外圆磨床检测的重要性与核心目标
外圆磨床作为精密机械加工的核心设备,广泛用于轴类、圆柱形工件的高精度磨削加工。其加工精度直接影响零部件的尺寸公差、表面粗糙度及几何形态,进而决定机械产品的装配质量与使用寿命。然而,长期运行中,机床导轨磨损、主轴跳动异常、砂轮系统失衡等问题会逐渐显现。因此,定期开展系统性检测是保障设备性能、预防加工缺陷的关键环节。外圆磨床检测的核心目标包括:验证设备精度是否符合ISO或行业标准(如JIS B6336)、识别潜在机械故障、优化加工参数以及延长关键部件寿命。通过科学的检测流程,可降低废品率30%以上,避免非计划停机造成的生产成本激增。
外圆磨床检测项目及技术要求
1. 主轴系统精度检测
使用千分表与标准验棒测量主轴径向跳动(≤0.002mm)和轴向窜动(≤0.0015mm),配合激光干涉仪分析转速波动对动态精度的影响。需特别注意轴承温升不超过45℃,避免润滑油膜失效导致的精度劣化。
2. 导轨几何精度检测
采用电子水平仪和直尺检测床身导轨的直线度(全长≤0.015mm/m)、平行度(≤0.01mm/1000mm)及扭曲度。对于静压导轨需额外监测油膜压力均匀性,确保误差值在±5%以内。
3. 砂轮系统动平衡检测
