热冲击后剥离强度检测:核心项目与技术要点
一、热冲击预处理条件设定
1. 温度范围与循环参数
- 低温/高温极值:根据应用场景选择极限温度(如-55℃
125℃适用于电子元件,-40℃180℃适用于航空航天涂层)。 - 驻留时间:每温度区间停留时间需确保试样达到热平衡(通常15~30分钟,依据试样厚度调整)。
- 循环次数:模拟长期使用环境,常见25~1000次循环(ASTM D6677建议至少50次)。
- 转换速率:温度变化速率影响热应力,需记录升/降温时间(如10℃/min)。
2. 试样预处理规范
- 温湿度调节:测试前需在标准环境(23±2℃,50±5% RH)中平衡48小时(ISO 291)。
- 边缘效应防护:对试样边缘进行密封处理,避免热冲击导致边缘剥离提前失效。
二、剥离强度检测核心项目
1. 剥离模式选择
- T型剥离(ASTM D1876):适用于对称结构(如金属-金属粘接)。
- 180°剥离(ASTM D903):用于薄膜、柔性材料与刚性基材的剥离测试。
- 90°剥离(ISO 8510-2):模拟弯曲应力场景,常见于电子柔性电路板。
2. 测试设备与参数
- 万能材料试验机:精度±1%,加载速度100±10 mm/min(参照ASTM标准)。
- 实时数据采集:记录载荷-位移曲线,计算平均剥离强度(单位N/mm)。
- 环境箱集成:高温或低温环境下进行原位测试(如-70℃~300℃温控箱)。
3. 失效模式分析
- 界面失效(Adhesive Failure):粘接剂与基材完全分离,表明界面结合力不足。
- 内聚失效(Cohesive Failure):破坏发生在粘接剂内部,反映材料自身强度缺陷。
- 混合失效:量化两种失效模式占比(如80%内聚+20%界面),辅助工艺优化。
三、关键检测指标与评价标准
1. 强度阈值判定
- 最低接受值(MAV):依据行业标准设定(如汽车行业≥3 N/mm)。
- 标准差分析:同一批次试样离散度应小于15%(确保工艺稳定性)。
2. 强度衰减率计算
