粘度效应(加入硫酸钙前)检测:关键检测项目与流程
一、检测目的
- 确定原料或基础液体的初始粘度特性。
- 为后续添加硫酸钙后的粘度变化提供基准数据。
- 评估流体在不同条件下的流变行为,预测工艺可行性。
二、检测仪器与试剂
- 主要仪器:
- 旋转粘度计(如Brookfield粘度计)
- 流变仪(分析粘弹性)
- 恒温水浴槽(控制温度)
- 精密天平(样品称量)
- 试剂与样品:
- 待测流体(未添加硫酸钙的原料体系)
- 标准校准液(验证仪器精度)
三、核心检测项目
1. 基础粘度测定
- 检测方法: 使用旋转粘度计在特定转速(如20-100 rpm)下测量流体的动态粘度(单位:mPa·s 或 cP)。
- 测试条件:
- 温度控制(如25±0.5℃)
- 剪切速率范围选择(模拟实际工艺条件)
- 数据记录: 记录不同剪切速率下的粘度值,绘制流变曲线(剪切应力 vs. 剪切速率)。
2. 流变特性分析
- 检测目标: 判断流体为牛顿流体或非牛顿流体(如假塑性、触变性)。
- 测试方法: 通过流变仪执行以下测试:
- 稳态剪切测试:获取粘度随剪切速率变化的规律。
- 动态振荡测试:分析储能模量(G')和损耗模量(G''),评估流体弹性与粘性占比。
3. 温度依赖性测试
- 检测意义: 温度对粘度影响显著,需明确待测流体的温度-粘度关系。
- 实验步骤: 在恒温水浴中调节样品温度(如10℃、25℃、40℃),分别测量粘度值,绘制温度-粘度曲线。