通过振动传感器与频谱分析仪评估砂轮组件的不平衡量,要求残余振动速度≤1.5mm/s(按ISO 1940-1标准)。首次安装或修整后必须执行动平衡校正,避免因离心力引发的工件振纹。
4. 进给机构定位精度检测
利用步距规和激光干涉仪校验X/Z轴定位精度(±2μm/300mm)、重复定位精度(±1μm),同步检测滚珠丝杠反向间隙(≤0.005mm)。数控系统需进行螺距补偿参数优化。
5. 冷却与过滤系统效能检测
检测磨削液流量(≥20L/min)、过滤精度(≤10μm)及PH值(7.5-9.0),防止工件热变形或表面锈蚀。每月需清理磁性分离器与纸带过滤装置,确保杂质去除率>95%。
检测数据管理与预防性维护策略
建立数字化检测档案,通过趋势分析预判部件寿命周期(如砂轮主轴轴承建议每8000小时更换)。实施TPM全员生产维护制度,结合振动监测、油液分析等技术手段,将故障停机率降低至1%以下。关键:外圆磨床检测需形成“测量-分析-改进”闭环,以数据驱动设备健康管理,最终实现加工质量与生产效率的双重提升。
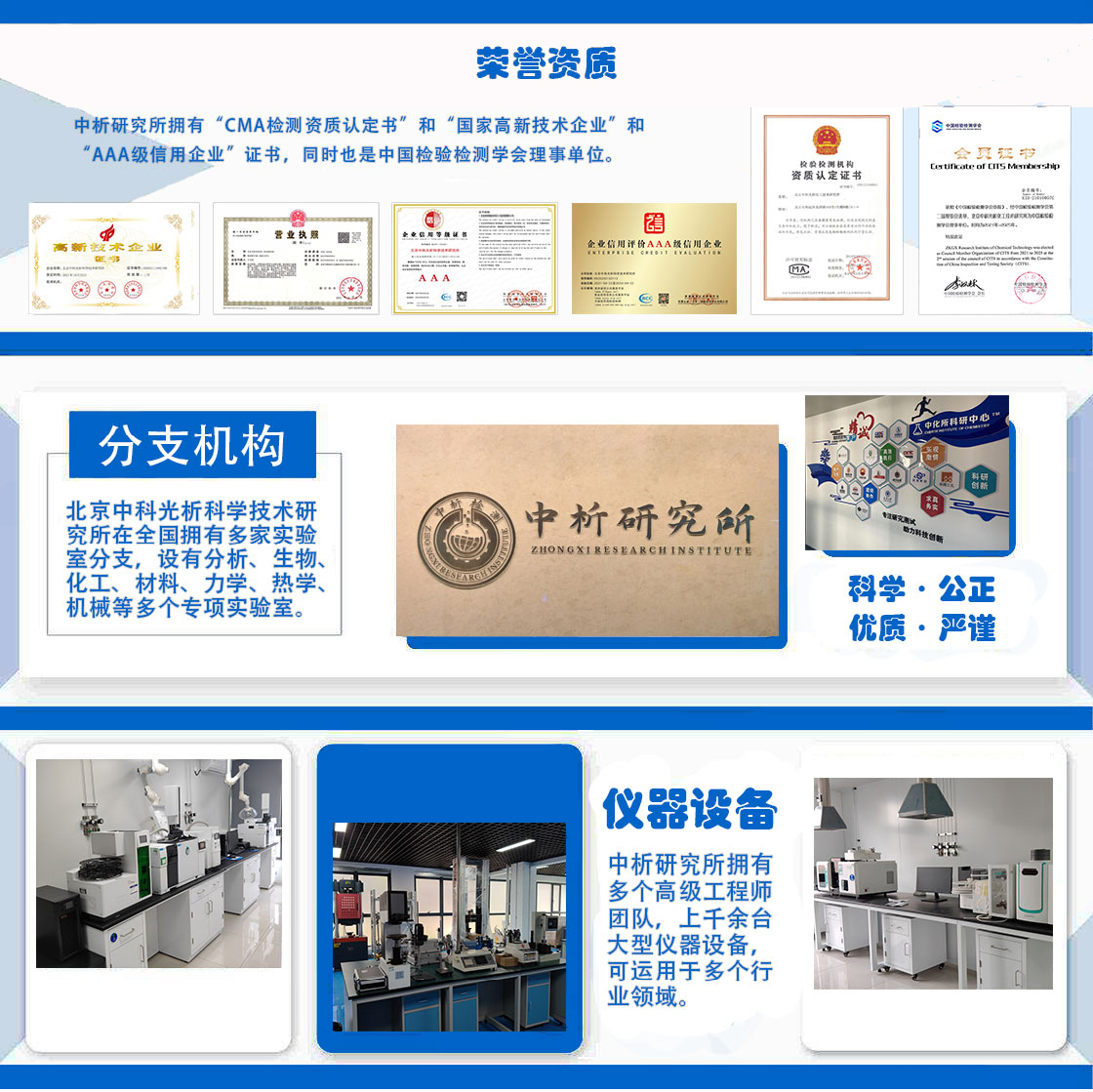
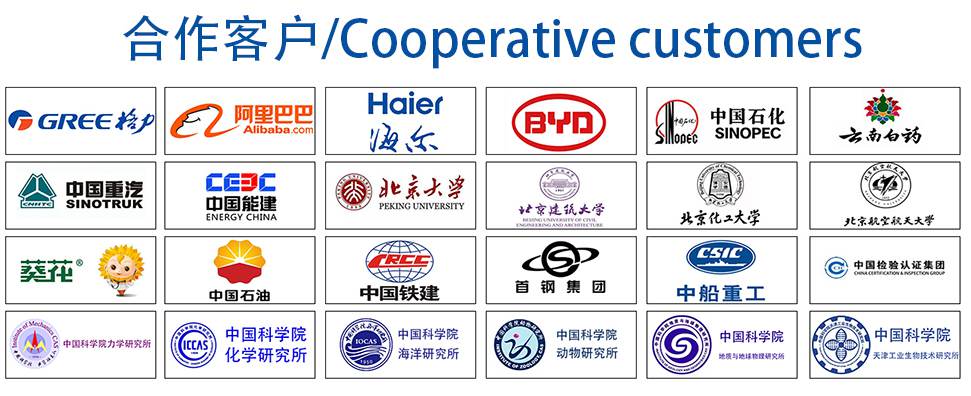