联合循环机组检测项目详解
一、燃气轮机检测项目
-
- 燃烧室内部检查:火焰稳定性、燃烧器积碳、喷嘴磨损等。
- 燃烧气体成分分析:监测CO、NOx排放是否达标,优化燃烧效率。
- 高温部件(透平叶片、燃烧室衬套)的裂纹与热腐蚀检测。
-
- 叶片清洁度与机械完整性检查,避免结垢或异物损伤。
- 转子动平衡测试,确保振动值在允许范围内。
- 空气过滤器压差监测,防止进气堵塞。
-
- 透平叶片涂层磨损评估及裂纹探伤(渗透检测或超声波检测)。
- 高温蠕变变形测量,评估叶片寿命。
- 排气温度场均匀性分析,避免局部过热。
-
- 润滑油系统油质化验(粘度、颗粒污染度)。
- 冷却水系统泄漏检测与流量校准。
- 燃料供应系统压力稳定性测试。
二、余热锅炉(HRSG)检测项目
-
- 管束腐蚀、泄漏检查(涡流检测或内窥镜)。
- 省煤器、蒸发器、过热器表面结垢与积灰分析。
- 烟气侧泄漏检测,防止废气旁路导致效率下降。
-
- 焊缝无损检测(RT/UT/MT)。
- 保温层完整性检查,减少热损失。
- 安全阀与泄压装置的功能性测试。
-
- 给水/炉水化学指标监测(pH值、溶解氧、硅含量等)。
- 凝结水精处理系统效率验证。
- 排污系统的排放合规性检查。
三、蒸汽轮机检测项目
-
- 转子轴系振动与对中精度检测。
- 汽缸结合面密封性检查(真空严密性试验)。
- 叶片与喷嘴的冲蚀、腐蚀评估。
-
- 调速器响应速度与精度测试。
- 主汽门、调节阀的严密性及动作灵活性检查。
-
- 凝汽器真空度监测与泄漏定位。
- 循环水系统换热效率测试。
- 抽气器工作性能验证。
