驱动电机系统检测的重要性与核心内容
随着新能源汽车、工业自动化等领域的快速发展,驱动电机系统作为动力输出的核心部件,其性能直接影响设备稳定性与使用寿命。为保障电机系统在复杂工况下的可靠运行,专业化的检测流程涵盖电气性能、机械特性、环境适应性等六大关键领域,涉及超过20项细分指标。通过科学系统的检测,可有效预防因电机故障引发的安全隐患,同时优化能效表现,延长设备服役周期。
检测项目一:电气性能测试
该项检测聚焦电机系统的电能转换效率与输出稳定性,使用高精度功率分析仪测量空载/负载状态下的电压、电流、功率因数等参数。重点关注额定功率偏差是否≤5%,效率曲线是否达到GB/T 18488标准要求,同时检测再生制动时的能量回收效率。
检测项目二:机械特性评估
通过转矩传感器和振动分析仪,对电机输出轴的转矩脉动、径向跳动进行动态监测。要求空载转速波动≤1%、额定转矩偏差≤3%,NVH测试中1米距离噪声值需控制在65dB(A)以内。对于伺服电机还需验证0.01°级别的定位精度。
检测项目三:绝缘与耐压测试
采用2500V绝缘电阻测试仪检测绕组对地绝缘阻值,要求冷态≥50MΩ,热态≥5MΩ。耐压测试施加2Un+1000V(最低1500V)持续1分钟不发生击穿,泄露电流需稳定在0.5mA/m以下,确保高压系统的安全性。
