弓曲与扭曲检测:核心检测项目解析
一、检测标准与规范
- IPC-6012(电子电路板):规定PCB弓曲度范围不超过0.75%~1.5%,具体取决于板厚。
- JIS B 7021(精密机械部件):要求关键传动部件扭曲角度偏差≤0.05°。
- ASTM D1184(复合材料层压板):基于厚度划分允许变形阈值,例如厚度≤3mm时,弓曲度上限为0.5mm/m。
二、核心检测项目及参数
-
- 定义:材料表面相对于理想平面的最大垂直偏差。
- 检测项:
- 整体弓曲度:全平面最高点与最低点的高度差(如PCB板四角悬空时的中心凹陷量)。
- 局部弓曲度:特定区域(如焊盘周围)的变形量,用于评估焊接可靠性。
- 工具:激光轮廓仪、三点接触式测微计。
-
- 定义:材料对角线方向上的非对称扭转程度。
- 检测项:
- 对角线扭曲量:测量两对对角的Z轴高度差,计算扭曲角度。
- 扭矩传递效应(适用于轴类零件):通过模拟负载测试扭曲刚度。
- 工具:光学干涉仪、数字图像相关(DIC)系统。
-
- 检测项:在-40°C~150°C温箱中循环测试,记录弓曲/扭曲量变化率。
- 应用场景:汽车电子、航天器部件需满足极端环境下的抗变形能力。
三、前沿检测技术
-
- 技术亮点:采用结构光或激光三角测量法,生成3D表面点云,精度达±0.01mm。
- 案例:半导体封装中BGA基板的实时在线检测。
-
- 技术亮点:通过卷积神经网络(CNN)识别变形特征,自动分类缺陷等级。
- 优势:检测速度提升50%,误判率低于0.1%。
-
