陶瓷熔块釉检测的重要性
陶瓷熔块釉是陶瓷制品表面的关键涂层,直接影响产品的外观质量、耐用性及安全性。其成分通常由硅酸盐、金属氧化物和助熔剂等混合高温熔融后形成玻璃态物质,再经研磨制成釉浆使用。由于生产原料、工艺参数及环境条件的差异,熔块釉的理化性能可能出现波动,进而导致陶瓷产品出现开裂、色差、耐腐蚀性不足等问题。因此,通过科学系统的检测手段对熔块釉的成分、物理性能及有害物质进行严格把控,是确保陶瓷产品品质、满足国际标准及市场需求的必要环节。
检测项目及方法
1. 化学成分分析
化学成分是决定熔块釉性能的核心因素。通过X射线荧光光谱(XRF)或电感耦合等离子体发射光谱(ICP-OES)等技术,检测SiO₂、Al₂O₃、CaO、K₂O、Na₂O等主要氧化物含量,以及重金属(如铅、镉)的残留量。确保配方符合设计要求,避免因成分偏差导致釉面缺陷或环保风险。
2. 物理性能测试
包括熔融温度、粘度、热膨胀系数等关键参数。通过高温显微镜观察釉料的熔融过程,利用热膨胀仪测定其与坯体的膨胀匹配性,防止因热应力差异引发开裂。此外,釉浆的流动性、悬浮稳定性等指标也需通过流变仪和沉降实验进行量化评估。
