三氧化钼(MoO₃)检测项目详解
一、引言
二、核心检测项目
1. 化学成分分析
(1)主成分含量测定
- 目的:确定MoO₃的纯度(通常要求≥99.5%)。
- 方法:
- 重量法:通过钼酸盐的沉淀反应计算含量;
- X射线荧光光谱(XRF):无损快速测定元素比例;
- 电感耦合等离子体发射光谱(ICP-OES):高精度检测微量杂质。
(2)杂质元素检测
- 关键杂质:Fe、Al、Ca、K、Na、Si等(影响催化活性及电性能);
- 检测手段:
- 原子吸收光谱(AAS)
- ICP-MS(痕量元素分析,检出限低至ppb级)。
2. 物理性质测试
(1)粒度分布
- 意义:粒度影响催化反应效率和材料加工性能。
- 方法:激光粒度分析仪、扫描电镜(SEM)形貌观测。
(2)比表面积与孔径
- 应用关联:高比表面积增强催化剂活性位点。
- 检测技术:氮气吸附-脱附法(BET法)。
(3)密度与熔点
- 标准方法:
- 密度:气体置换法(如氦气比重计);
- 熔点:热分析仪(DSC/TGA)。
3. 结构表征
(1)晶体结构分析
- 方法:X射线衍射(XRD)确定晶型(如α-MoO₃斜方晶系);
- 意义:晶相差异影响光学、电化学性能。
(2)微观形貌
- 手段:扫描电镜(SEM)、透射电镜(TEM)观测表面形貌及颗粒分布。
4. 热稳定性评估
- 检测项目:热分解温度、相变行为。
- 设备:热重分析仪(TGA)、差示扫描量热仪(DSC)。
