镀层厚度检测:核心检测项目与关键技术解析
一、镀层厚度检测的核心项目
-
- 重要性:确保镀层整体厚度符合设计规范,避免因过薄导致性能失效或过厚增加成本。
- 方法:
- X射线荧光光谱法(XRF):非破坏性,适用于多镀层分析(如镍+金镀层)。
- 金相显微镜法:(破坏性)切割样品后观察截面,精度达±0.1μm。
- 标准:ISO 3497、ASTM B568。
-
- 应用场景:螺钉螺纹、连接器触点等高磨损部位。
- 仪器:涡流测厚仪(磁性基体)、β反向散射仪(非磁性基体)。
- 数据要求:单点厚度偏差≤±10%标称值。
-
- 检测方法:
- 多点扫描法:通过XRF或涡流仪在表面网格化取点(通常≥9点/m²)。
- 热震试验:验证厚度均匀性对结合力的影响(如150℃烘烤后急冷)。
- 判定标准:厚度极差(最大值-最小值)≤平均厚度的20%。
- 检测方法:
-
- 关键工艺验证:电镀前处理不良易导致镀层剥落。
- 试验方法:
- 划格试验:刀刃间隔1mm划格,胶带撕拉后镀层脱落面积<5%。
- 弯曲试验:180°折弯基材,镀层无开裂(ASTM B571)。
-
- 盐雾试验:按中性盐雾(NSS)、铜加速盐雾(CASS)分级:
- 汽车部件:96小时无红锈(ASTM B117)。
- 孔隙率检测:铁氰化钾试纸法(孔隙点≤5个/cm²)。
- 盐雾试验:按中性盐雾(NSS)、铜加速盐雾(CASS)分级:
二、检测方法的选择策略