3. 釉面质量检测
对烧成后的釉面进行目视检查及仪器分析,重点检测光泽度、颜色均匀性、针孔、气泡等表观缺陷。使用光泽度仪量化表面反光性能,借助电子显微镜(SEM)观察微观结构,分析缺陷成因,优化烧成工艺。
4. 耐化学腐蚀性测试
模拟实际使用环境,将釉面浸泡于酸、碱溶液中,通过失重法或表面形貌变化评估其耐腐蚀能力。尤其针对餐具、建筑陶瓷等用途,需符合国标(如GB 4806.4-2016)对食品接触材料的安全要求。
5. 重金属迁移量检测
采用原子吸收光谱(AAS)或电感耦合等离子体质谱(ICP-MS)方法,测定铅、镉、铬等有害元素在酸性条件下的溶出量,确保符合欧盟RoHS、美国FDA等国际法规限值,保障消费者健康。
总结
陶瓷熔块釉检测覆盖成分、物理性能、表观质量及安全性的多维度评价,是优化生产工艺、提升产品竞争力的重要依据。通过标准化检测流程与齐全仪器结合,可精准识别潜在问题,为陶瓷企业提供可靠的质量控制方案,助力行业绿色可持续发展。
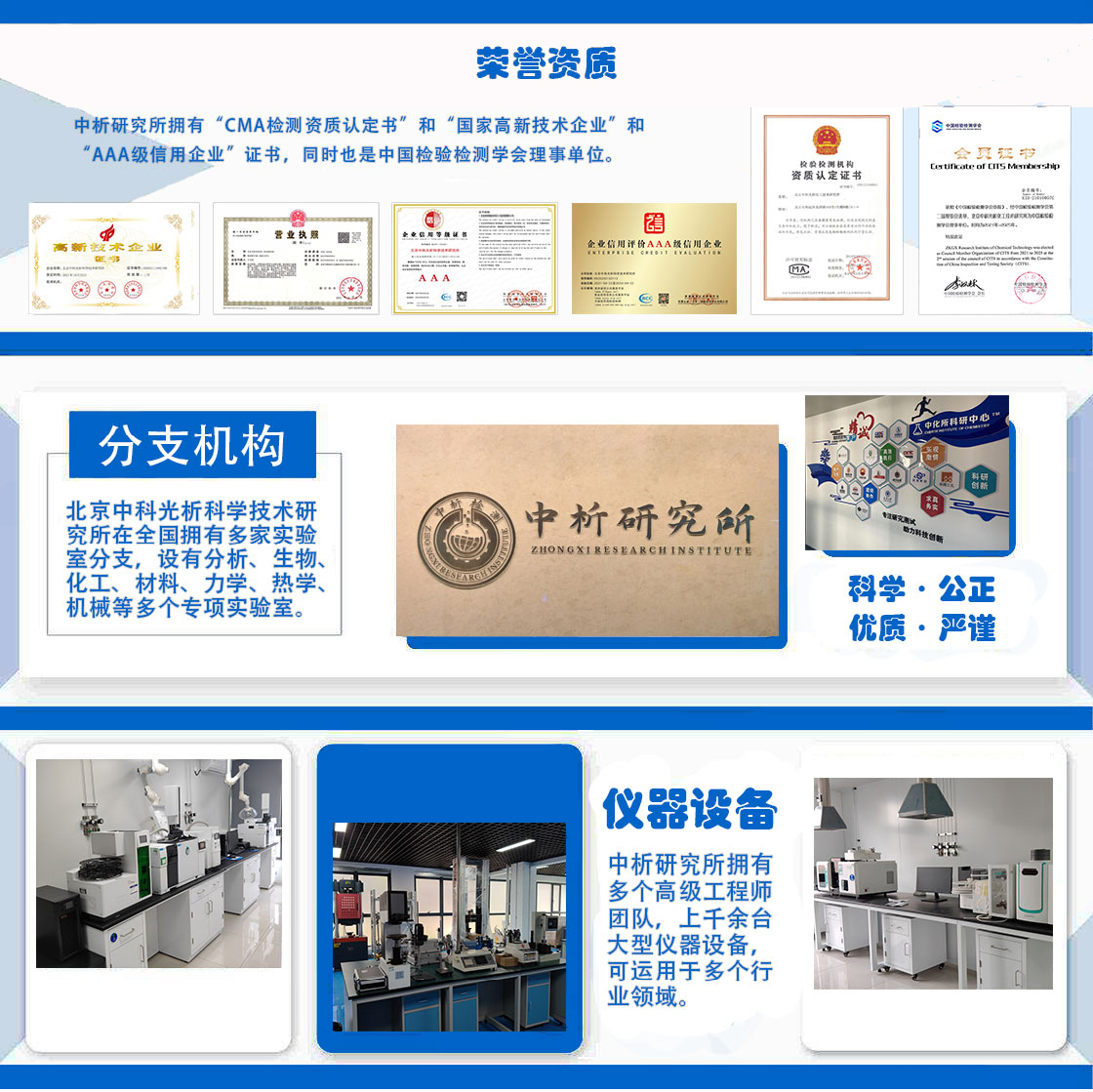
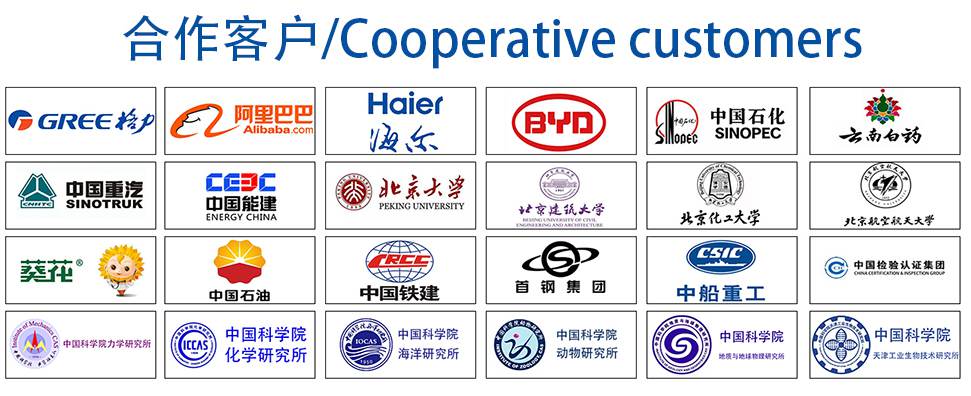