功能验证检测:核心检测项目详解
一、功能验证检测的核心目标
- 需求符合性验证:确认功能实现与需求文档完全一致。
- 缺陷识别与修复:发现潜在逻辑错误、性能瓶颈或安全漏洞。
- 用户体验保障:确保用户交互流程符合预期,避免使用障碍。
二、功能验证检测的关键项目分类
1. 基础功能检测
-
- 检测内容:数据输入范围、格式、边界值,输出结果的正确性。
- 方法:等价类划分、边界值分析、错误推测法。
- 示例:验证用户注册时邮箱格式的合法性,或数值输入超出范围时的提示。
-
- 检测内容:端到端业务流程是否覆盖所有需求场景。
- 方法:流程图分析、用户场景模拟(如购物车下单流程)。
- 工具:Jira、TestRail(用例管理)。
2. 性能与稳定性检测
-
- 检测内容:系统在高并发、大数据量下的响应能力。
- 指标:TPS(每秒事务数)、响应时间、错误率。
- 工具:JMeter、LoadRunner。
-
- 检测内容:断网、断电、数据异常时的系统恢复能力。
- 方法:故障注入测试(如强制关闭服务进程)。
3. 安全性与合规性检测
-
- 检测内容:用户角色权限分配、越权访问风险。
- 示例:普通用户尝试访问管理员接口的拦截效果。
-
- 检测内容:敏感数据加密传输(如HTTPS)、存储加密(如AES)。
- 标准:GDPR、ISO 27001。
4. 兼容性检测
-
- 检测内容:不同操作系统(Windows/macOS)、浏览器(Chrome/Firefox)、移动设备的适配性。
- 工具:BrowserStack、Sauce Labs。
-
- 检测内容:API与第三方系统的数据交互正确性(如支付接口)。