- 应用:高温环境材料(如电极材料)需优异热稳定性。
5. 电化学性能测试
- 关键参数:电导率、介电常数、电化学阻抗谱。
- 适用领域:锂离子电池电极材料、半导体器件。
- 方法:四探针法测电导率,电化学工作站分析阻抗。
6. 环境与安全指标
(1)重金属溶出量
- 标准:符合RoHS、REACH等法规;
- 方法:酸浸提后ICP-MS检测。
(2)粉尘爆炸性
- 意义:粉末状MoO₃需评估生产储存安全性;
- 测试:粉尘爆炸极限测定(依据GB/T 16425)。
三、检测标准与规范
- 国际标准:ASTM E394(钼含量测定)、ISO 10276(核级MoO₃规范);
- 国内标准:GB/T 3469-2022(工业三氧化钼)。
四、应用场景与检测关联
- 催化剂:侧重纯度、比表面积、杂质含量;
- 电子材料:关注电导率、晶体结构;
- 环保材料:需通过重金属溶出测试。
五、总结
上一篇:射线检测(RT)检测下一篇:粘度效应(加入硫酸钙后)检测
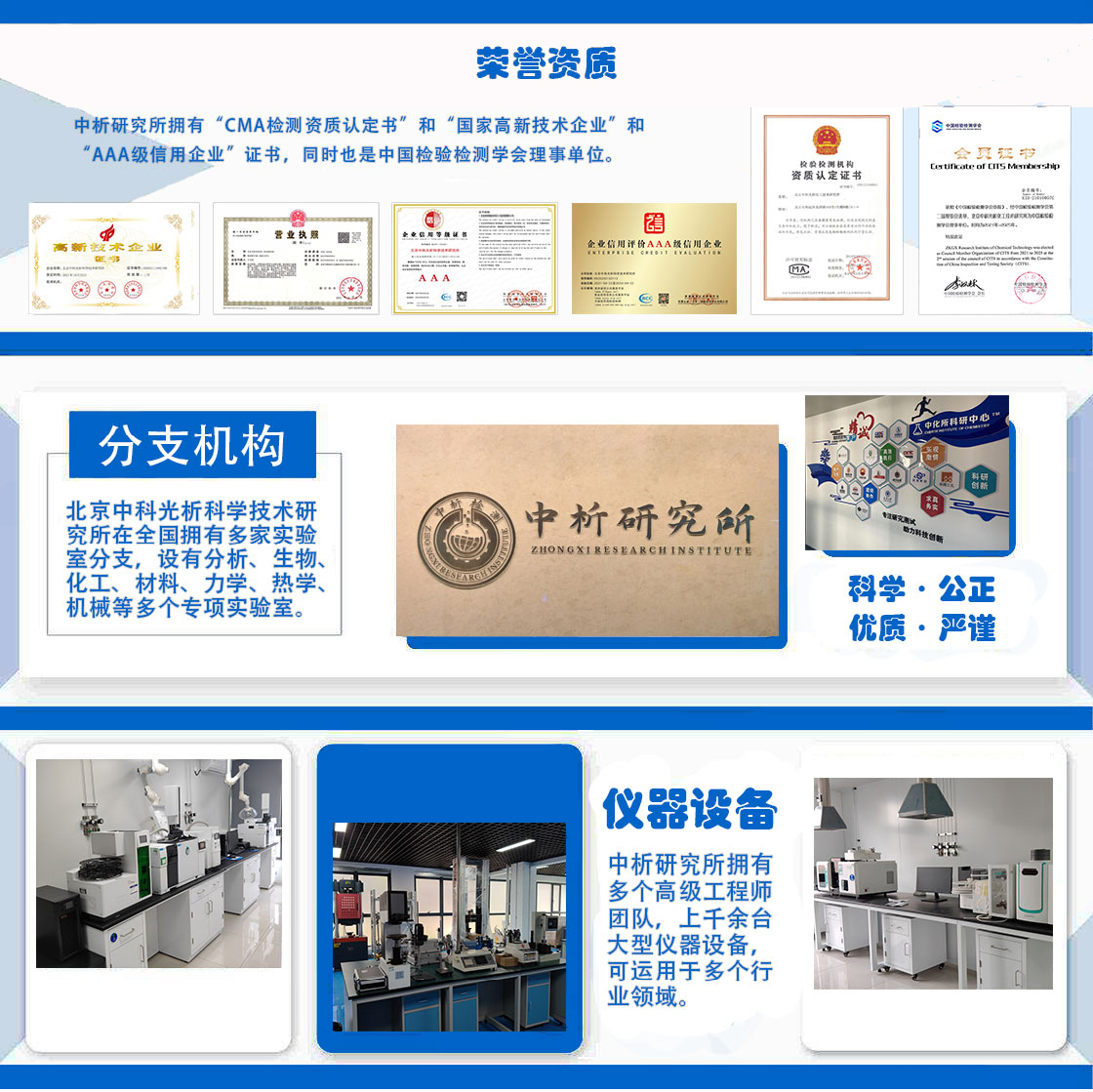
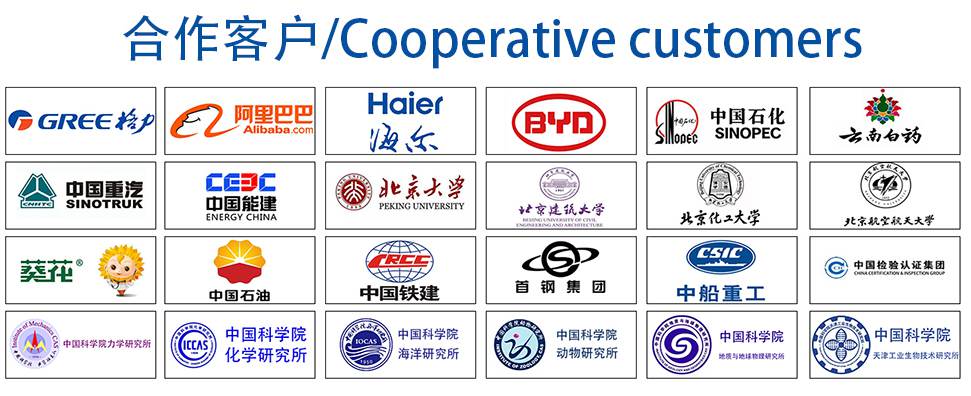
材料实验室
热门检测
254
215
189
203
197
204
209
201
207
217
203
199
198
203
197
195
209
199
209
202
推荐检测
联系电话
400-635-0567