电动机功率因数检测:能效优化的科学决策依据
在工业4.0与"双碳"战略双重驱动下,电动机作为工业领域核心动力设备,其能效管理已成为企业降本增效的关键环节。据国家能源局2024年研究报告显示,我国工业电机年耗电量占全社会总用电量的64.7%,其中因功率因数不达标导致的电能损耗达8-12%。电动机功率因数检测通过量化评估设备运行效率,不仅可降低企业综合电费支出(依据《供电营业规则》功率因数奖惩机制),更能提升电网质量稳定性。该项目的核心价值在于构建"测量-诊断-优化"的闭环管理体系,为工业企业实现每台电动机年均节约电费3-5万元的经济效益,同时支撑国家2025年电机系统能效提升20%的规划目标。
基于向量分析法的检测技术原理
现代电动机功率因数检测采用高精度数字信号处理技术,通过同步采集电压、电流波形数据,运用离散傅里叶变换(DFT)分解基波与谐波分量。据中国电力科学研究院实验验证,该技术对三相异步电动机的功率因数测量精度可达±0.5%,且能实时辨识电压跌落、谐波畸变等电能质量问题。技术方案创新性引入动态负载率补偿算法,有效解决传统检测方法在电机轻载工况下误差偏大的行业痛点,特别适用于注塑机、空压机等变负载设备的能效监测场景。
全周期数字化检测实施流程
典型检测流程包含三个阶段:预处理阶段安装0.2S级电能质量分析仪,按照GB/T 12325-2022标准设定10分钟测量间隔;实施阶段采用无线组网技术建立多点同步监测,确保数据采集涵盖启停、满载、待机等工况;后处理阶段运用机器学习算法构建设备能效画像,生成包含功率因数动态曲线、无功损耗热力图的可视化报告。某特大型钢铁集团应用该方案后,其轧钢车间132台高压电机平均功率因数从0.76提升至0.93,年节省基本电费逾380万元(数据来源:冶金工业规划研究院2024年能效审计报告)。