- 方法:Postman、Swagger文档验证。
5. 用户体验(UX)检测
-
- 检测内容:页面布局、按钮响应、提示信息的清晰度。
- 方法:A/B测试、用户焦点小组。
-
- 检测内容:对视障用户的支持(如屏幕阅读器兼容性)。
- 标准:WCAG 2.1。
三、功能验证检测的实施流程
- 需求分析:明确功能点优先级(如MoSCoW法则)。
- 测试用例设计:覆盖正向、反向、异常场景。
- 自动化测试集成:对高频用例采用Selenium、Cypress等工具实现自动化。
- 缺陷管理:使用Jira、Bugzilla跟踪问题闭环。
- 报告生成:输出通过率、缺陷分布、风险建议。
四、常见挑战与解决方案
- 需求变更频繁:采用敏捷测试,迭代更新用例。
- 环境差异导致缺陷:使用Docker容器统一测试环境。
- 性能瓶颈定位困难:结合APM工具(如New Relic)进行代码级分析。
五、行业标准参考
- 软件领域:ISTQB测试体系、IEEE 829测试文档标准。
- 硬件领域:ISO 9001质量管理体系、IEC 61508功能安全标准。
总结
上一篇:屏蔽效率检测下一篇:集电极-基极截止电流检测
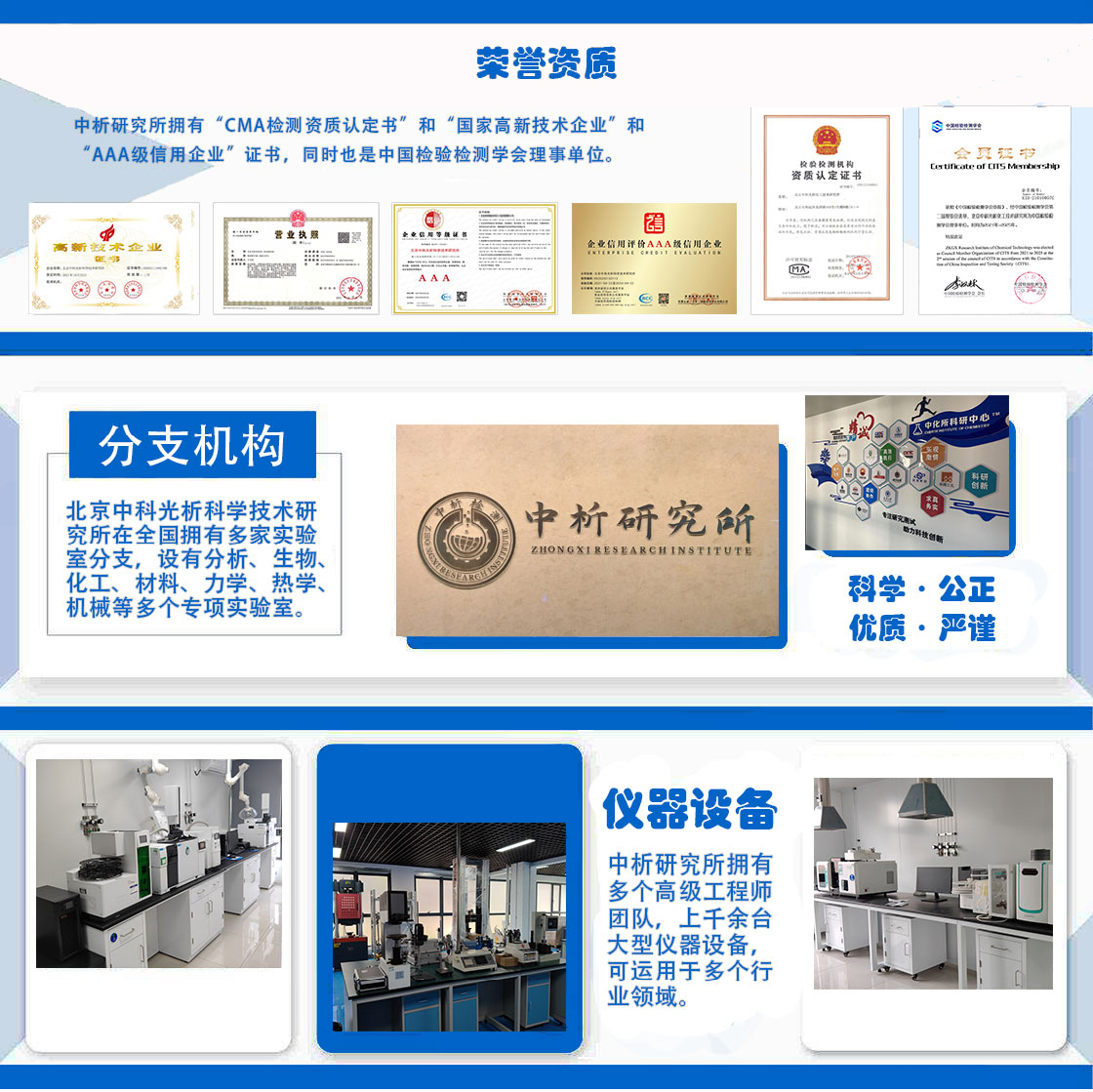
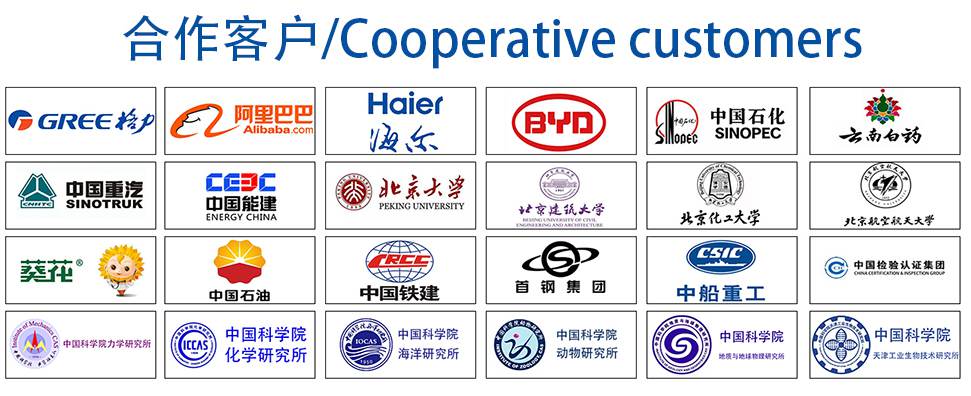
材料实验室
热门检测
254
215
190
203
197
204
210
202
207
217
204
199
203
203
198
195
210
199
209
202
推荐检测
联系电话
400-635-0567