四、辅助系统检测项目
-
- 发电机绝缘电阻、绕组温度监测。
- 变压器油色谱分析(DGA)及局部放电检测。
- 继电保护装置动作试验。
-
- DCS/PLC程序逻辑验证与冗余测试。
- 传感器(压力、温度、流量)校准与漂移修正。
- 紧急停机系统(ETS)可靠性测试。
-
- SCR/SNCR脱硝系统效率测试。
- 烟气在线监测系统(CEMS)数据准确性校验。
- 噪声与振动水平合规性评估。
五、整体性能检测
-
- 机组热效率计算(热耗率、供电煤耗)。
- 联合循环整体出力验证(燃气轮机+蒸汽轮机功率匹配)。
-
- 冷态/热态启动时间优化。
- 负荷升降速率与稳定性分析。
-
- 燃料消耗量与发电成本核算。
- 设备可用率与等效可利用小时数统计。
六、检测周期与标准
- 日常检测:每日巡检(振动、温度、压力等参数记录)。
- 月度检测:润滑油、水质化验及辅助系统功能性测试。
- 年度大修:全面解体检查与关键部件寿命评估。
- 参考标准:ASME、IEC、GB/T等国际及行业规范。
上一篇:管道支吊架检测下一篇:钻井液材料(低黏聚阴离子纤维素)检测
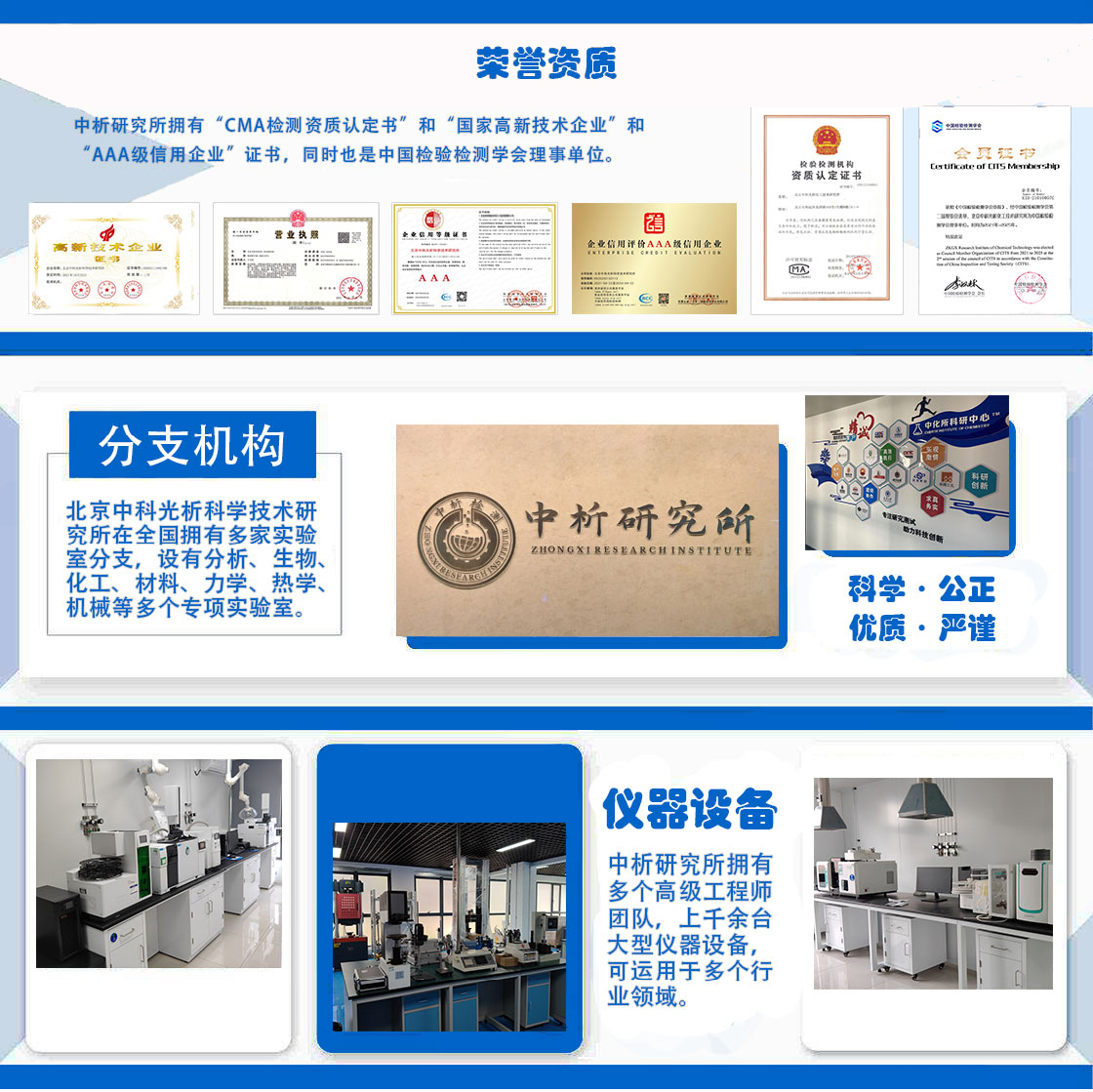
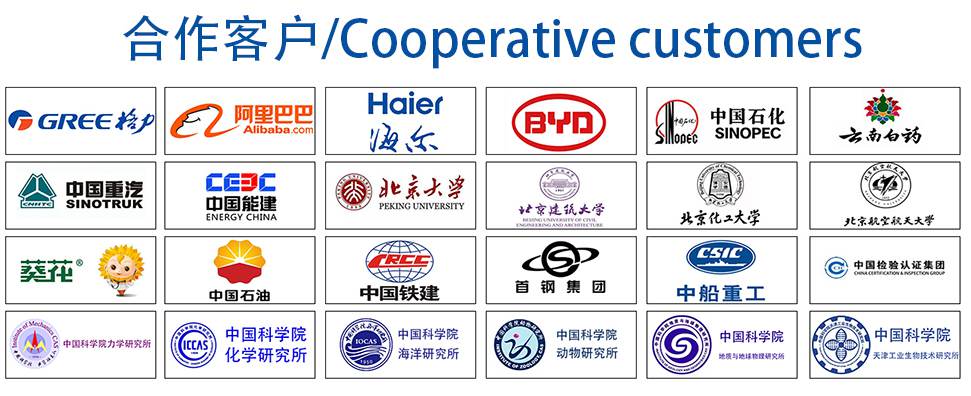
材料实验室
热门检测
276
233
208
216
215
220
228
223
231
231
220
219
222
219
213
209
226
212
224
218
推荐检测
联系电话
400-635-0567