燃气轮机检测项目详解
一、外观与基础结构检测
-
- 腐蚀与变形:检查外壳是否存在锈蚀、凹痕或裂纹,重点关注焊缝区域。
- 密封性验证:通过气压或泡沫剂检测法兰、阀门连接处的泄漏情况。
- 热疲劳痕迹:观测高温区域(如燃烧室周边)的氧化层剥落或颜色异常。
-
- 叶片状态:目视检查叶片表面腐蚀、磨损、积垢情况,使用内窥镜探查内部流道。
- 导叶调节机构:测试导叶角度调节的灵活性,检查作动器的液压/气动密封。
-
- 高温部件损伤:检查涡轮叶片是否存在烧蚀、蠕变变形或涂层脱落。
- 冷却孔堵塞:利用内窥镜确认冷却空气通道的通畅性,防止局部过热。
二、性能参数检测与分析
-
- 输出功率衰减:对比历史数据,分析功率下降是否超出设计允许范围(通常应<5%)。
- 热效率评估:通过排气温度、燃料消耗量计算热效率,判断燃烧系统状态。
-
- 振动频谱分析:安装加速度传感器,监测轴承、齿轮箱的振动幅值(通常要求<7.1mm/s RMS)。
- 温度梯度异常:使用红外热像仪扫描燃烧室、涡轮段,温差>50℃需重点排查。
- 排气成分检测:测量NOx、CO排放浓度,判断燃烧是否充分(ISO标准限值:NOx<50ppm)。
三、无损检测技术(NDT)应用
检测方法 | 适用场景 | 技术要点 |
---|---|---|
渗透检测(PT) | 表面裂纹检测(如叶片根部) | 清洗后喷洒显影剂,紫外灯下观察缺陷显示 |
磁粉检测(MT) | 铁磁性材料表面/近表面缺陷 | 磁化后施加荧光磁粉,裂纹处形成磁痕 |
超声波检测(UT) | 内部裂纹、厚度测量(如壳体) | 采用5MHz探头,分析回波时差与信号强度 |
射线检测(RT) | 焊接质量、内部结构完整性 | X射线或γ射线透照,数字化成像分析 |
四、燃烧系统专项检测
-
- 积碳与磨损:拆卸后测量喷嘴孔径偏差(允许公差±0.05mm)。