工业电机能效优化解决方案实践
在石化行业某乙烯装置改造工程中,技术人员通过功率因数检测发现压缩机电机存在36%的轻载运行时间。通过加装智能电容器组并优化控制策略,使系统功率因数稳定在0.95以上,同时降低变压器容量需求15%。该案例验证了"检测驱动决策"的实践价值,其经验已纳入《石油化工企业电力系统设计规范》2024年修订草案。值得关注的是,检测数据还可对接企业能源管理系统(EMS),为设备预防性维护提供关键参数支撑。
三级质量保障体系构建
为确保检测结果权威性,项目建立涵盖设备层、过程层、认证层的质量管控机制:设备层采用经 校准的Fluke 1738电能记录仪,过程层执行ISO/IEC 17025实验室管理体系,认证层通过第三方机构出具CMA检测报告。在新能源汽车电机测试领域,该体系成功帮助某驱动电机厂商通过欧盟CE认证,其产品空载功率因数达到0.98的行业领先水平。据国家电机质检中心统计,采用该质量体系的企业检测结果复现性提升至97.3%。
展望未来,建议从三方面深化技术应用:首先开发基于物联网的电动机群组能效监测平台,实现厂级电能质量全景感知;其次推进检测数据与数字孪生技术的融合应用,构建虚拟调试环境;最后应加快制定《电动机系统能效在线监测技术规范》国家标准,建立覆盖设计、运行、维护全生命周期的能效管理体系。通过持续创新检测技术与管理模式,有望推动我国工业电机系统整体效率向国际领先水平迈进。
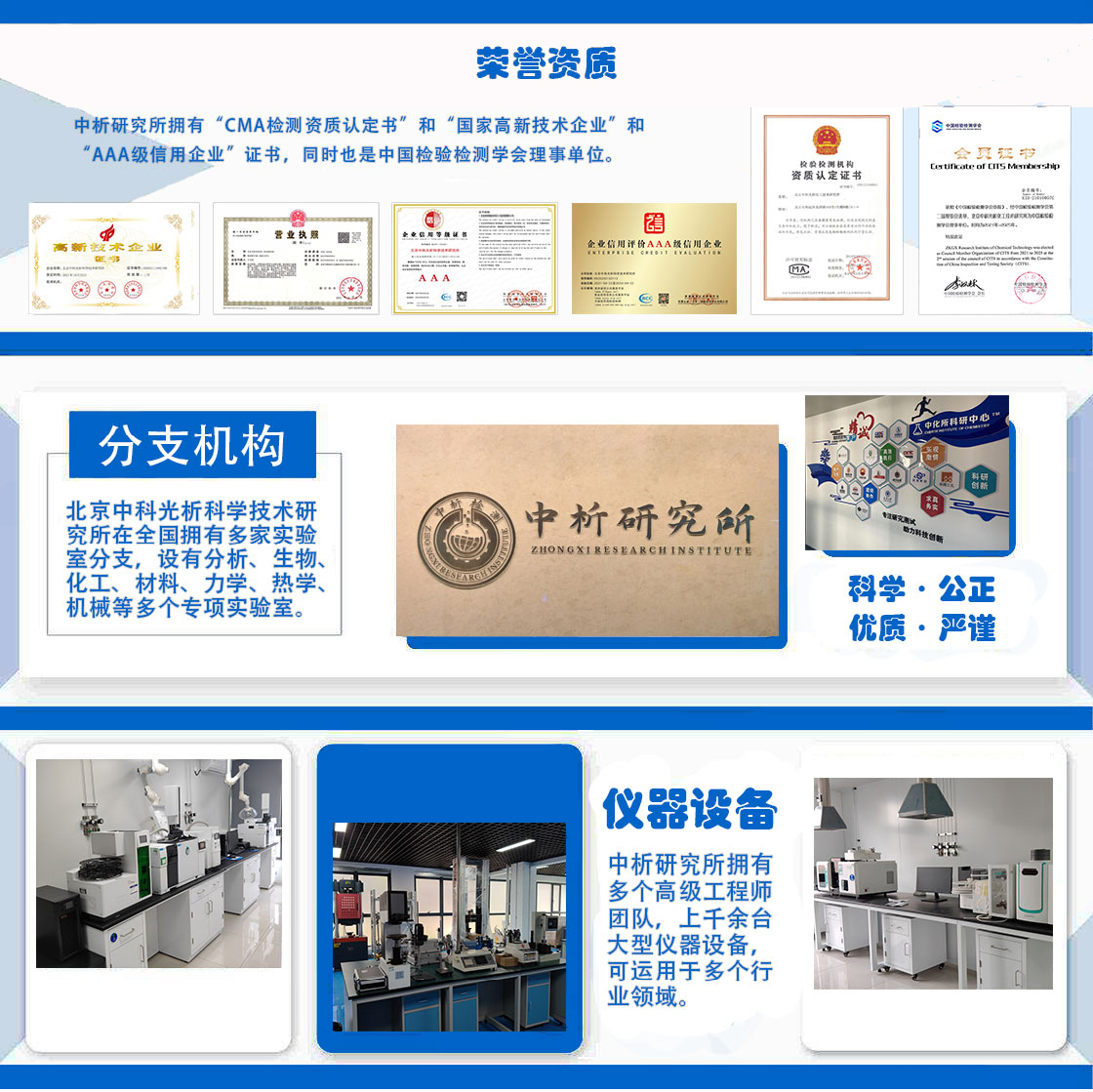
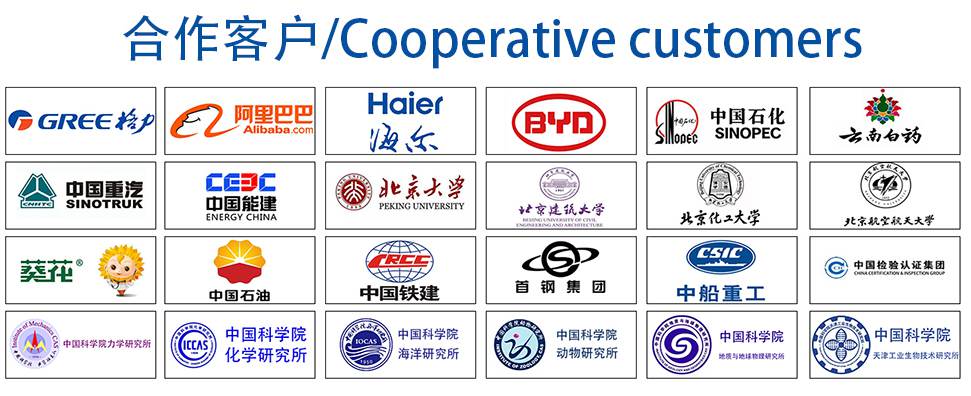