:通过夹持两试样测量界面温差。
- 压力调控测试:在不同压力下评估接触热阻变化。
- 标准参考:ASTM D5470(电子界面材料测试)。
- 应用场景:芯片与散热器间的导热硅脂性能评估。
三、动态热阻测试
1. 瞬态热响应分析
- 测试原理:施加阶跃温度变化,记录材料温度响应曲线。
- 设备:瞬态热测试仪(如T3Ster)。
- 应用场景:半导体器件瞬态散热性能分析。
2. 循环热负载测试
- 方法:模拟实际工况中的温度循环,检测热阻的稳定性。
- 标准参考:JEDEC JESD51(电子元器件可靠性测试)。
- 应用场景:动力电池、LED灯具的寿命评估。
四、复杂系统热阻检测
1. 电子模组/设备整体热阻
- 测试目标:评估PCB、芯片、外壳等组成的系统散热效率。
- 方法:红外热成像结合热电偶测温,构建热阻网络模型。
- 案例:智能手机处理器散热设计验证。
2. 服装/纺织品热阻测试
- 标准方法:
- 暖体假人测试:模拟人体散热,测量服装整体热阻(单位:clo值)。
- 平板法:ASTM F1868(测量纺织品保温性能)。
- 应用场景:户外服装、消防服的隔热等级认证。
五、环境适应性测试
1. 温湿度循环试验
- 条件:-40℃~150℃温度循环,湿度5%~95% RH。