- 技术亮点:用于多层复合材料内部应力分布分析,预测潜在扭曲风险。
- 适用领域:航空发动机叶片、碳纤维增强塑料(CFRP)部件。
四、行业应用案例
-
- 需求:铝合金CNC加工后的弓曲度需≤0.1mm,确保屏幕贴合无缝隙。
- 方案:高精度气浮平台搭配蓝光扫描仪,全检周期<10秒/件。
-
- 挑战:涂布烘烤后的极片扭曲导致叠片错位。
- 对策:红外热成像监测烘烤温度场均匀性,结合在线纠偏系统控制扭曲量<0.3mm。
-
- 标准:模腔扭曲容忍度±0.005mm,防止塑料件缩水变形。
- 检测流程:三坐标测量机(CMM)搭配温度补偿算法,消除环境干扰。
五、数据驱动的质量控制
- SPC(统计过程控制):实时采集产线检测数据,绘制X-bar控制图,识别工艺波动趋势。
- 闭环反馈系统:将检测结果自动反馈至加工设备(如CNC补偿加工参数),实现零缺陷生产。
结语
- 《基于深度学习的多材料构件变形实时监测技术》
- 《ISO 1101:2017 几何公差标准在复杂曲面检测中的应用》
上一篇:热冲击后剥离强度检测下一篇:外观和尺寸检测
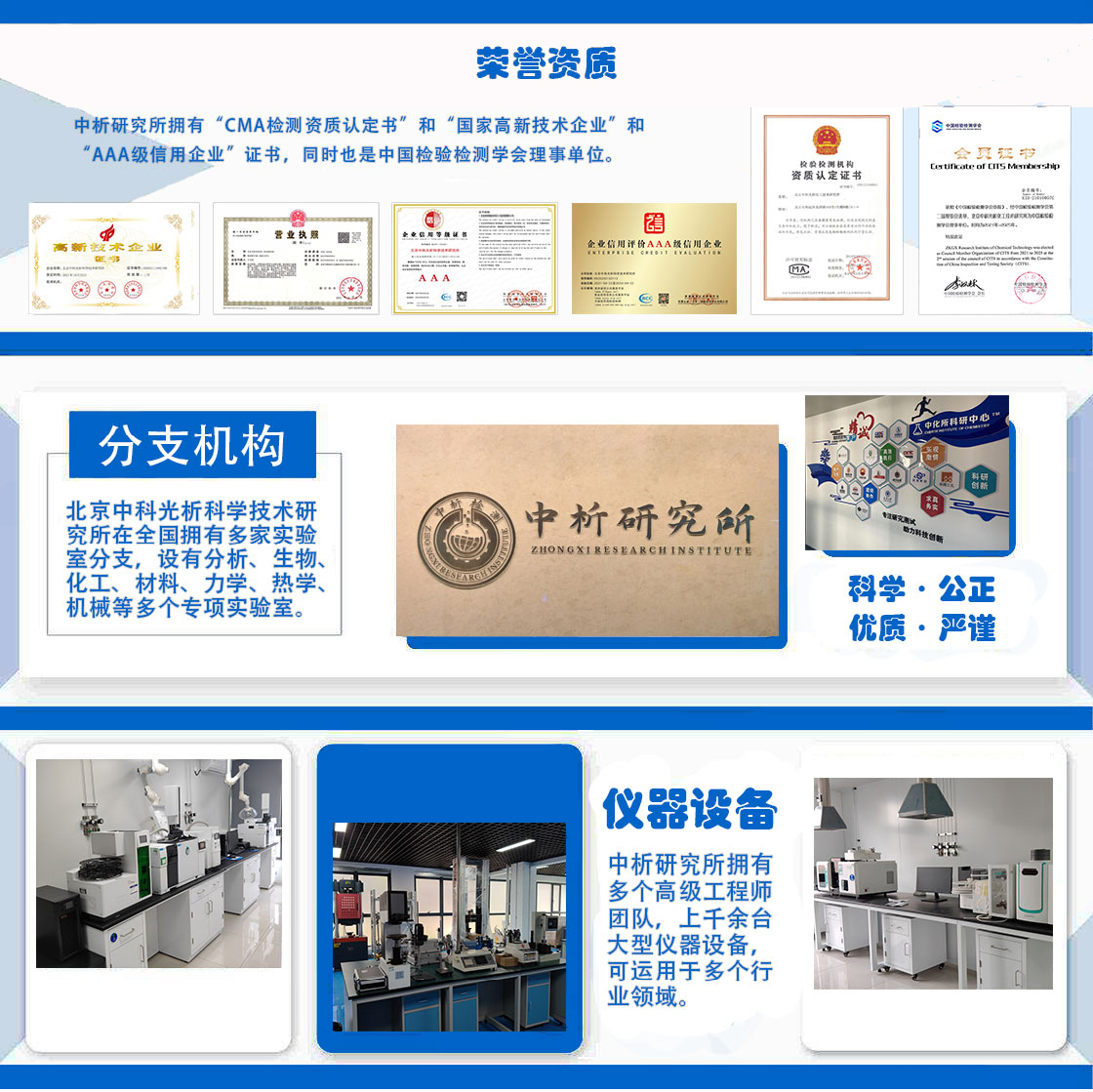
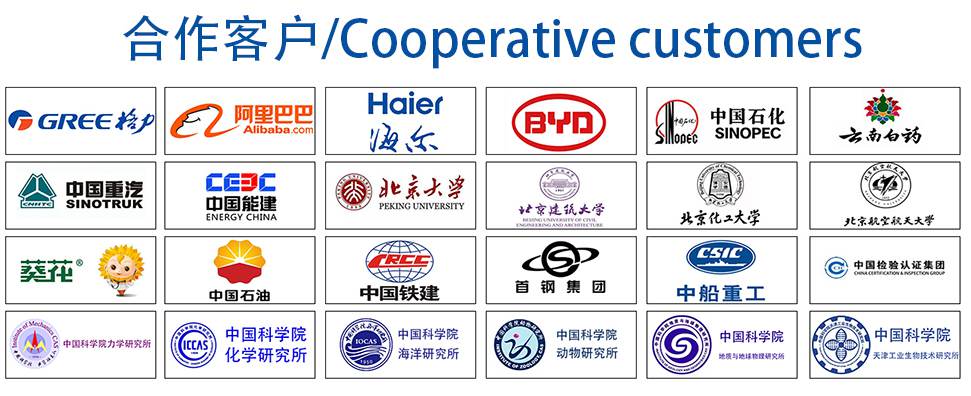
材料实验室
热门检测
269
227
202
211
208
211
224
217
228
229
212
213
216
214
207
204
221
207
220
213
推荐检测
联系电话
400-635-0567