重型深孔钻镗床检测技术与关键项目解析
重型深孔钻镗床作为大型机械加工领域的核心设备,广泛应用于航空航天、能源装备、军工制造等行业的深孔加工领域。其加工精度、稳定性直接影响工件质量与生产效率,因此定期开展系统性检测是保障设备性能的关键环节。根据GB/T 23572-2009《深孔钻镗床精度检验》及ISO 3655标准要求,检测需覆盖几何精度、动态性能、功能可靠性等多个维度,并结合实际工况制定针对性检测方案。
一、几何精度检测
几何精度是衡量机床基础性能的核心指标。检测项目包括:主轴径向跳动(≤0.008mm)、主轴端面跳动(≤0.005mm)、导轨直线度误差(0.02mm/1000mm)、工作台平面度(≤0.03mm/m²)等。需使用激光干涉仪、电子水平仪等高精度仪器,结合标准试棒进行多点位测量,并依据坐标系修正误差。
二、动态性能测试
动态性能检测聚焦设备运行中的稳定性与抗振能力。主要包含:主轴高速运转温升(温升≤25℃)、进给系统重复定位精度(±0.005mm)、切削负载下振动位移量(振幅≤0.01mm)。通过振动测试仪、红外热像仪等设备模拟实际加工负载,记录关键参数波动曲线,分析传动系统刚性衰减趋势。
三、液压与冷却系统检测