检测项目四:环境适应性验证
在高低温试验箱中进行-40℃~120℃温度循环测试,模拟湿热、盐雾等恶劣环境。要求电机在85℃持续运行4小时后,绝缘性能下降不超过15%,防护等级需达到IP67标准,确保沙尘、淋雨等工况下的正常运行。
检测项目五:能效与温升测试
使用红外热像仪监测绕组温升,规定H级绝缘材料最高温度≤180℃,轴承部位温升≤40K。能效测试要求系统效率MAP图中高效区(效率≥90%)覆盖80%以上工作区间,符合IE4及以上能效等级标准。
检测项目六:控制功能验证
通过CAN总线分析仪检测控制器通讯协议,验证转速闭环控制的稳态误差≤0.2%。模拟电网电压骤降、负载突变等异常工况,测试故障保护响应时间是否≤10ms,确保过流、过温等保护功能可靠触发。
整套检测体系需依据GB/T 18488.1-2015等国家标准,结合ISO 16750系列环境试验规范,运用自动化测试平台实现数据采集与分析。定期检测可降低电机故障率35%以上,为设备安全运行提供技术保障。
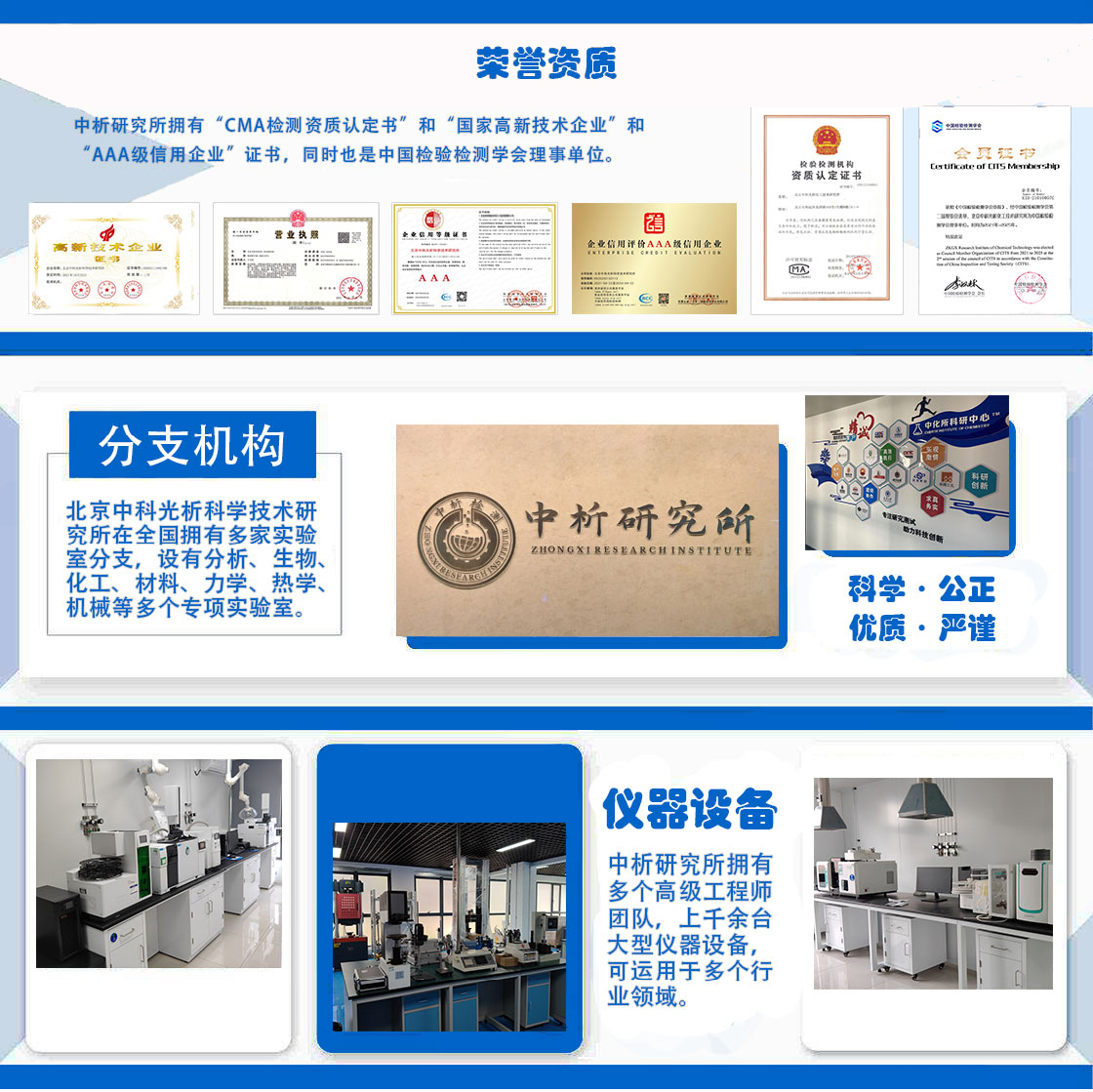
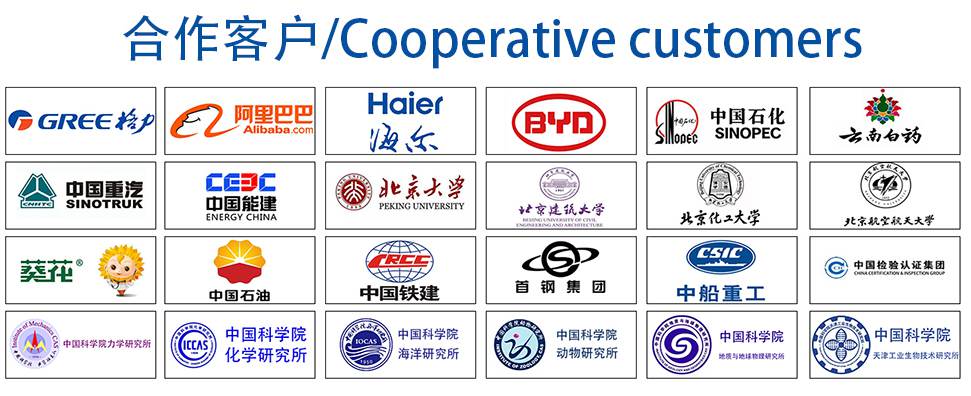