- 目的:检测热阻材料在极端环境下的性能衰减。
2. 老化测试
- 方法:高温高湿加速老化(如85℃/85% RH,1000小时)。
- 评估指标:热阻变化率、材料形变、界面剥离等。
六、检测设备与技术创新
- 主流设备:热流计(如TA Instruments)、激光闪射仪(Netzsch LFA)、红外热像仪(FLIR)。
- 技术趋势:
- 多物理场耦合测试(热-力-电联合分析)。
- 微纳米尺度热阻测量(扫描热显微镜)。
- 基于AI的热阻预测与优化。
七、行业应用案例
- 电子行业:芯片封装热阻需低于1.5℃/W,否则引发过热故障。
- 新能源汽车:电池模组层间接触热阻优化可提升续航10%以上。
- 建筑节能:Low-E玻璃热阻值>0.5 m²·K/W,满足绿色建筑标准。
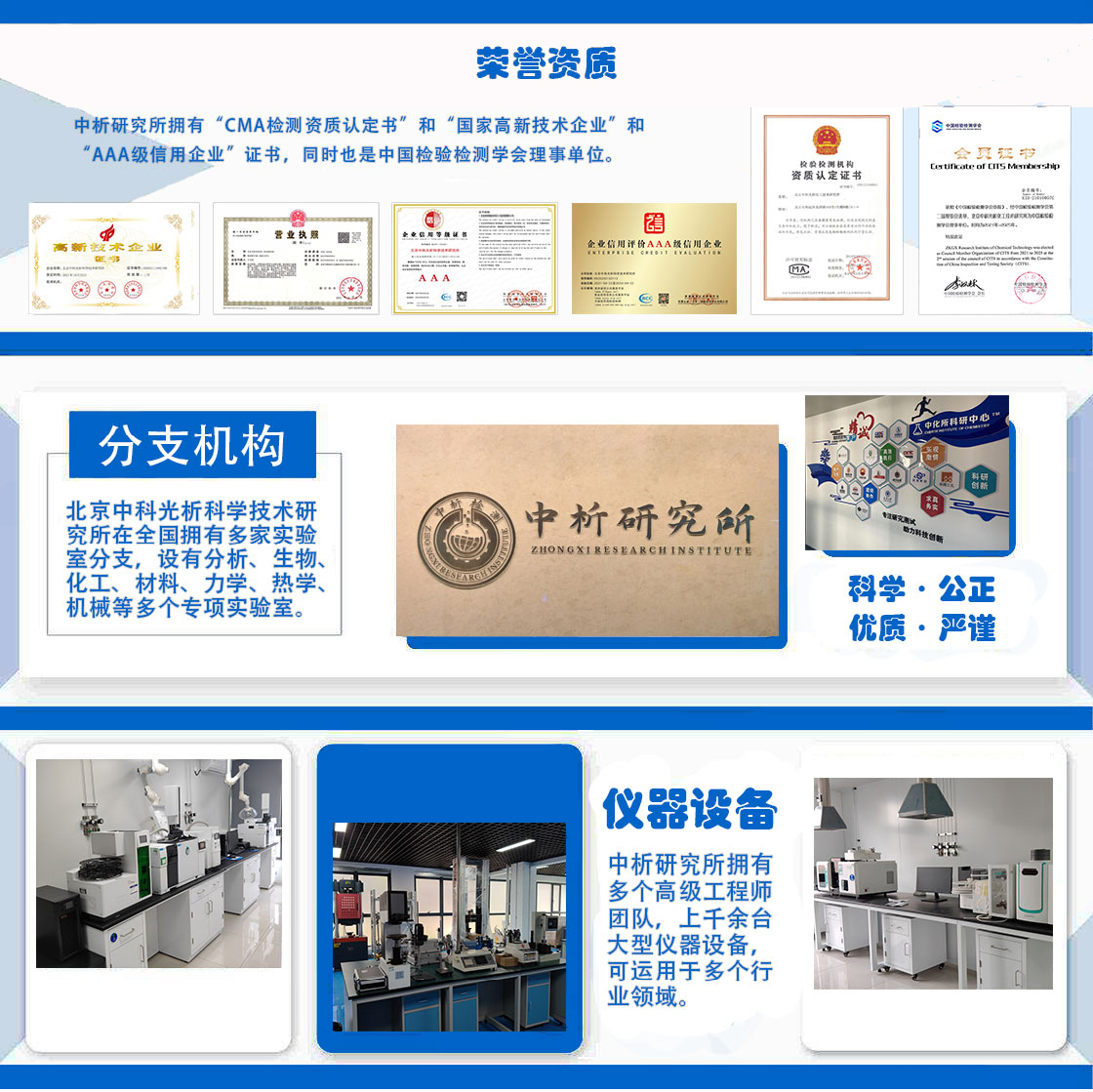
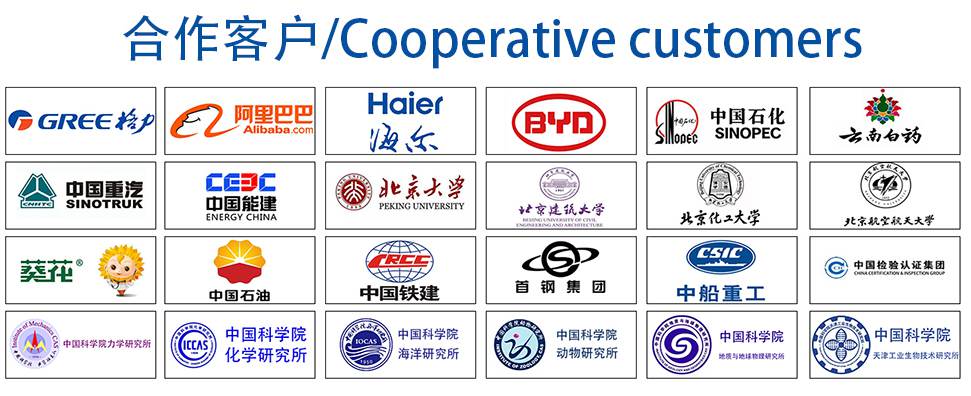
材料实验室
热门检测
254
215
190
203
197
204
210
202
207
217
203
199
203
203
197
195
210
199
209
202
推荐检测
联系电话
400-635-0567