往复运动用密封圈材料检测的重要性
往复运动用密封圈是液压系统、气动装置及机械传动设备中的关键部件,其性能直接影响设备的密封性、耐久性和安全性。在高速往复运动的工况下,密封圈材料需承受周期性摩擦、高压冲击、温度变化及介质侵蚀等多重挑战。因此,对密封圈材料的科学检测成为确保其可靠性和寿命的核心环节。通过系统化的检测项目,可全面评估材料的物理性能、化学稳定性及动态适应性,为选材优化、工艺改进和故障预防提供数据支持。
核心检测项目及内容
1. 物理机械性能检测
• 硬度测试:采用邵氏硬度计或显微硬度仪,评估材料抗压变形能力;
• 拉伸强度与断裂伸长率:通过万能材料试验机测定材料在拉伸状态下的极限承载能力;
• 压缩永久变形率:模拟长期受压工况,检测材料回弹性能是否达标(参考ISO 815标准);
• 撕裂强度:验证材料抗裂性能,预防安装或运行中发生意外破损。
2. 化学稳定性检测
• 耐介质性测试:浸泡于液压油、润滑剂、酸碱溶液等介质中,观察溶胀、溶解或脆化现象;
• 耐温性能分析:通过高低温循环试验(-40℃~200℃)评估材料热稳定性;
• 耐老化性能:采用氙灯老化箱或臭氧老化箱模拟长期使用后的性能衰减情况。
