机械采油系统效率检测项目及关键技术
引言
一、检测项目分类
1. 地面设备检测
(1) 电动机系统
- 输入电能参数:电压、电流、功率因数、有功功率、无功功率等;
- 电动机效率:通过空载、负载试验计算电机效率曲线;
- 负载率匹配度:实际负载与额定功率的匹配合理性;
- 谐波干扰:检测电网谐波对电机性能的影响。
(2) 减速箱与传动装置
- 扭矩与转速:输入轴与输出轴的扭矩差值计算传动效率;
- 机械损失:皮带传动滑差率、齿轮箱摩擦损失;
- 润滑状态:油温、油压及润滑剂性能影响检测。
(3) 平衡系统
- 平衡度测试:游梁式抽油机的平衡块位置与电流变化曲线分析;
- 惯性载荷:曲柄平衡与游梁平衡的协调性。
2. 井下设备检测
(1) 抽油杆系统
- 载荷分布:通过示功图检测光杆载荷、悬点位移;
- 杆柱应力:弯曲、振动导致的疲劳损耗分析;
- 杆管摩擦:井斜段或结蜡井的摩擦阻力检测。
(2) 抽油泵性能
- 泵效计算:实际排量与理论排量的比值(需结合液面恢复测试);
- 漏失量检测:固定阀、游动阀的密封性及间隙磨损;
- 气锁/液击:含气井的气体影响或液击振动信号分析。
3. 系统综合效率
- 系统输入功率:电动机输入电能总和;
- 有效功率输出:液体提升至地面所做的有效功;
