动态弯曲应力检测:核心检测项目与关键技术解析
一、动态弯曲应力检测的核心目标
- 量化疲劳寿命:预测材料的循环载荷耐受极限;
- 识别失效模式:定位裂纹萌生、扩展的关键区域;
- 验证设计参数:优化结构几何形状与材料配比;
- 评估安全系数:确保服役环境下的动态稳定性。
二、检测项目的技术细分及实施要点
1. 动态载荷谱模拟测试
- 检测内容: 复现实际工况中的动态载荷(如正弦波、随机振动、冲击载荷),记录应力-时间曲线。
- 关键技术参数:
- 频率范围:0.1Hz~1kHz(根据应用场景调整);
- 载荷幅值:±10N~±100kN(需匹配试件刚度);
- 波形控制精度:误差<±2% FS。
- 设备选型: 高频液压伺服疲劳试验机(如Instron 8800系列)或电磁激振系统(适用于高频低幅场景)。
2. 应变场动态监测
- 检测方法:
- 电阻应变片法:在试件表面粘贴应变片,采样率≥1kHz;
- 光纤光栅传感器(FBG):适用于高温、腐蚀环境;
- 数字图像相关技术(DIC):非接触式全场应变分析(精度可达0.01%)。
- 数据解析: 提取动态应变均值、幅值、相位角,构建应力-应变滞回曲线。
3. 疲劳裂纹扩展速率测定
- 测试标准: 依据ASTM E647,预制裂纹试件在ΔK(应力强度因子幅)控制下的扩展行为。
- 关键输出: da/dN(裂纹扩展速率)与ΔK关系曲线,确定Paris公式参数(C、m)。
4. 动态应力集中系数评估
