1. 检测背景与意义
2. 核心检测项目及方法
2.1 滤失量测定(核心项目)
- 检测原理:模拟井下高温高压条件,测量悬浮液在特定时间内通过标准滤膜的滤液体积。
- 仪器设备:高温高压滤失仪(如OFITE或Fann品牌)、滤纸(直径9cm,孔隙度2~5μm)、量筒。
- 步骤:
- 将悬浮液注入滤失仪,施加目标压力(通常500 psi)及温度(如150°C)。
- 记录30分钟内的滤液体积(单位:mL)。
- 按API标准计算“API滤失量”(30min滤液量×2)。
- 判定标准:API滤失量≤5mL为优质性能,>15mL需调整配方。
2.2 悬浮液密度(比重)检测
- 目的:确保悬浮液密度满足地层压力平衡需求。
- 方法:采用泥浆比重秤或电子密度计直接测量,单位为g/cm³。
2.3 pH值测定
- 意义:pH影响悬浮液中黏土颗粒的分散性和稳定性。
- 方法:使用pH试纸或数字pH计,控制范围通常为8~10(碱性环境抑制腐蚀)。
2.4 流变参数测试
- 关键参数:塑性黏度(PV)、动切力(YP)、静切力(Gel Strength)。
- 检测仪器:六速旋转黏度计(如Fann 35A)。
- 作用:评估悬浮液的携岩能力和泵送效率。
2.5 沉降稳定性分析
- 方法:将悬浮液静置24小时后,测量上下层密度差。
- 标准:密度差≤0.05g/cm³为合格,否则需添加悬浮剂。
3. 影响因素及优化策略
- 固相颗粒级配:细颗粒(如纳米碳酸钙)可填充滤饼孔隙,降低滤失量。
- 降滤失剂选择:常用聚合物(如CMC、PAC)或树脂类材料,需进行配伍性实验。
- 温度压力适应性:高温会导致聚合物降解,需采用抗温改性剂(如磺化褐煤)。
4. 检测标准与规范
- 国际标准:API RP 13B-1(水基钻井液测试规程)、ISO 10414-1。
- 行业实践:同步检测滤饼厚度(≤2mm)和渗透性(滤饼致密性)。
5.
上一篇:机械采油系统效率检测下一篇:排气流速检测
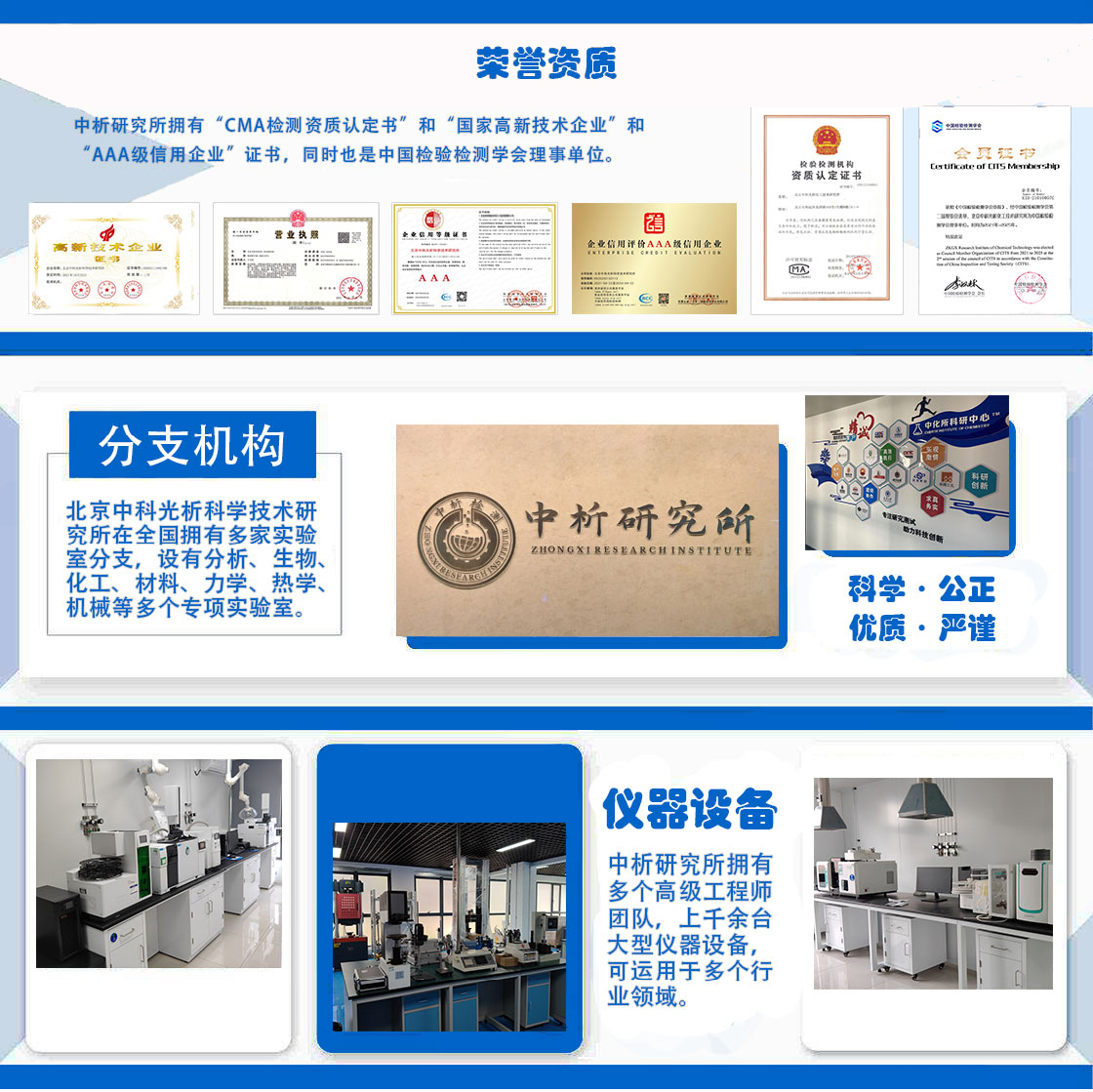
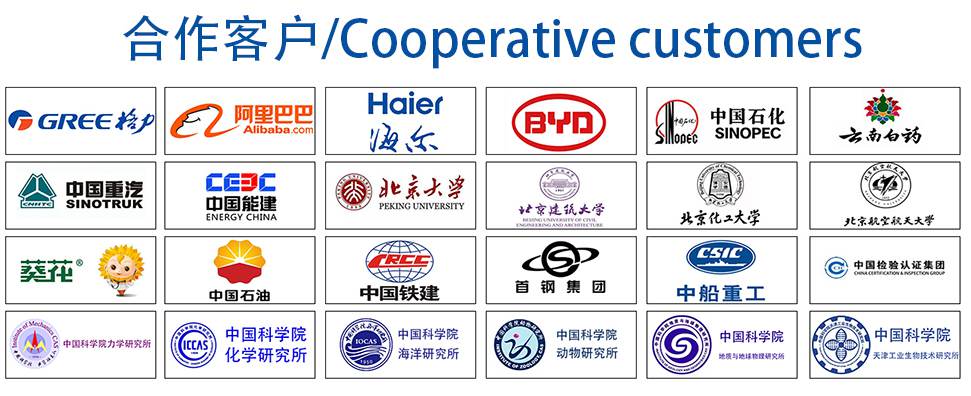
材料实验室
热门检测
254
215
190
203
198
204
210
202
207
217
204
199
204
203
198
195
210
199
209
202
推荐检测
联系电话
400-635-0567