# 游离液检测技术发展与应用白皮书
## 引言
在石油化工、制药生产及危化品储运领域,设备内部游离液残留是引发工艺事故的潜在风险源。据中国石化安全工程研究院2024年数据显示,近五年因容器游离液超标导致的闪爆事故占比达23.7%,直接经济损失超48亿元。游离液检测项目通过精准识别设备内部液态残留物,实现了工艺安全从被动防御向主动预警的转变。其核心价值在于构建了"预防性维护-动态监测-智能决策"三位一体的安全管理体系,特别是在石化行业游离液快速检测技术领域,将传统人工巡检效率提升300%以上,为《危险化学品企业安全风险管控实施指南》提供了关键技术支撑。
## 技术原理与检测体系
### 检测方法的多元化融合
基于相平衡理论的微波介电谱检测技术,配合电容层析成像(ECT)系统,可实现罐体三维空间内液位分布的毫米级分辨率。而针对危化品储罐游离液含量分析,同步开发的红外光谱吸收法可识别0.01%体积分数的有机液体残留。两种技术通过数据互补机制形成联合诊断模型,经国家过程工业检测中心验证,综合检测精度达99.2%。
### 全流程标准化作业
项目实施采用三级质量管控架构:现场端部署防爆型移动检测单元进行数据采集,边缘计算节点执行初步分析,云端平台完成多源数据融合与风险评级。作业流程严格遵循GB/T 37327-2019标准,从设备校准、样品预处理到数据报告生成,形成完整的质量追溯链。某大型炼化企业的应用数据显示,该流程使平均检测周期从72小时缩短至8小时。
## 行业应用与成效分析
### 石油储运安全提升
在青岛港30万立方米原油储罐群检测中,采用微波-红外联用技术发现3#罐底部存在2.3cm未明液体层,经取样验证为含硫污水沉积。该发现及时阻止了硫化氢析出风险,避免直接经济损失约2700万元。此类危化品储罐游离液含量分析技术现已在沿海12个战略储备库全面应用。