- 实验设计: 在试件几何突变区域(如孔洞、焊缝)布设应变片,对比理论计算值(如有限元仿真)与实测值差异。
- 优化策略: 通过倒角设计、局部强化降低应力集中系数(Kt值)。
5. 材料阻尼特性测试
- 检测意义: 量化材料在动态载荷下的能量耗散能力(阻尼比ζ)。
- 测试方法: 自由衰减法或共振驻波法,结合FFT频谱分析计算损耗因子。
三、典型应用案例分析
- 载荷谱设计:模拟加速-制动循环(频率0.5~5Hz,最大弯矩45kN·m);
- 应变监测方案:沿轴向布置12组应变片,采样率10kHz;
- 结果分析:
- 识别轮毂压装处为应力集中点(实测Kt=2.1,理论值1.8);
- 优化热处理工艺后,疲劳寿命提升30%。
四、检测技术发展趋势
- 多物理场耦合测试:同步监测温度-应力-振动信号(如红外热像仪+应变仪);
- AI驱动的预测模型:基于LSTM神经网络预测剩余疲劳寿命;
- 微型化传感器集成:MEMS应变传感器实现嵌入式实时监测。
五、
上一篇:镍上镀金层孔隙率检测下一篇:电快速瞬变脉冲群抗扰度检测
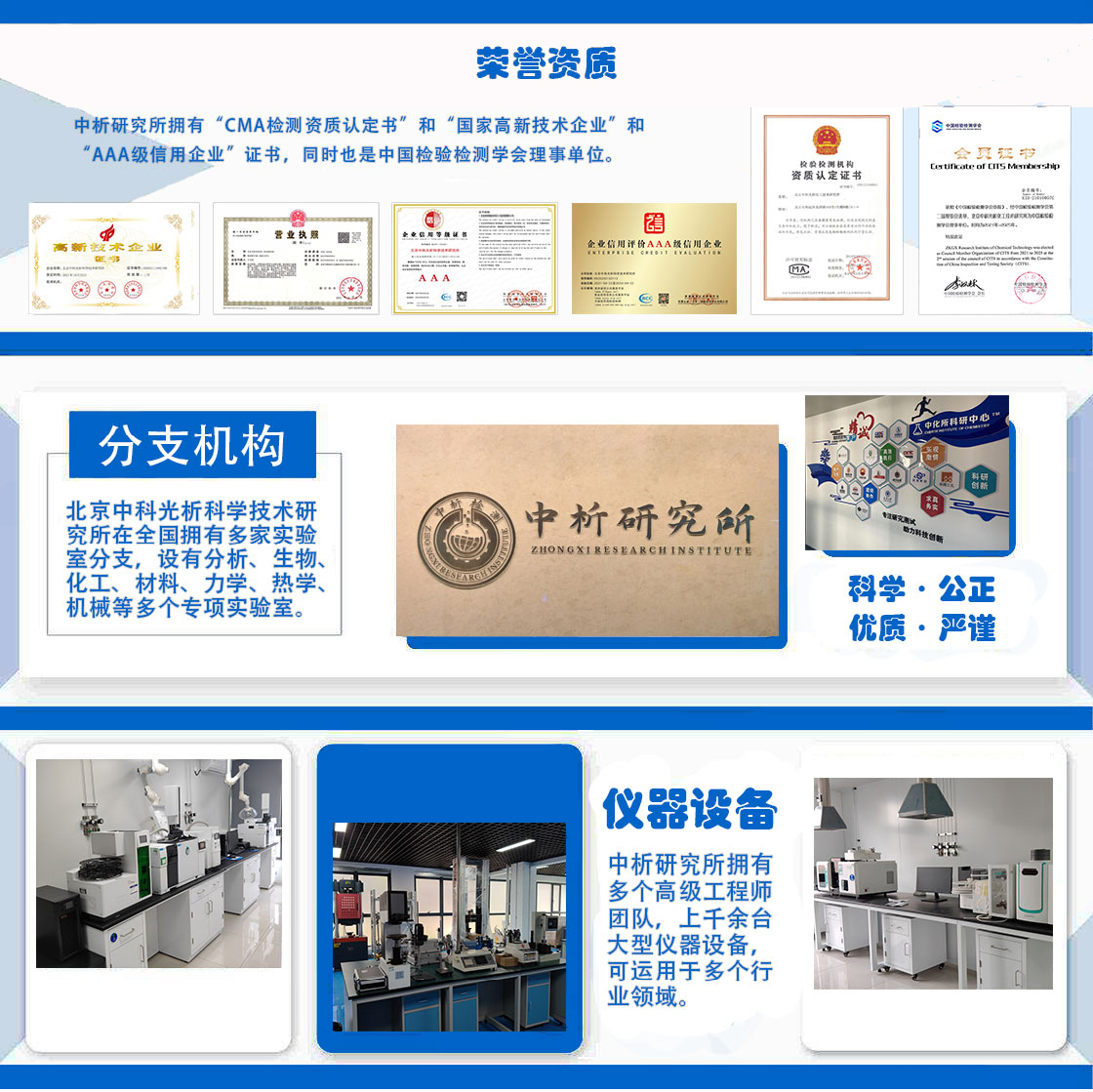
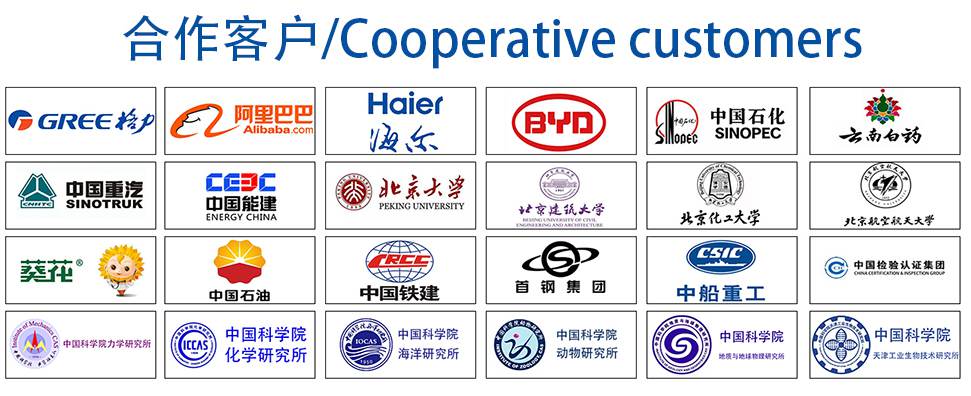
材料实验室
热门检测
269
227
202
211
209
211
224
217
228
229
212
213
216
214
207
204
221
207
220
213
推荐检测
联系电话
400-635-0567