射线检测(RT)技术详解:核心检测项目与应用领域
一、RT检测的核心技术原理
- 射线能量:根据材料厚度选择X射线机电压或γ射线源种类(如Ir-192、Co-60)。
- 灵敏度:通常要求达到2%以上,通过像质计(IQI)验证。
- 几何不清晰度:控制焦点尺寸与工件距离,避免图像模糊。
二、RT检测的核心项目分类
1. 焊接质量检测
- 适用对象:管道环焊缝、压力容器对接焊、钢结构焊缝等。
- 检测缺陷:
- 体积型缺陷:气孔、夹渣、未熔合。
- 面积型缺陷:裂纹、未焊透。
- 标准规范:
- ISO 17636(金属材料焊接的射线检测)
- ASME Boiler and Pressure Vessel Code Section V
- GB/T 3323(中国国家标准)
- 典型应用:
- 油气长输管道环焊缝检测(壁厚≥8mm时优先采用RT)。
- 核电设备安全壳焊接接头全数检测。
2. 铸件与锻件内部缺陷检测
- 适用对象:发动机缸体、阀门铸件、风电主轴锻件等。
- 检测缺陷:
- 缩孔、疏松、冷隔(铸件)。
- 白点、折叠、偏析(锻件)。
- 技术要点:
- 铸件检测需采用低能量射线提高对比度。
- 锻件检测需多角度透照以捕捉分层缺陷。
- 案例参考:
- 航空航天钛合金铸件的X射线检测,分辨率要求≤1%厚度。
3. 在役设备腐蚀与壁厚测量
- 适用对象:化工管道、储罐、锅炉受热面。
- 检测内容:
- 均匀腐蚀导致的壁厚减薄。
- 局部腐蚀坑或沟槽缺陷。
- 技术方法:
- 数字射线测厚(DR技术):通过灰度值分析实时计算剩余壁厚。
- 双壁单影法:用于小直径管道的周向腐蚀检测。
4. 复合材料与电子元件检测
- 适用对象:碳纤维复材结构件、PCB电路板、封装芯片。
- 检测难点:
- 低密度材料(如塑料)需微焦点X射线(<5μm焦点)提高分辨率。
- 多层结构需采用层析成像(CT)技术分离不同深度的缺陷。
