高压管汇及承压元件检测的重要性
高压管汇及承压元件是石油、化工、天然气等行业中传输高压流体的关键设备,其安全性和可靠性直接关系到生产系统的稳定运行和人员安全。由于长期承受高压、腐蚀、振动等复杂工况,管汇及承压元件容易产生裂纹、变形、疲劳损伤等问题,可能导致泄漏甚至爆炸事故。因此,定期进行系统性检测是预防事故、延长设备寿命的必要手段。检测流程需涵盖材料性能、结构完整性、密封性等多方面,并严格遵循行业标准(如ASME、API相关规范)以确保检测结果的准确性和可追溯性。
检测项目及流程详解
1. 外观与尺寸检查
首先需对高压管汇及承压元件进行目视检查,观察表面是否存在腐蚀、划痕、焊接缺陷或机械损伤。同时使用卡尺、测厚仪等工具测量关键部位尺寸(如壁厚、法兰间距),确保符合设计公差要求。若发现明显变形或异常磨损,需进一步分析原因并评估风险。
2. 压力试验
压力试验是核心检测项目之一,包括静态水压试验和气密性试验:
- 静态水压试验:将设备加压至设计压力的1.5倍(依据标准调整),保压10-30分钟,检查是否存在渗漏或永久变形。
- 气密性试验:使用惰性气体加压至工作压力,通过气泡法或电子检漏仪检测微小泄漏点。
3. 无损检测(NDT)