方法 | 精度(μm) | 破坏性 | 适用场景 |
---|---|---|---|
金相显微镜法 | ±0.1 | 是 | 实验室高精度仲裁检测 |
X射线荧光法 | ±0.5 | 否 | 多层镀层在线检测 |
涡流法 | ±1.0 | 否 | 磁性基体快速筛查 |
三、影响检测结果的关键因素
-
- 例:锌合金基体电镀铜需预镀氰化铜,防止置换反应导致结合不良。
-
- Ra>0.8μm时,XRF检测误差增加,需采用截面补偿算法。
-
- 涡流法在温度波动>5℃时需重新校准,湿度>80%可能影响电化学测试。
四、行业应用案例
- 电子连接器:镀金层厚度0.2-0.5μm,需100%在线XRF检测以确保阻抗稳定性。
- 汽车紧固件:锌镍镀层≥8μm,盐雾试验≥720小时,结合力划格测试达0级。
五、
- 日常生产中采用非破坏性方法(如XRF)进行全检;
- 定期抽样进行破坏性试验(金相法、结合力测试);
- 结合功能需求定制检测方案(如高频PCB需额外检测镀层表面粗糙度)。
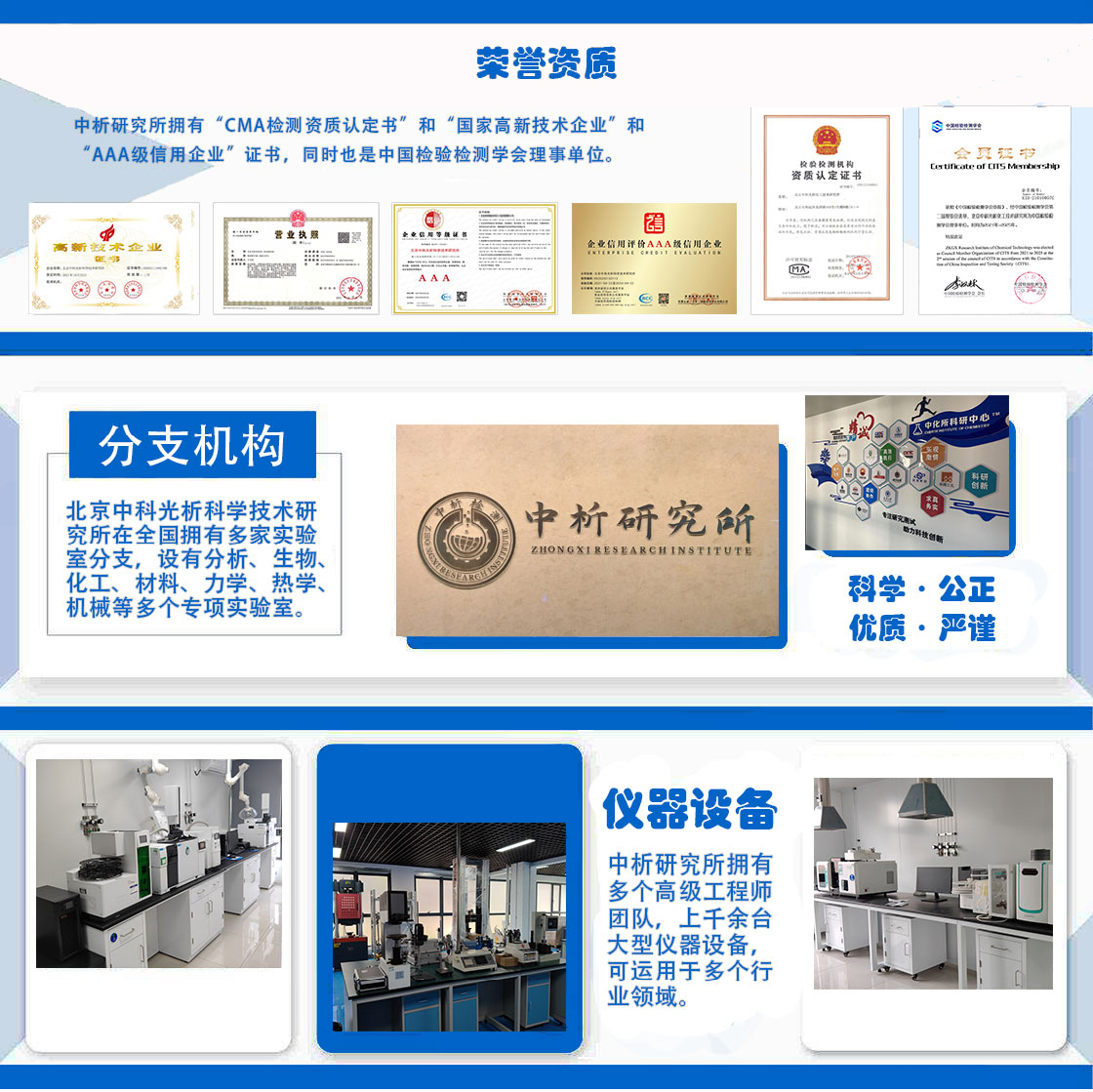
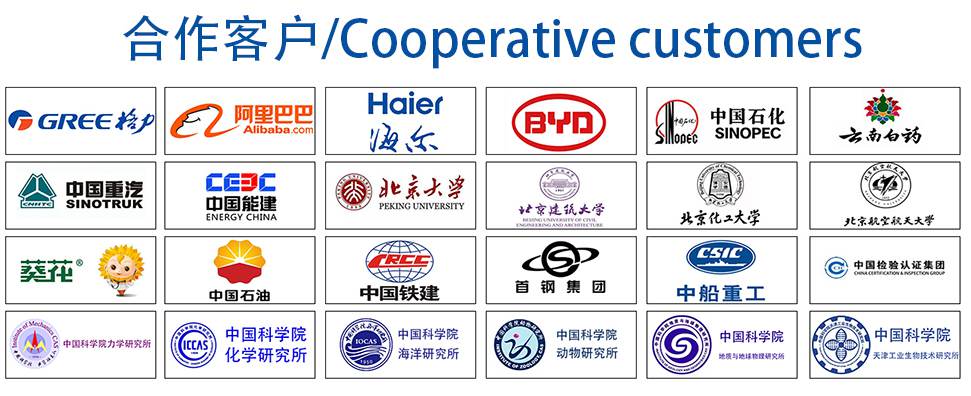
材料实验室
热门检测
269
227
202
211
209
211
224
217
228
229
212
213
216
214
207
204
221
207
220
213
推荐检测
联系电话
400-635-0567