3. 动态性能测试
• 往复摩擦磨损试验:使用专用试验机模拟实际工况,记录摩擦系数变化及磨损量;
• 动态密封效率评估:在设定压力(如10~50MPa)和频率(1~5Hz)下检测泄漏量;
• 疲劳寿命测试:通过百万次以上的往复运动循环,测定材料抗疲劳性能极限。
4. 材料成分与微观结构分析
• 傅里叶红外光谱(FTIR):鉴定高分子材料的化学基团及添加剂成分;
• 扫描电镜(SEM):观察磨损表面形貌,分析失效机理;
• DSC热分析:测定玻璃化转变温度(Tg)和熔融温度(Tm),评估热力学特性。
检测标准与质量控制
检测需遵循国际通用标准(如ASTM D2000、ISO 3601)或行业规范,结合工况参数制定个性化检测方案。企业应建立全流程质量监控体系,从原材料入厂检验到成品抽检实现闭环管理。通过大数据分析检测结果,可优化材料配方并预测密封圈服役寿命,显著提升设备运行可靠性。
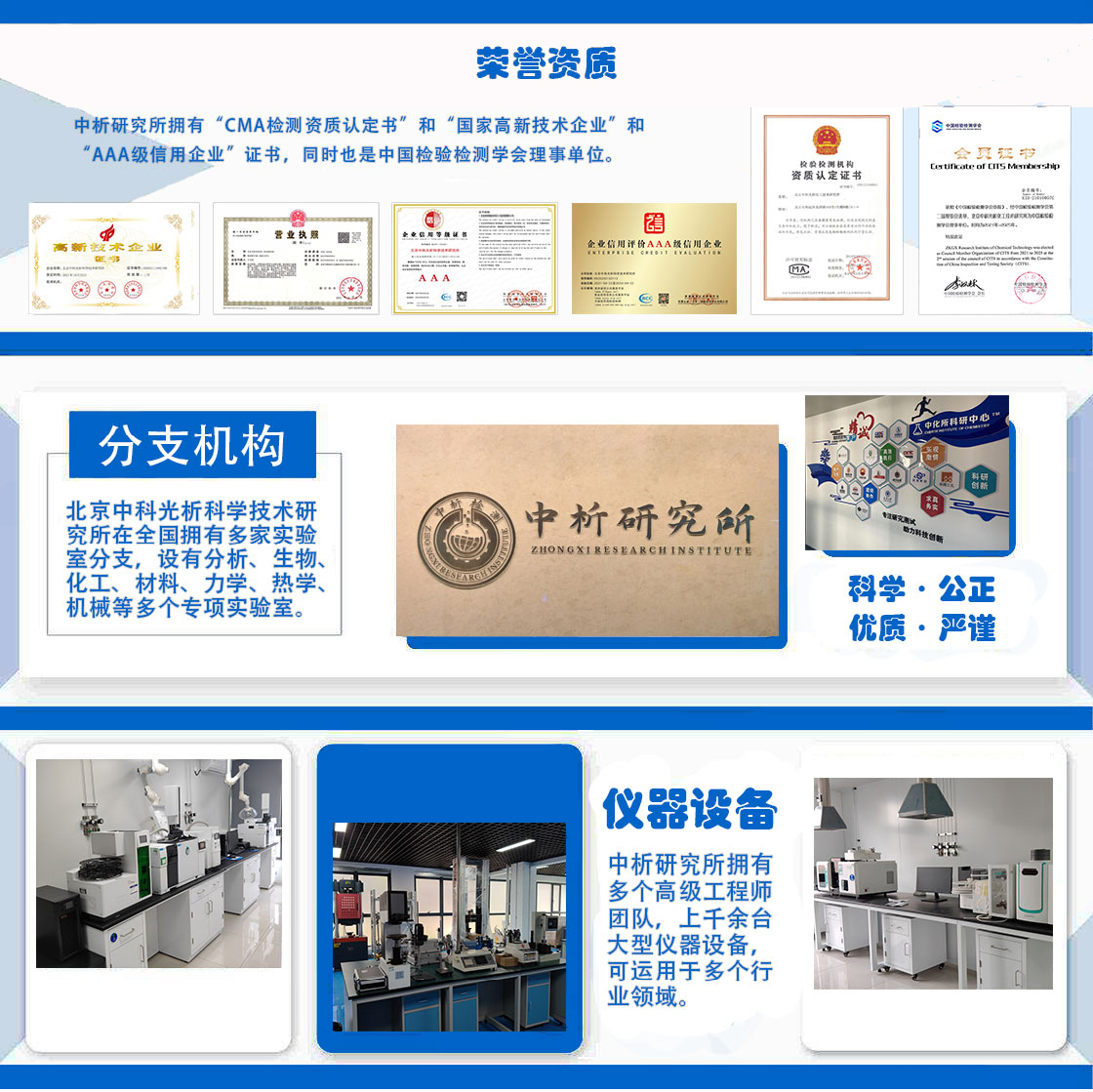
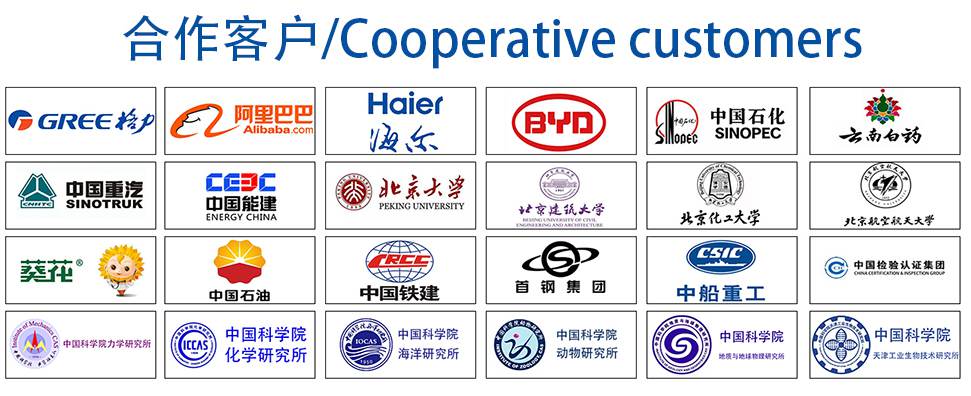