针对关键焊缝和高应力区域,采用无损检测技术:
- 超声波检测(UT):探测内部裂纹、夹杂等缺陷。
- 磁粉检测(MT):用于铁磁性材料表面及近表面缺陷的识别。
- 射线检测(RT):通过X射线或伽马射线成像分析内部结构完整性。
4. 材料性能分析
通过取样或原位检测评估材料性能,包括:
- 硬度测试(布氏/洛氏硬度计)
- 化学成分分析(光谱仪)
- 金相组织观察(显微镜)
5. 密封件与连接部件专项检测
检查法兰、螺纹接头、密封圈等部位的配合状态及密封性能,对重复使用的密封件需评估其弹性形变恢复能力,必要时进行更换。
6. 振动与疲劳测试(可选)
针对动态工况下的管汇系统,通过振动台模拟实际工况,监测应力集中区域的疲劳裂纹扩展趋势,评估剩余寿命。
检测注意事项
检测前需彻底清洁设备表面,排除油污、锈垢干扰;检测过程中需遵循安全规程,使用校准合格的仪器;检测后应出具详细报告,提出维修或更换建议。对于高风险部件,建议结合在线监测技术实现实时状态评估。
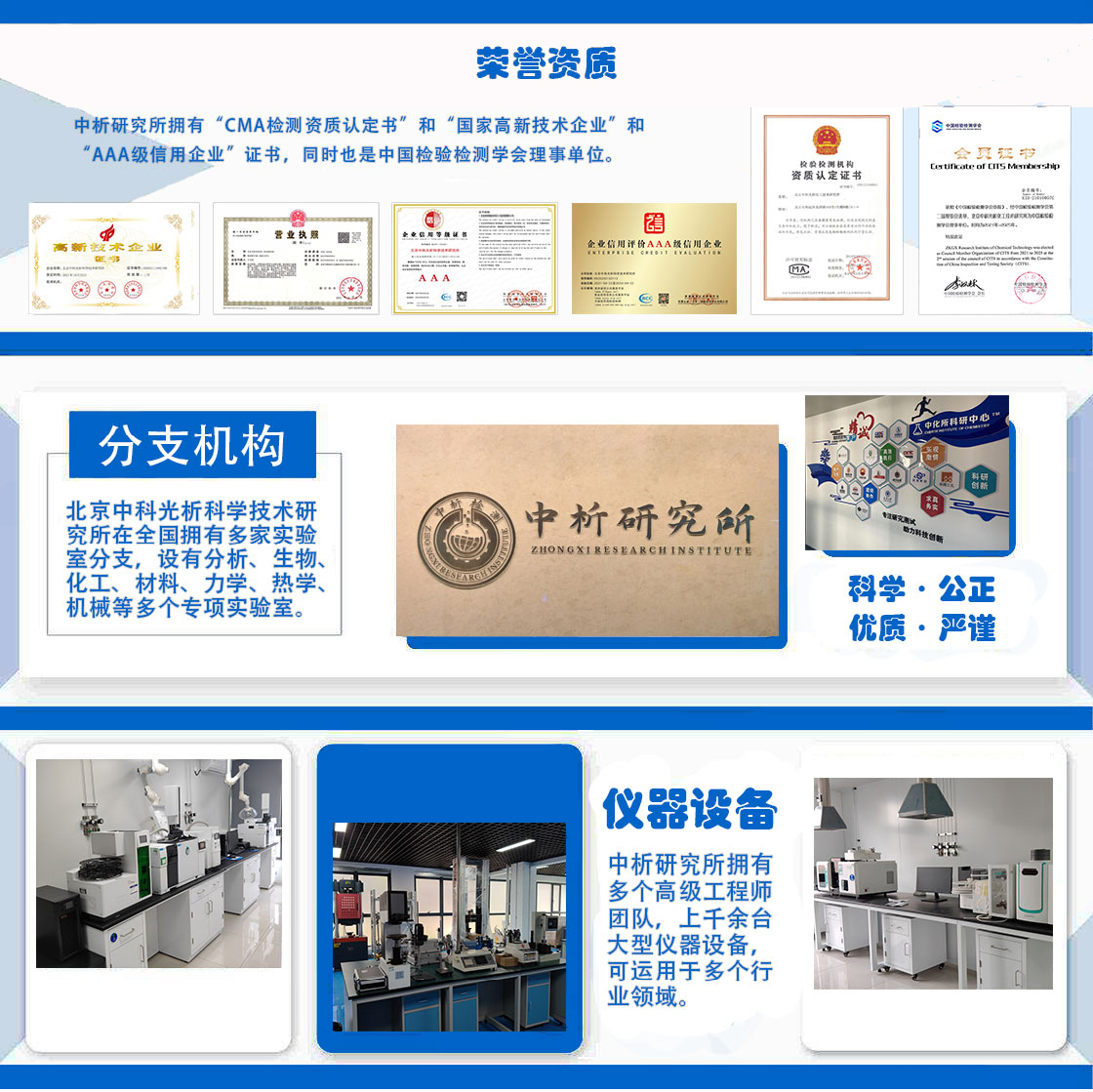
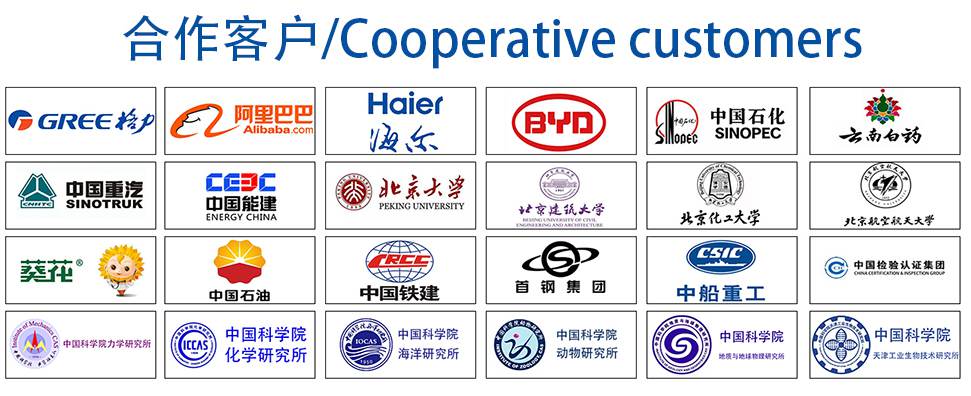