- 系统效率计算:有效功率/输入功率×100%(行业标准SY/T 5264-2012)。
二、检测方法
1. 直接测量法
- 使用功率分析仪、扭矩传感器、载荷传感器等设备实时采集数据;
- 示功图诊断技术结合电参数分析。
2. 间接计算法
- 通过液面恢复测试推算泵效;
- 基于电机特性曲线估算传动效率。
3. 测试标准
- 遵循《SY/T 5264-2012 机械采油系统效率测试方法》;
- 国际对标API RP 11L(游梁式抽油机设计推荐做法)。
三、数据分析与优化建议
-
- 低泵效(<40%):检查气锁、结蜡、泵漏失;
- 电机负载率低(<30%):调整冲次或更换小功率电机;
- 传动损耗过高:更换高效皮带、优化减速箱润滑。
四、
上一篇:粘度效应(加入硫酸钙后)检测下一篇:饱和盐水悬浮液滤失量检测
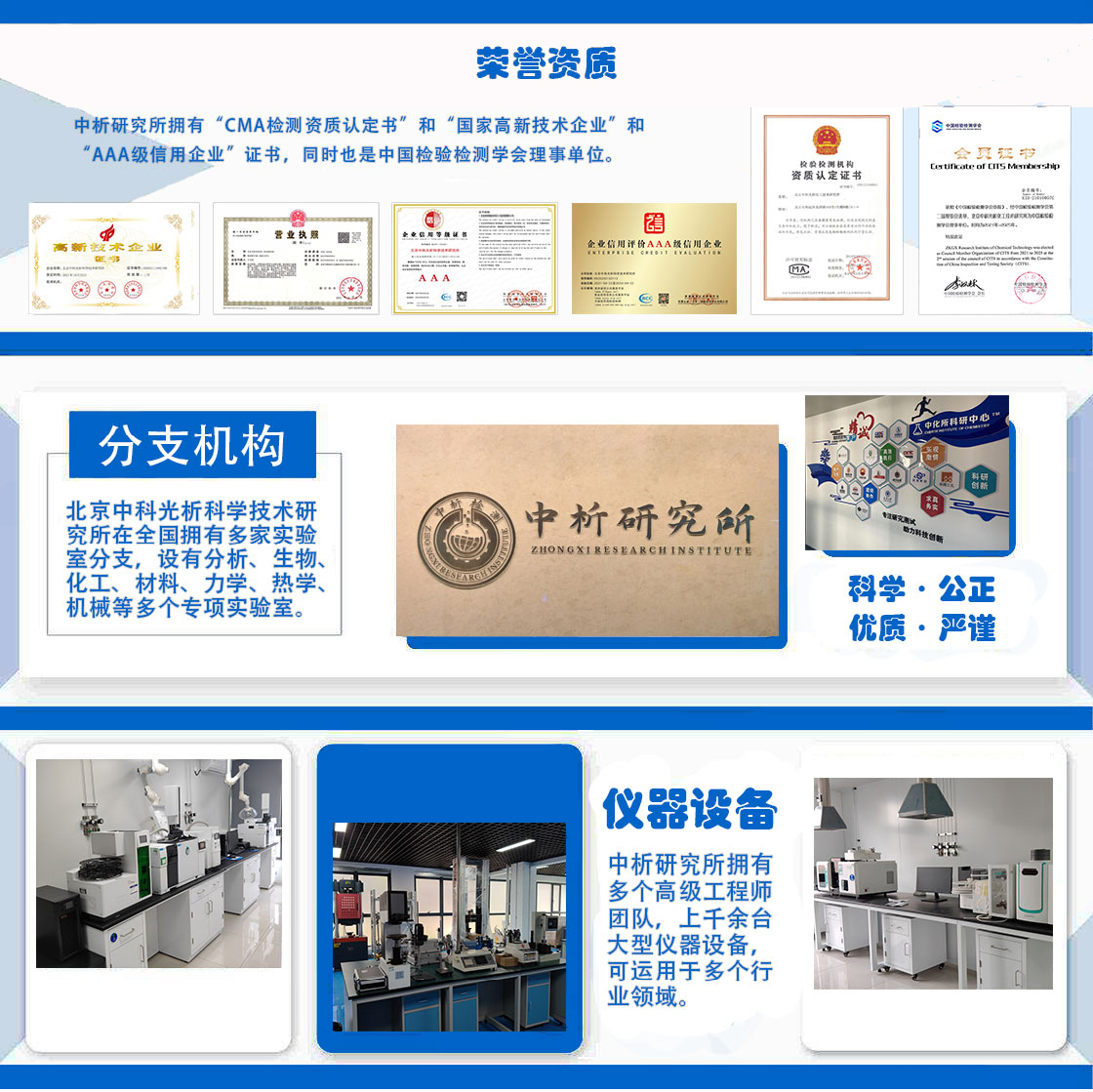
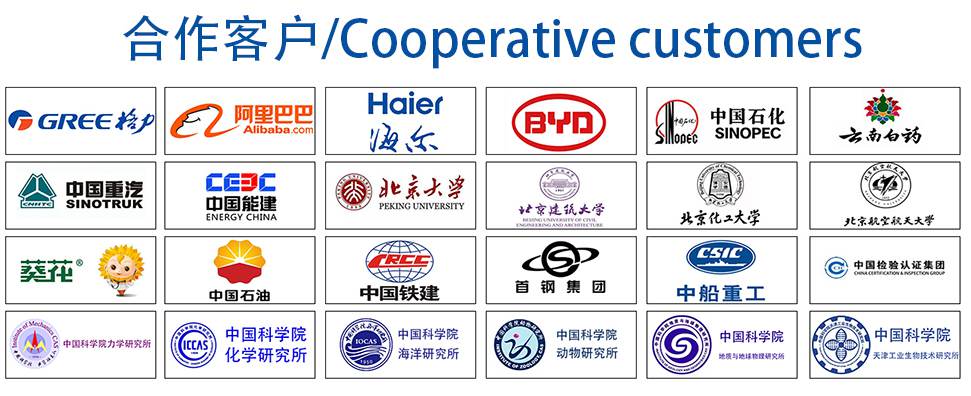
材料实验室
热门检测
254
215
189
203
197
204
209
201
207
217
203
199
198
203
197
195
209
199
209
202
推荐检测
联系电话
400-635-0567