深孔加工依赖高效排屑与冷却,需对液压系统进行压力稳定性(波动≤±5%)、流量均匀性(偏差<8%)检测,同时验证冷却液过滤精度(≤20μm)与循环泵组耐久性。采用压力传感器、流量计等工具,连续监测8小时工况数据,确保系统无泄漏且响应速度达标。
四、电气控制系统校验
重点验证PLC程序逻辑、伺服驱动精度及安全联锁功能。检测项包括:急停响应时间(<0.5s)、坐标轴定位误差补偿能力、过载保护触发阈值等。通过模拟故障注入测试,评估控制系统容错机制,确保符合IEC 60204-1机械电气安全标准。
五、综合加工精度验证
最终通过试件加工进行整机性能验证。选用标准试棒(直径200-500mm,长度>5m)进行深孔钻镗,检测孔径公差(IT7级)、内壁粗糙度(Ra≤1.6μm)、直线度偏差(<0.05mm/m)等指标,综合评判设备实际加工能力。
重型深孔钻镗床的检测周期建议每6个月进行一次常规检测,连续高负荷生产环境下需缩短至3个月。通过标准化检测流程与数据分析,可显著降低设备故障率,延长关键部件寿命,为企业实现精密加工提供可靠保障。
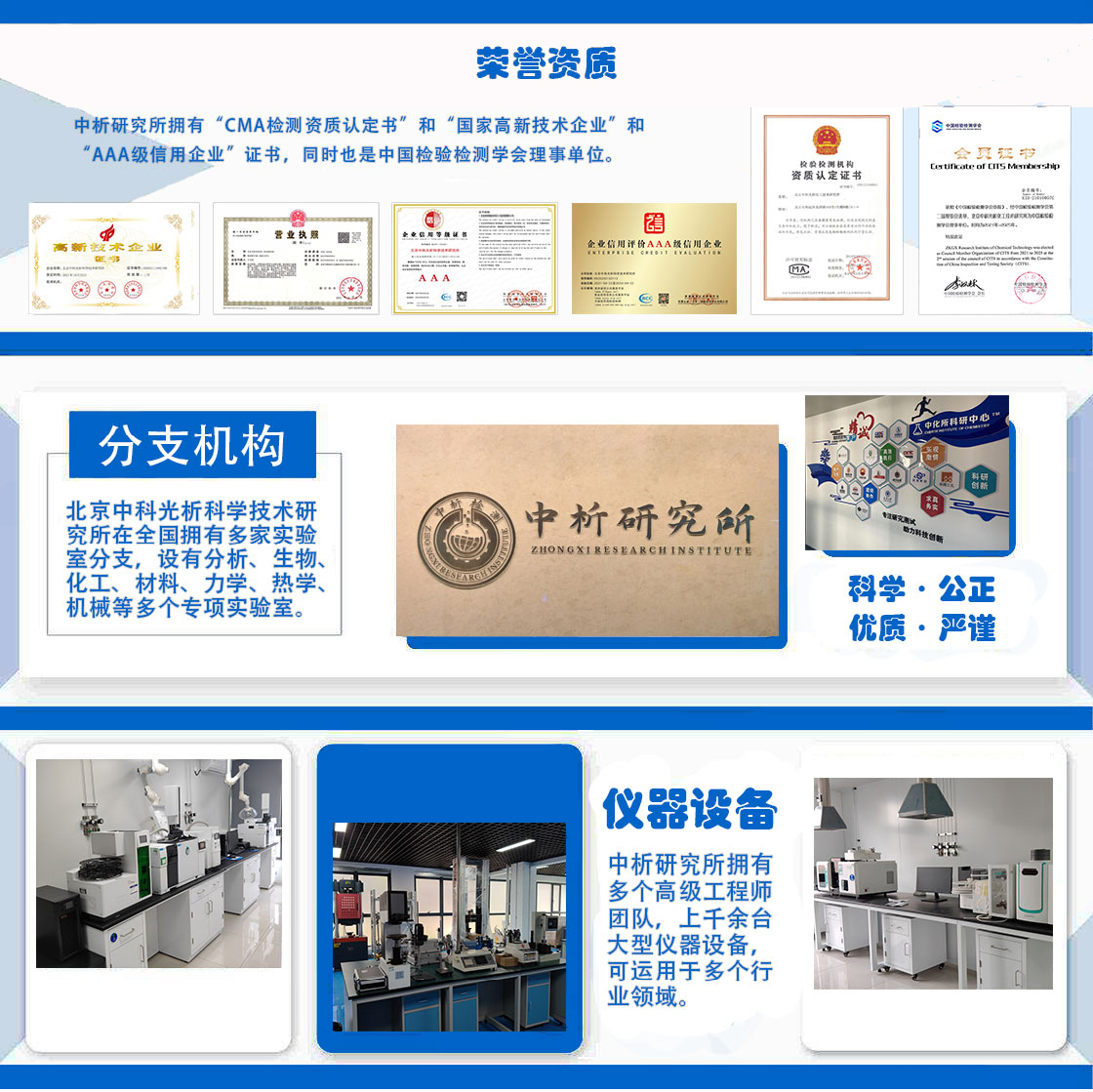
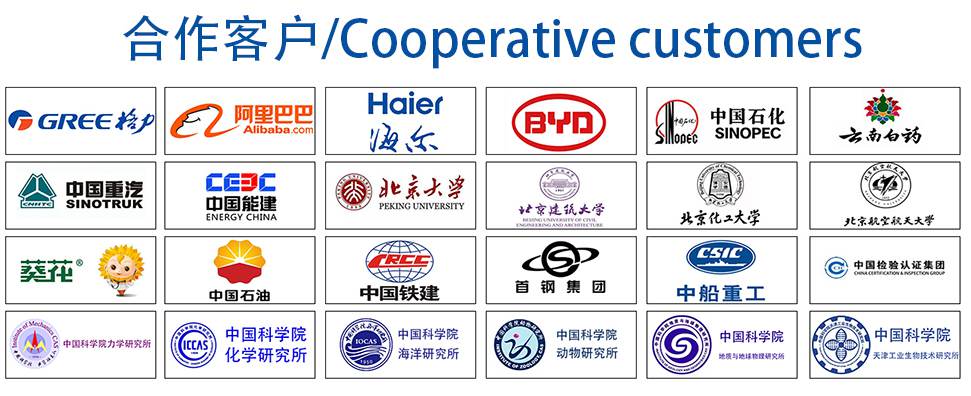