- 公式:衰减率=(原始强度-热冲击后强度)/原始强度×100%。
- 分级评价:
- Ⅰ级(衰减≤10%):优异抗热冲击性能。
- Ⅱ级(10%~30%):需改进工艺或材料。
- Ⅲ级(衰减>30%):不符合可靠性要求。
3. 微观结构关联分析
- SEM/EDS检测:观察界面裂纹扩展路径及元素分布,解析失效机理。
- DSC/TGA辅助测试:评估粘接剂玻璃化转变温度(Tg)变化对性能的影响。
四、国际标准对照与选择建议
标准号 | 适用范围 | 核心差异 |
---|---|---|
ASTM D3167 | 纤维增强塑料层压板 | 侧重高刚度材料低速剥离 |
ISO 11339 | 柔性-刚性材料粘接 | 允许定制剥离角度 |
JIS K6854 | 胶粘剂通用测试 | 强调环境预处理条件 |
GB/T 2790 | 中国国标软质材料剥离 | 简化数据处理流程 |
五、案例分析:某PCB柔性电路板热冲击测试
1. 测试条件
- 热冲击:-40℃(30min)←→125℃(30min),100次循环。
- 剥离测试:90°模式,速度50 mm/min,5组试样。
2. 结果与改进
- 初始强度:4.2 N/mm → 热冲击后降至2.8 N/mm(衰减33%)。
- 失效模式:70%界面失效(环氧树脂与铜箔结合不良)。
- 改进措施:增加等离子体表面处理,衰减率降至12%。
六、
- 开发多物理场耦合测试(温度+湿度+振动)。
- 基于机器学习的剥离强度预测模型构建。
上一篇:电快速瞬变脉冲群抗扰度检测下一篇:弓曲和扭曲检测
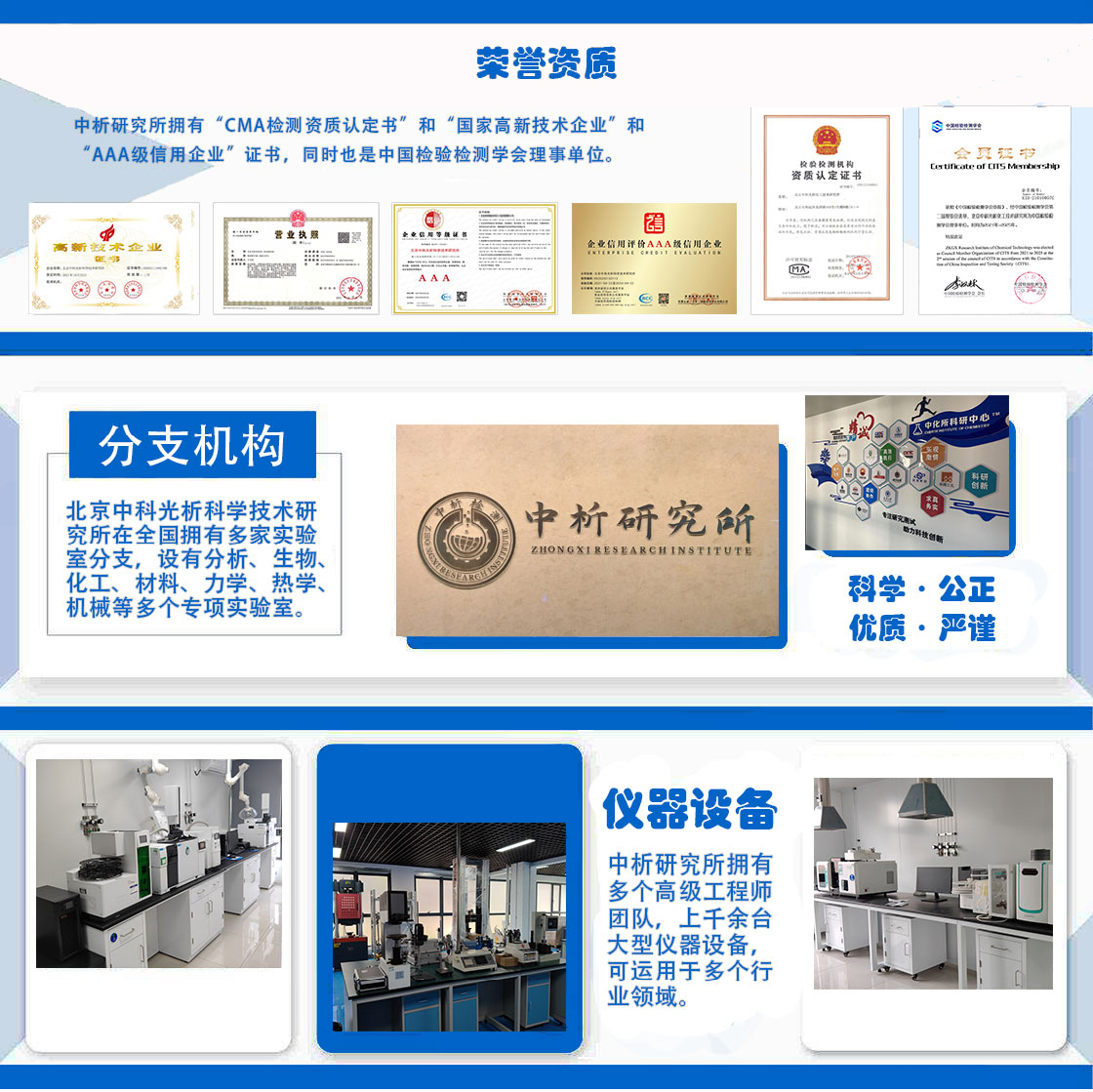
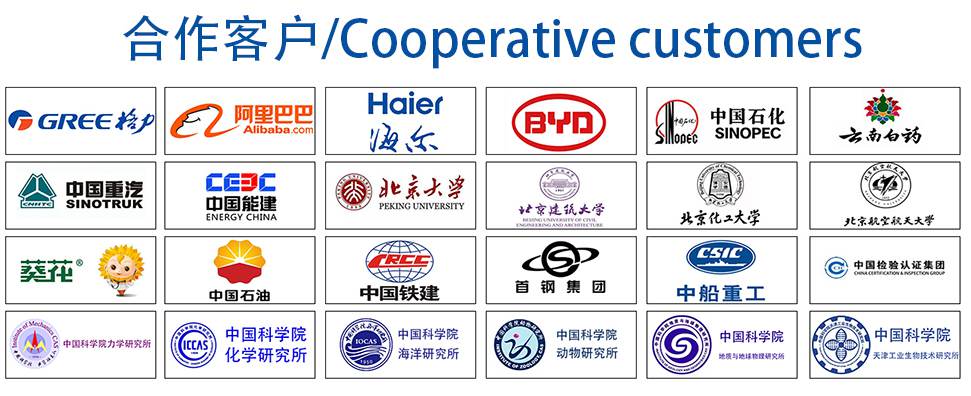
材料实验室
热门检测
269
227
202
211
208
211
223
217
228
229
212
213
216
214
207
204
221
207
220
213
推荐检测
联系电话
400-635-0567