一、基础性能检测
-
- 表面质量:检查硫化后的补带表面是否平整光滑,无气泡、杂质、裂纹或分层现象。微小瑕疵可能导致局部电场集中或机械强度下降。
- 尺寸公差:测量补带厚度、宽度及修复区域长度,偏差需符合GB/T 2951标准(如厚度误差≤±0.2mm)。
- 边缘贴合度:观察补带与电缆护套的过渡区域是否平滑,避免因边缘翘起引发后续磨损。
-
- 拉伸强度与断裂伸长率:按GB/T 528标准,将补带制成哑铃形试样,测试其拉伸强度(通常要求≥10MPa)和断裂伸长率(≥300%),确保补带具备与原生护套相近的柔韧性和抗拉能力。
- 硬度测试:使用邵氏硬度计检测补带硫化后的硬度(参考值:60~80 Shore A),硬度过高可能导致脆裂,过低则易变形。
- 耐磨性试验:模拟电缆拖动工况,通过旋转磨耗仪测试补带的磨损量,确保其耐机械摩擦性能。
二、硫化工艺关键参数验证
-
- 使用温度记录仪全程监控硫化过程,确保温度曲线符合材料要求(通常为150~160℃),避免欠硫(强度不足)或过硫(老化脆化)。
- 验证硫化时间与设备压力参数的匹配性,保证胶料充分交联。
-
- 剥离强度测试:按GB/T 2791标准,将补带与电缆护套剥离,测试界面粘接力(一般要求≥4kN/m)。界面粘接不良会导致水分或瓦斯渗透。
- 显微观察:采用电子显微镜或光学显微镜观察粘接界面,确保无空隙、分层,胶料与护套形成化学键合。
三、电气安全性能检测
-
- 绝缘电阻:使用500V兆欧表测量补带区域绝缘电阻(≥100MΩ·km),确保修复后电缆绝缘性能恢复。
- 工频耐压:对修复段施加2.5kV电压(持续5分钟),监测是否发生击穿或漏电现象。
-
- 通过高频电流传感器检测补带区域在额定电压下的局部放电量(≤10pC),评估绝缘层内部缺陷。
四、耐环境老化性能测试
-
- 耐油性:将补带试样浸泡于煤油或柴油中(70℃×24h),测试其体积变化率(≤20%)和力学性能保留率(≥80%)。
