连续性检测:关键检测项目与应用指南
一、连续性检测的核心目标
- 预防故障:通过实时监控关键参数,识别异常趋势,避免突发性停机。
- 提升效率:分析数据优化流程,减少资源浪费。
- 合规性保障:满足行业安全标准(如ISO、FDA、GDPR等)。
二、检测项目的分类与关键指标
1. 工业制造领域
- 设备状态监测:
- 振动分析:通过加速度传感器检测设备振动频率,识别轴承磨损、轴不对中等问题(参考ISO 10816标准)。
- 温度监控:红外热像仪监测电机、齿轮箱等部件的温升,预警过热风险。
- 润滑油质量检测:粘度、金属颗粒含量等指标分析,判断设备磨损程度。
- 工艺连续性:
- 压力与流量稳定性:化工生产中管道压力波动超过±5%可能触发报警。
- 生产线节拍一致性:通过PLC记录各工位时间偏差,优化生产节拍。
2. IT与网络运维
- 系统可用性:
- 服务心跳检测:每秒发送心跳包,响应延迟>1秒视为异常。
- 负载均衡状态:CPU、内存使用率超过80%时自动扩容。
- 数据完整性:
- 数据库事务日志监控:校验事务完整性,防止数据丢失。
- 文件哈希校验:定期对比文件的MD5/SHA-256值,识别非法篡改。
3. 医疗健康领域
- 生命体征连续性:
- 心电监护:动态心电图(Holter)监测ST段异常,预警心肌缺血。
- 血氧饱和度:持续监测SpO₂,低于90%触发警报。
- 设备可靠性:
- 呼吸机压力波形:检测通气压力稳定性,避免患者气压伤。
- 输液泵流速误差:误差超过±5%需立即校准。
4. 能源与基础设施
- 电网稳定性:
- 频率波动检测:电网频率偏差超过±0.5Hz启动调频机组。
- 输电线路温度:光纤测温系统实时监控电缆过热风险。
- 建筑安全:
- 结构振动监测:地震或施工导致的楼体振动超限时启动疏散。
- 消防水压监测:压力低于0.2MPa时自动启动增压泵。
三、实施连续性检测的技术方法
- 传感器与数据采集:
- 硬传感器:如压电式振动传感器、光纤光栅温度传感器。