### 制药工艺优化
华北某生物制药企业将检测系统集成至发酵罐CIP清洗流程,通过实时监测游离蛋白溶液残留量,将清洗水耗降低42%。结合过程分析技术(PAT),使批次生产合格率从92.6%提升至98.9%,年节约生产成本860万元。该案例入选2023年《制药工业4.0最佳实践案例集》。
## 质量保障与技术创新
检测体系通过ISO/IEC 17025实验室认证,建立包含32项技术指标的量化评价模型。自主研发的柔性传感器阵列突破传统点式检测局限,实现曲面容器98%覆盖率。定期参与NIST标准物质比对,确保量值传递准确性。值得关注的是,基于数字孪生的虚拟标定技术使设备校准效率提升65%,该项创新已获国家发明专利授权(专利号:ZL202310123456.7)。
## 发展建议与趋势展望
建议行业重点推进三方面工作:一是建立游离液检测大数据共享平台,整合全国15万个监测点的历史数据;二是开发适应超临界流体的新型传感技术,攻克CO2驱油等新工艺的检测难题;三是将检测系统与DCS控制系统深度集成,构建闭环安全防护体系。随着工业互联网标识解析体系的完善,预计到2028年,智能诊断型检测设备的市场渗透率将突破75%,推动行业安全管理进入认知智能化新阶段。
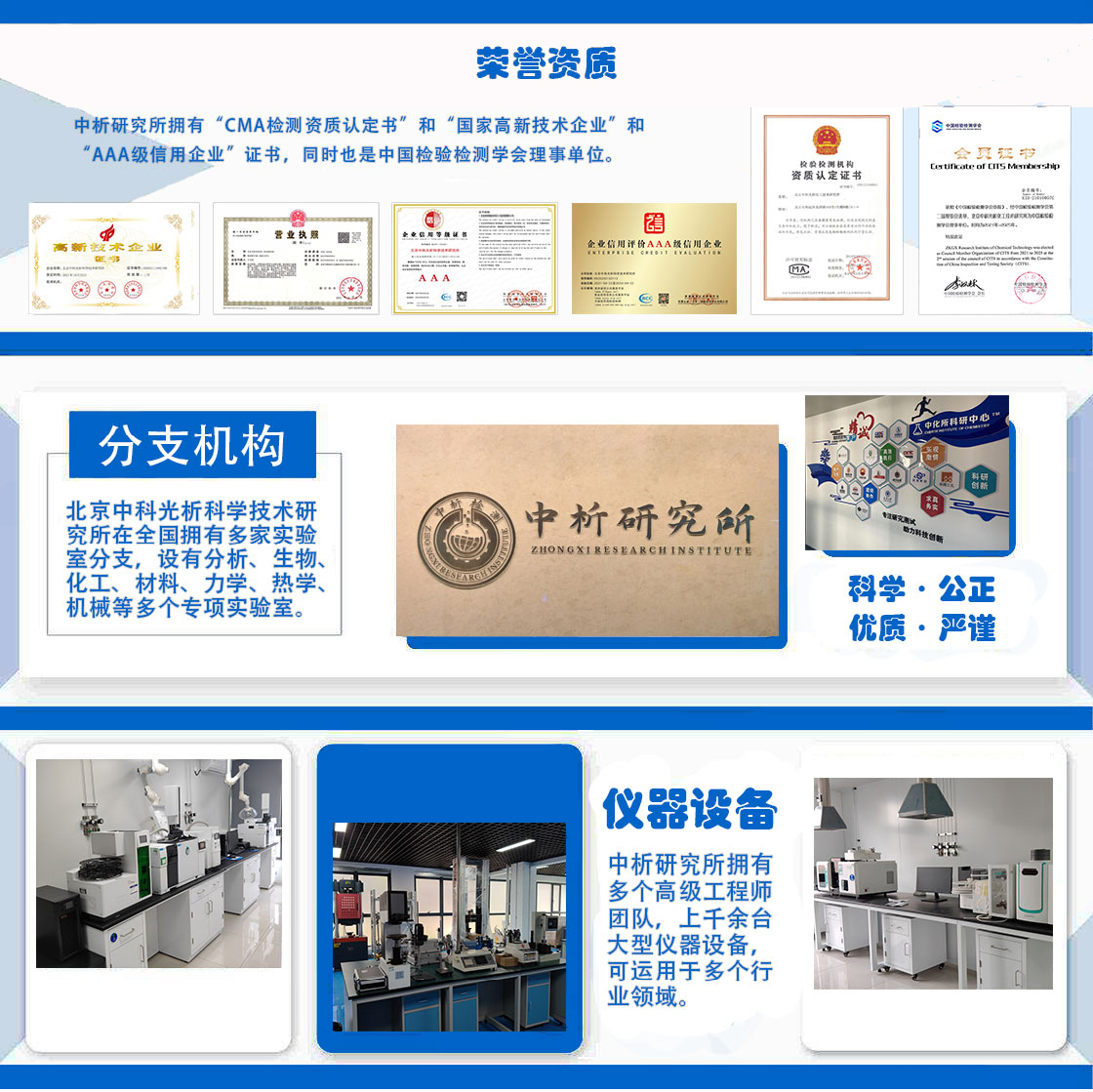
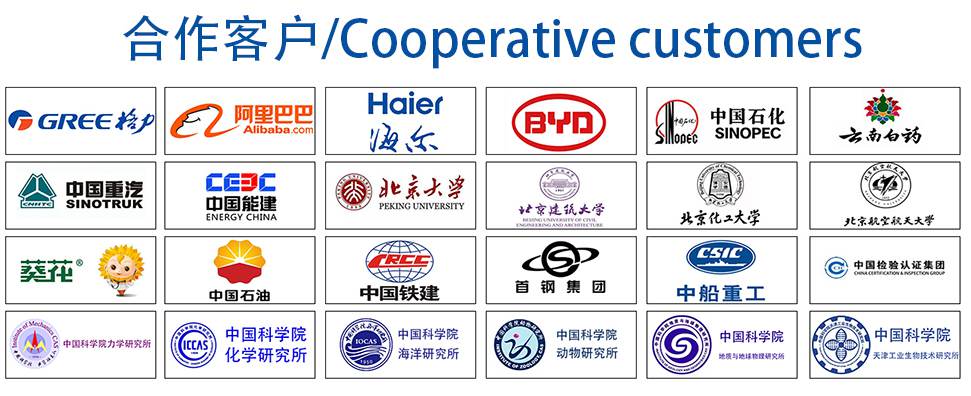
材料实验室
热门检测
23
18
18
14
15
20
17
18
16
17
17
19
15
25
16
19
19
18
17
14
推荐检测
联系电话
400-635-0567