4. 流体稳定性测试
- 检测内容:
- 静置稳定性:将样品静置24-48小时,观察是否分层或沉降,并复测粘度变化。
- 机械稳定性:高速搅拌后立即测量粘度,验证流体抗剪切破坏能力。
5. 重复性与误差分析
- 检测要求: 同一批次样品重复测量3-5次,计算相对标准偏差(RSD),验证数据可靠性。
- 误差控制: 校准仪器、控制环境温湿度、避免气泡干扰。
6. 数据对比与报告
- 输出内容: 将检测结果与行业标准或历史数据进行对比,形成包含以下内容的报告:
- 初始粘度值范围
- 流体类型(牛顿/非牛顿)
- 温度敏感性系数
- 稳定性评级
四、注意事项
- 样品制备:确保样品均匀无气泡,必要时进行脱气处理。
- 仪器校准:每次检测前使用标准硅油或甘油校准粘度计。
- 环境控制:避免震动、温度波动对测量的干扰。
- 记录细节:注明测试时间、操作人员、仪器型号等追溯信息。
五、
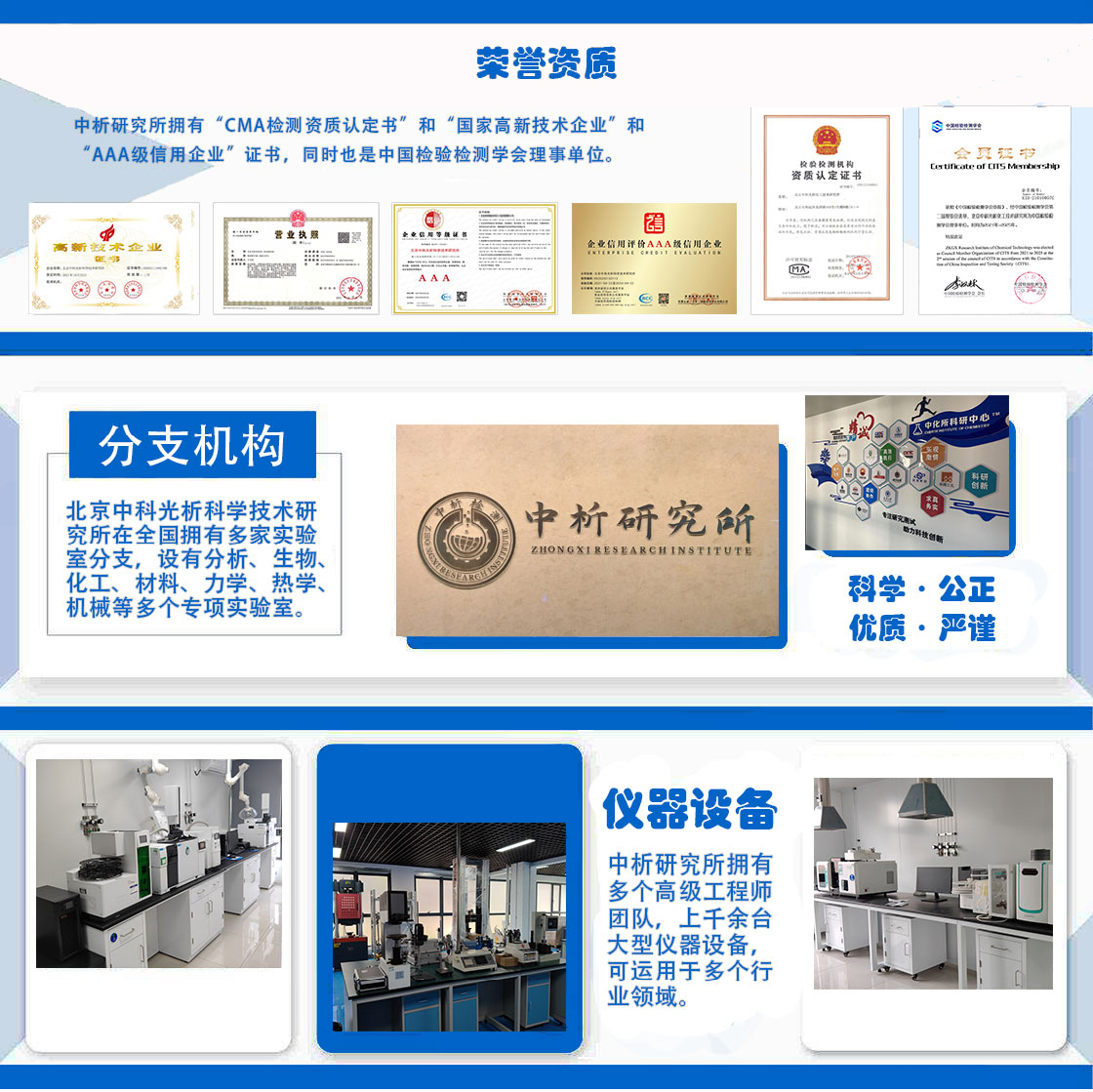
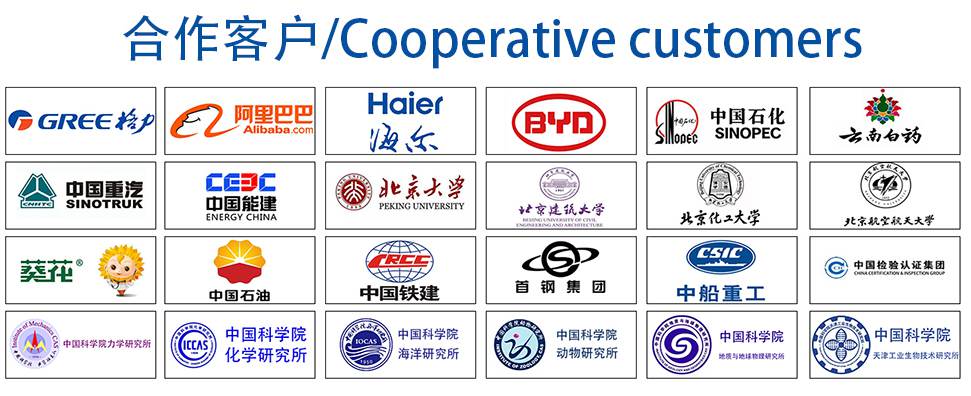
材料实验室
热门检测
262
220
199
207
200
205
215
208
215
220
207
206
211
208
200
198
213
202
211
206
推荐检测
联系电话
400-635-0567