- 软测量技术:通过数学模型间接计算不可直接测量的参数(如反应釜内物料浓度)。
- 数据传输与存储:
- 工业场景:采用OPC UA协议实现设备互联,边缘计算节点预处理数据。
- 医疗场景:符合HIPAA标准的加密传输,确保患者隐私。
- 数据分析与预警:
- 阈值报警:静态阈值(如温度>100℃)与动态阈值(基于历史数据的3σ原则)。
- 机器学习模型:LSTM网络预测设备剩余寿命,随机森林分类故障类型。
- 响应机制:
- 自动化干预:IT系统中自动重启服务或切换备用节点。
- 人工介入流程:工业场景触发工单系统,指派工程师检修。
四、行业应用案例
-
- 检测项目:冲压机床振动频谱、液压系统压力。
- 效果:故障识别率提升40%,维护成本降低25%。
-
- 检测项目:虚拟机CPU争用、存储IOPS。
- 效果:服务可用性从99.9%提升至99.99%。
-
- 检测项目:气道压力峰值、氧浓度偏差。
- 效果:临床事故率下降60%。
五、挑战与未来趋势
- 挑战:
- 多源数据融合困难(如工业场景中振动、温度、电流信号的关联分析)。
- 高频率检测带来的数据存储与计算压力。
- 趋势:
- 数字孪生技术:构建虚拟模型实时映射物理设备状态。
- 边缘智能:在传感器端集成AI芯片,实现本地化实时决策。
结语
- 《ISO 13374 标准:机械设备状态监测与诊断》
- 《医疗设备连续性检测的FDA合规指南》
- 论文《基于深度学习的工业异常检测方法综述》
上一篇:集电极-基级击穿电压检测下一篇:最高允许结温检测
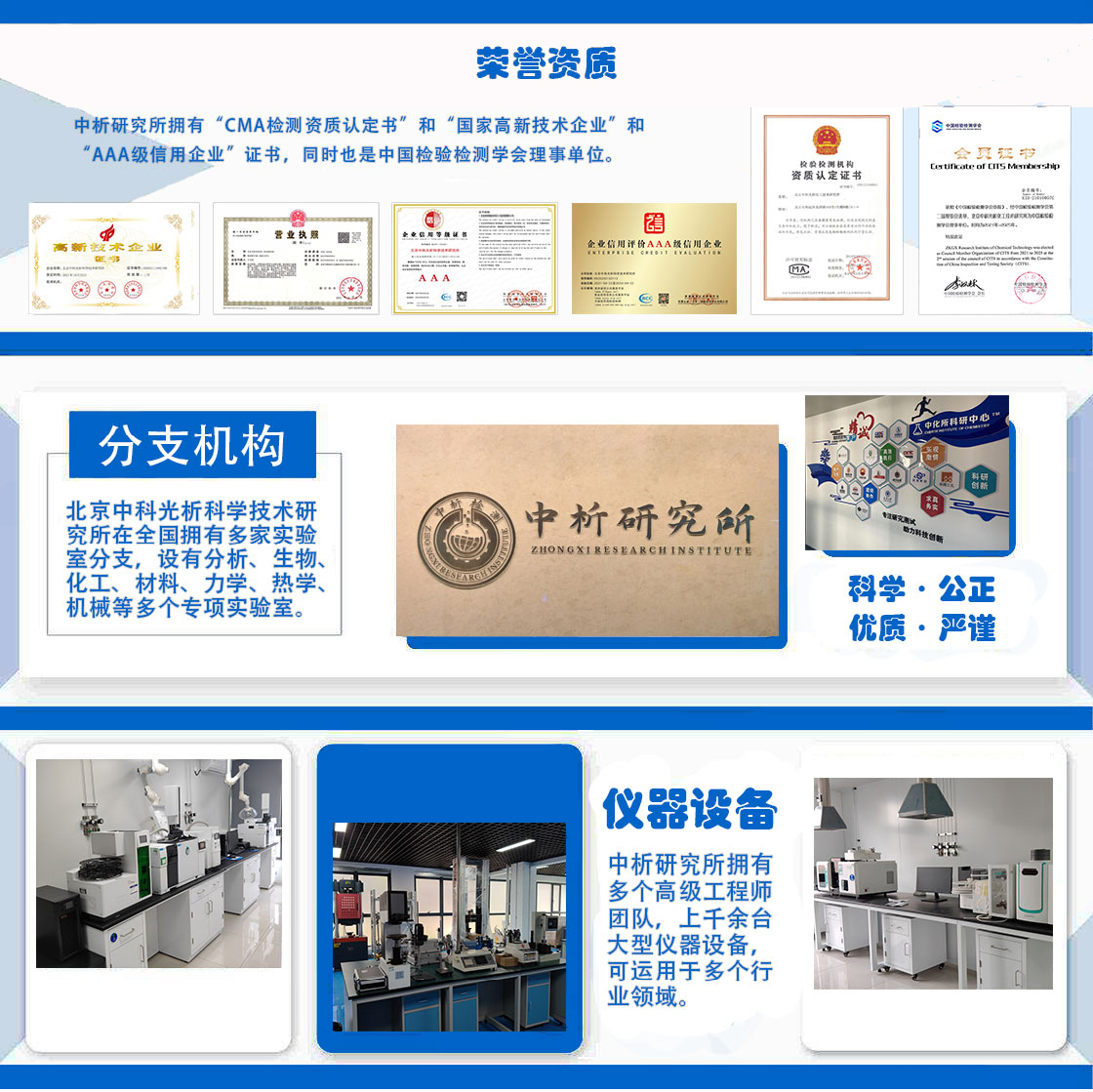
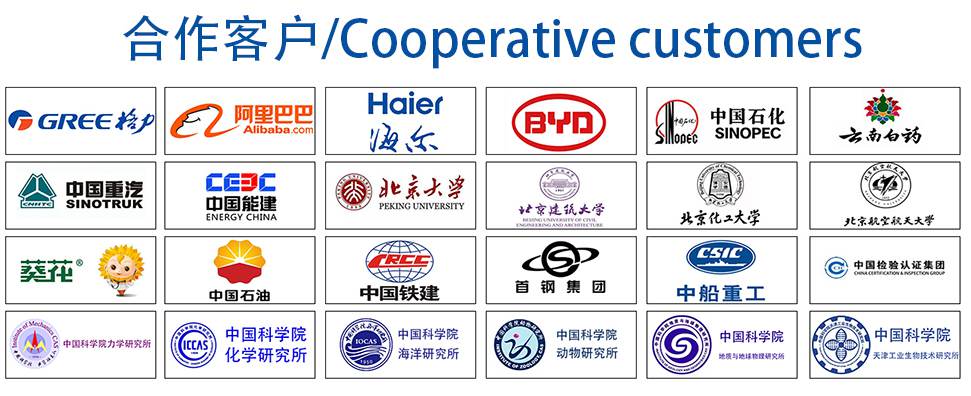
材料实验室
热门检测
254
215
190
203
197
204
210
202
207
217
203
199
203
203
197
195
210
199
209
202
推荐检测
联系电话
400-635-0567