- 雾化效果测试:在试验台模拟喷射,观察燃料分布均匀性。
-
- 热障涂层完整性:使用涡流检测仪测量涂层厚度,脱落面积>10%需修复。
- 裂纹扩展监测:定期进行荧光渗透检测,记录裂纹长度变化趋势。
五、辅助系统检测
-
- 油液分析:检测金属颗粒含量(如Fe>50ppm预警磨损)、黏度变化(新油±15%)。
- 滤芯压差监测:压差>0.5bar时需更换滤芯,防止供油不足。
-
- 空气冷却器效率:测量冷却前后空气温差,效率下降>20%需清洗散热片。
- 水冷管路流量检测:超声波流量计验证流量是否满足设计值(误差<5%)。
六、典型案例分析
- 检测过程:振动监测发现3倍频异常升高,内窥镜发现第7级叶片根部裂纹。
- 处理措施:更换受损叶片,调整动平衡,振动值从9.2mm/s降至4.5mm/s。
- 检测方法:热成像显示局部温度达980℃(正常值≤850℃),渗透检测确认烧蚀孔洞。
- 解决方案:更换联焰管,优化燃料分配,NOx排放降低18%。
七、检测周期建议
检测类型 | 周期 | 主要项目 |
---|---|---|
日常巡检 | 每8小时 | 振动监测、油压/油温、排气温度 |
月度检查 | 30天 | 滤芯更换、紧固件扭矩校验、泄漏检测 |
年度大修 | 12个月 | 无损检测、燃烧系统解体检查、动平衡校正 |
结语
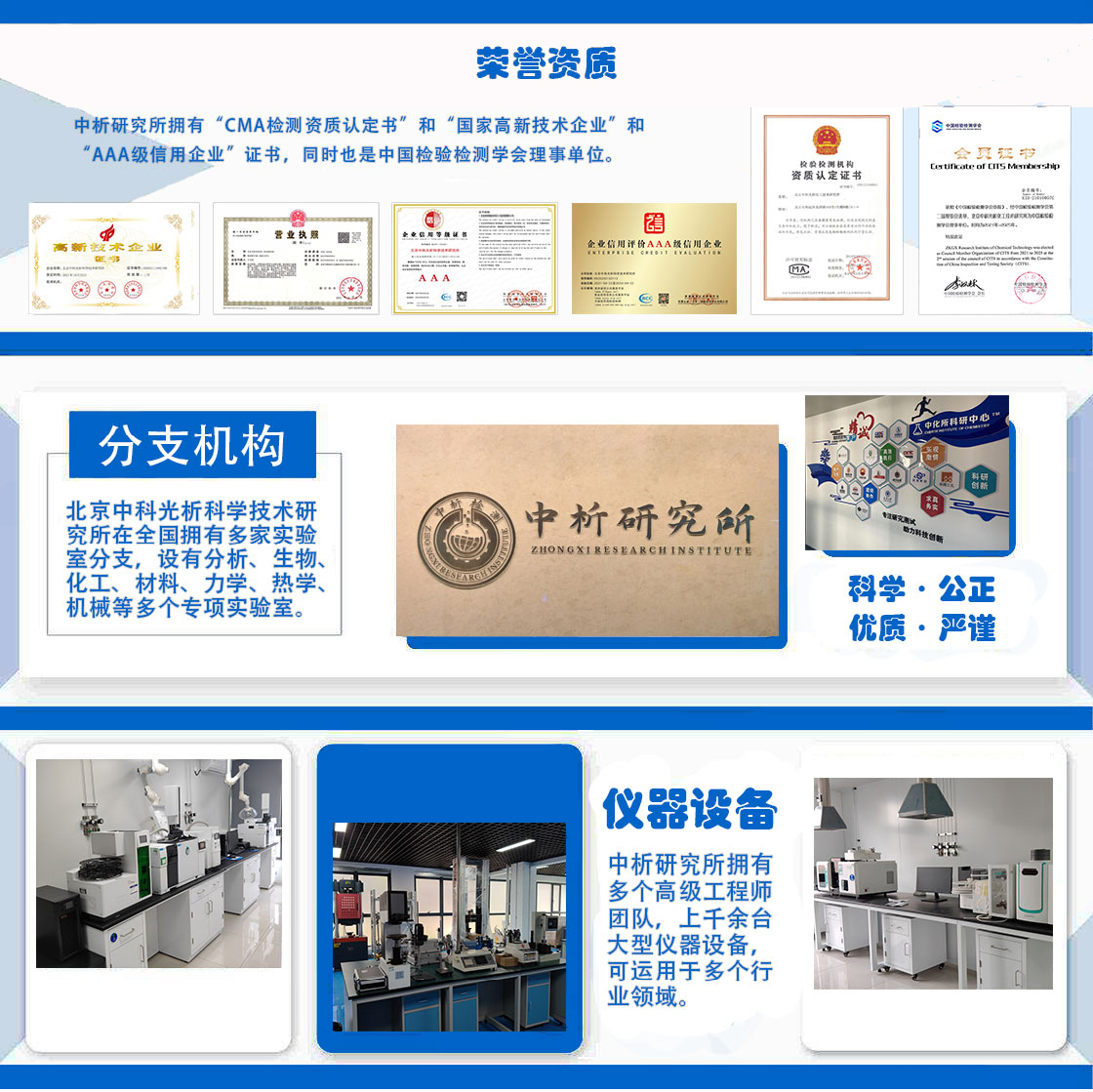
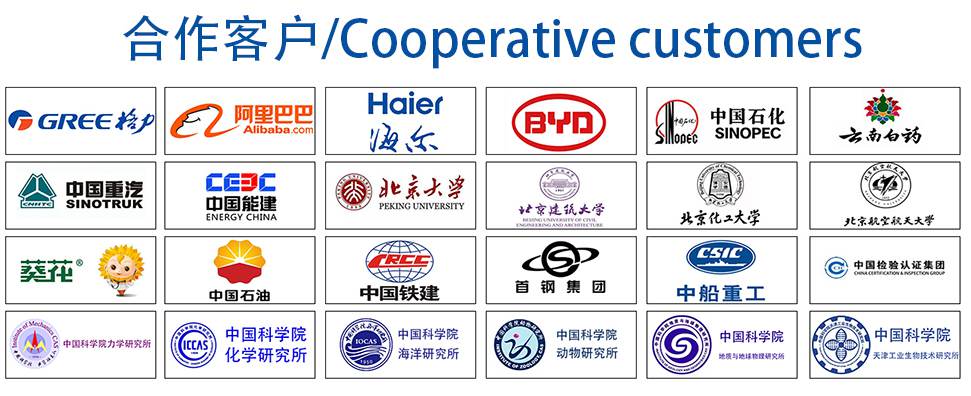
材料实验室
热门检测
269
227
202
211
209
211
225
218
228
229
212
213
216
215
207
204
221
207
220
214
推荐检测
联系电话
400-635-0567