- 耐酸碱性:模拟矿井水环境(pH 3~11溶液浸泡48h),观察表面是否溶胀、剥落。
-
- 按GB/T 2423.22标准,进行-40℃(2h)→+90℃(2h)循环10次,检测补带是否开裂或与护套脱离。
-
- 将试样置于85℃、85%RH环境中加速老化168小时,评估拉伸强度与伸长率的变化率(≤30%)。
五、特殊工况模拟测试
-
- 依据MT 386标准,对补带进行酒精喷灯燃烧试验,要求移开火源后30秒内自熄,且烧损长度≤50mm。
-
- 测量补带表面电阻率(≤1×10^8Ω),避免静电积聚引发瓦斯爆炸。
-
- 模拟电缆卷绕收放,将修复段绕经3倍电缆直径的滚筒弯曲100次,检测补带是否开裂或脱粘。
六、使用寿命评估
-
- 通过高温加速老化实验(如100℃×720h),推算补带在常温下的使用寿命(通常要求≥5年)。
-
- 对修复段施加周期性机械应力(如拉伸-松弛循环),记录失效周期数以评估实际工况下的耐久性。
七、检测标准与认证
- 核心标准:GB/T 7594.7(电线电缆橡皮绝缘和橡皮护套)、MT/T 816(矿用电缆热补带技术条件)、IEC 60502(电力电缆试验方法)。
- 认证要求:需通过MA(煤矿安全认证)、阻燃认证及第三方检测机构(如煤炭科学研究总院)的型式试验。
结语
上一篇:抗拉性能检测下一篇:矿用输送带整体带芯检测
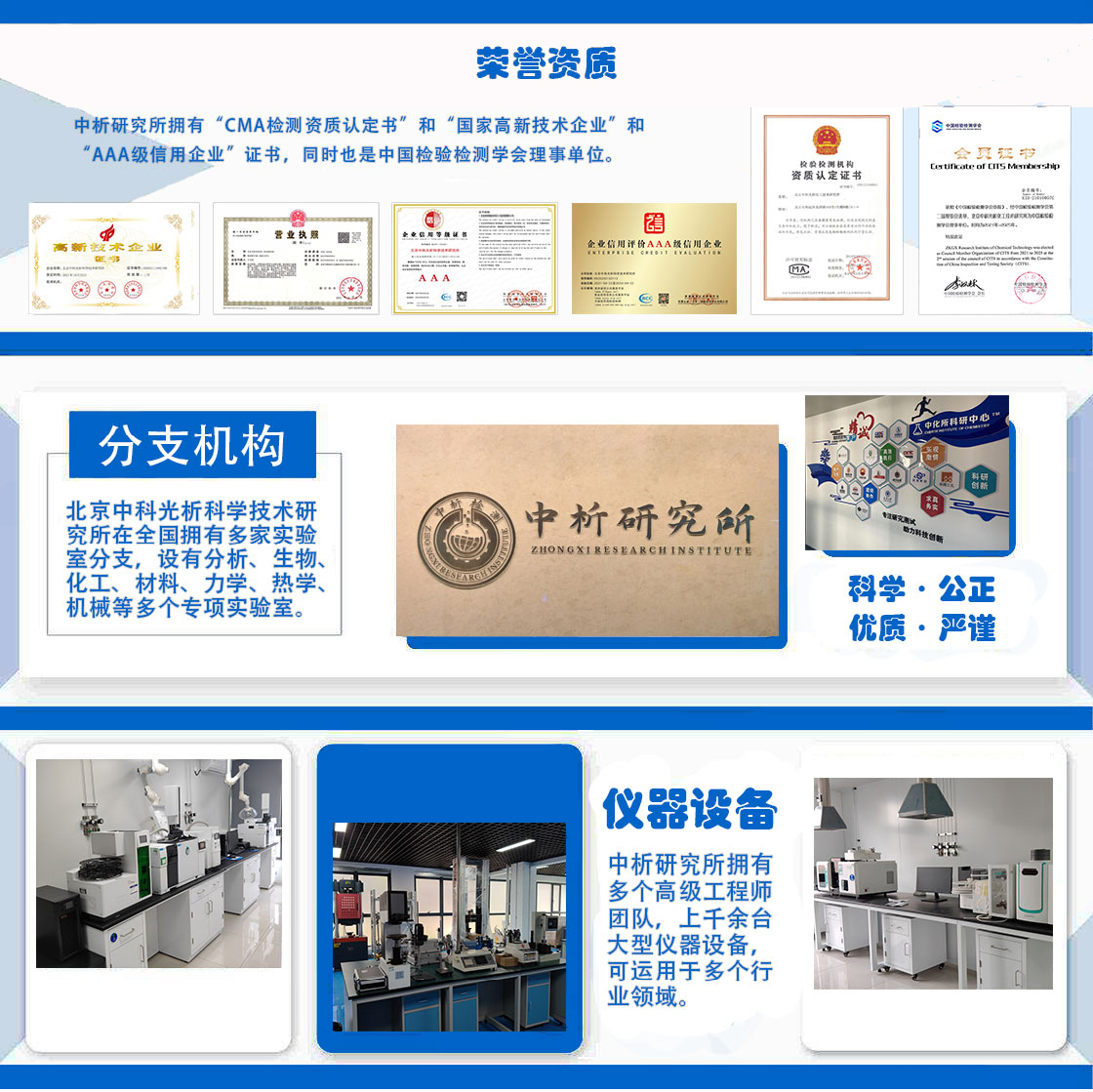
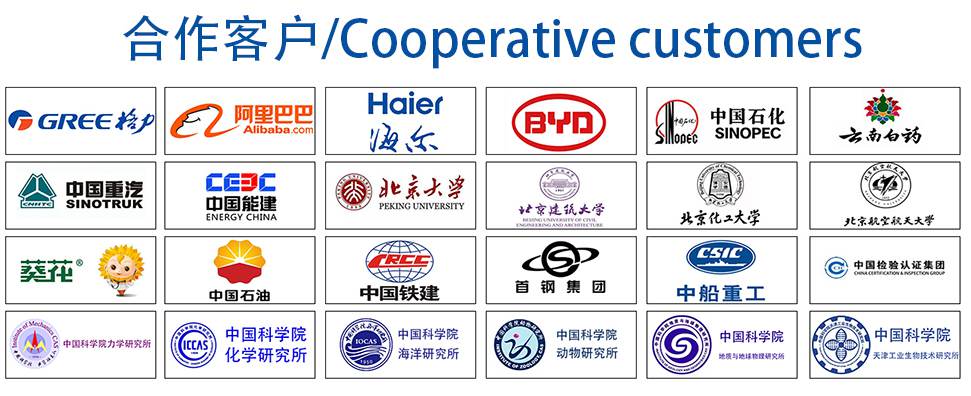
材料实验室
热门检测
276
233
208
217
215
220
228
223
231
231
220
219
222
219
213
209
227
212
224
218
推荐检测
联系电话
400-635-0567