- 典型应用:
- 航空复材蒙皮的分层、孔隙率检测(ASTM E2737)。
- BGA焊点虚焊、空洞的3D成像分析。
5. 特殊结构与复杂组件检测
- 适用对象:
- 航空航天发动机涡轮叶片冷却孔。
- 核反应堆燃料棒封装完整性。
- 创新技术:
- 中子射线照相:检测含氢材料(如橡胶密封圈)的缺陷。
- 高能直线加速器:用于厚钢构件(如300mm以上铸锭)的检测。
三、RT检测的标准流程与关键控制点
-
- 清理检测表面,去除飞溅、氧化皮。
- 选择射线源(如X射线机能量、γ源活度)和胶片类型(如D4、D7)。
-
- 确定透照角度(单壁透照或双壁透照)。
- 布置像质计(IQI)和标记带,确保可追溯性。
-
- 计算曝光参数(如焦距、管电流、时间)。
- 数字成像(DR/CR)实时监控图像质量。
-
- 根据标准(如EN 1435)分级缺陷(圆形缺陷、条形缺陷)。
- 使用图像处理软件(如DICONDE)进行对比度增强和尺寸测量。
四、RT检测的局限性与应对策略
-
- 需严格屏蔽辐射,采用遥控操作和区域监控系统。
-
- 传统胶片法耗时较长,数字RT(DR)可提速50%以上。
-
- 对平行于射线方向的裂纹检出率低,需结合超声检测(UT)互补。
五、未来发展趋势
- 智能化:AI辅助缺陷识别(如深度学习算法分类气孔与夹渣)。
- 高精度成像:纳米焦点CT(分辨率达0.5μm)用于微电子器件。
- 绿色技术:低剂量实时成像系统减少辐射暴露。
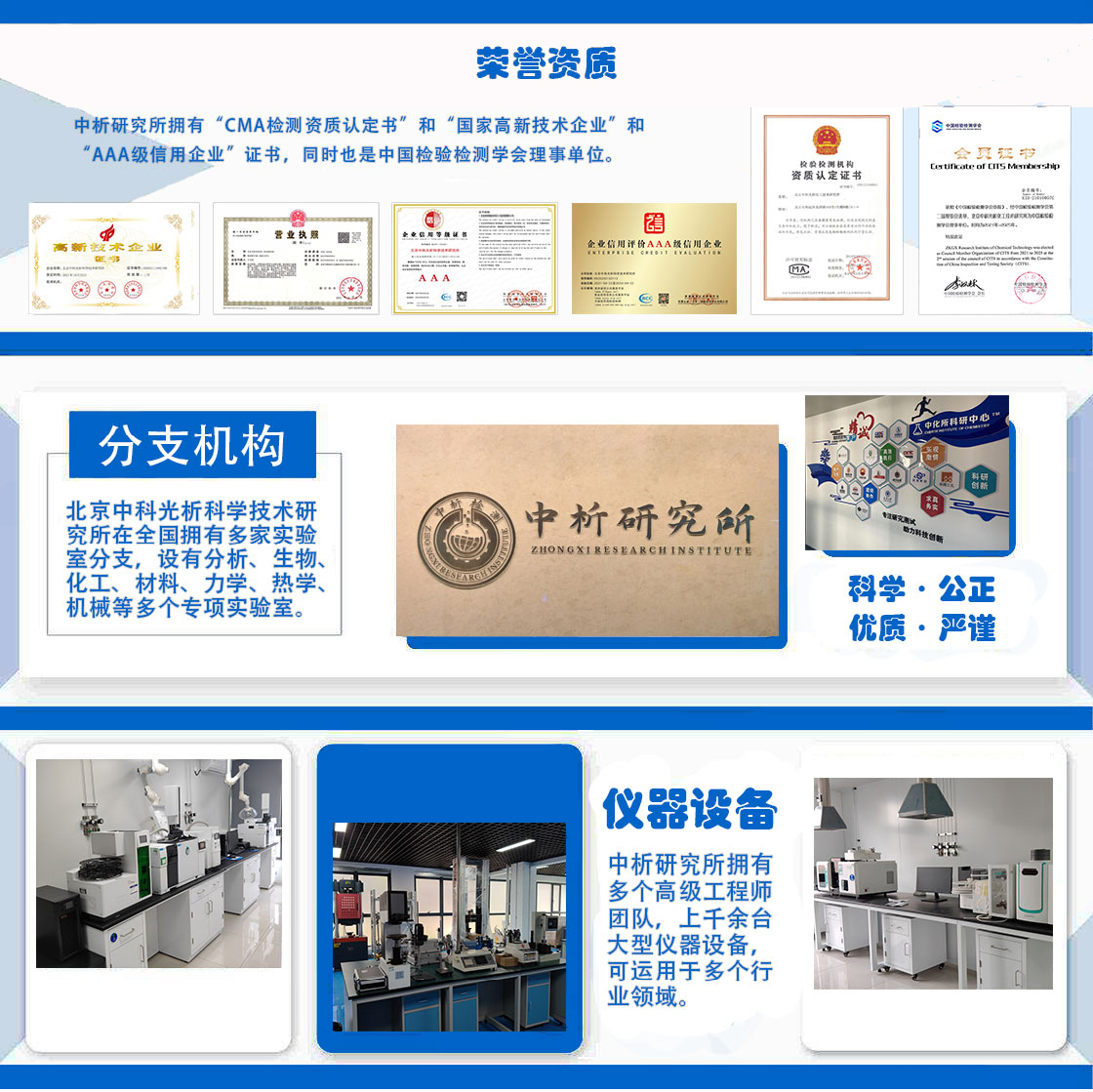
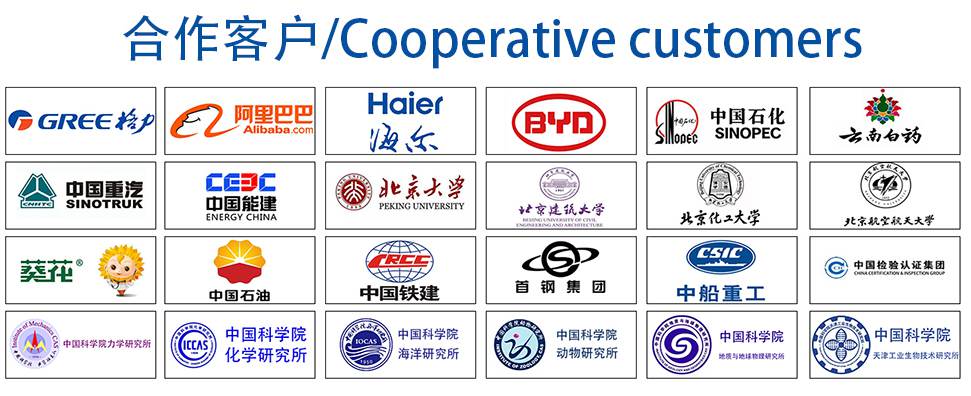
材料实验室
热门检测
254
215
190
203
198
204
210
202
207
217
204
199
204
203
198
195
210
199
209
202
推荐检测
联系电话
400-635-0567