一、检测原理与系统构成
- 加载模块:采用伺服液压系统(精度±0.5%FS)或电磁激振器(频率范围0-2000Hz)
- 传感系统:包含光纤光栅传感器(分辨率1με)、应变片式扭矩传感器(精度0.1级)
- 数据采集系统:高速采集卡(采样率≥1MHz)配合LabVIEW平台
二、核心检测项目规范
- 动态扭矩刚度系数
- 检测标准:ISO 6721-2:2019
- 测试方法:施加0.2%屈服扭矩的循环载荷(频率扫描1-100Hz)
- 关键指标:相位角滞后(φ)、储能模量(G')、损耗模量(G'')
- 典型值范围:碳钢结构tanδ<0.01,橡胶基复合材料tanδ可达0.3
- 疲劳寿命评估
- 执行ASTM E2368标准
- 加速试验方法:采用梯形波载荷(上升时间0.1s,保持0.5s)
- 数据采集:记录裂纹萌生点(应变突变≥5%)、裂纹扩展速率(da/dN)
- 典型曲线:S-N曲线在10^6次循环时应力幅下降至静态强度30%
- 热-力耦合检测
- 温度控制:-70℃~300℃温箱(梯度±2℃/min)
- 同步测量:红外热像仪(空间分辨率0.1mm)与DIC系统配合
- 关键参数:温度-应力耦合系数(dσ/dT)、热滞后环面积
- 微观损伤识别
- 在线监测技术:
- 声发射传感器(频率范围20-400kHz)
- 非线性超声检测(二次谐波系数β>10^-10 m/W)
- 特征提取:小波包能量熵(阈值0.85)、Hilbert-Huang变换
三、技术难点与解决方案
- 多物理场耦合建模
- 建立包含J2塑性本构的动力学方程: �∂2�∂�2=∂∂�(��∂�∂�)+�(�,�)ρ∂t2∂2θ=∂x∂(GJ∂x∂θ)+q(x,t)
- 采用COMSOL Multiphysics进行流固耦合仿真(网格尺寸<0.1mm)
- 信号去噪处理
- 开发改进型VMD算法:
- 自适应分解层数K=8
- 惩罚因子α=2000
- 信噪比提升15dB以上
- 不确定度分析
- 蒙特卡洛法量化误差源:
- 传感器非线性误差(±0.3%)
- 温度漂移(0.05%FS/℃)
- 动态响应延迟(<50μs)
四、创新发展趋势
- 智能传感技术:MEMS陀螺阵列(尺寸5×5×2mm)实现三维扭转变形测量
- 数字孪生应用:建立包含材料微观结构特征的虚拟样机,预测精度提升40%
- 机器学习算法:深度卷积网络(ResNet-50)实现损伤识别准确率98.7%
- 早期裂纹检出时间提前300小时
- 刚度系数测量重复性误差<0.8%
- 疲劳寿命预测误差从±25%降低到±8%
- 宏观应变场与微观位错运动的关联分析
- 太赫兹波(0.1-10THz)在复合材料内部的传播特性
- 量子传感技术在微扭矩测量中的应用(灵敏度10^-8 N·m/√Hz)
上一篇:冷却引起的热时间常数检测下一篇:便携电子设备用密封二次电池和电池组检测
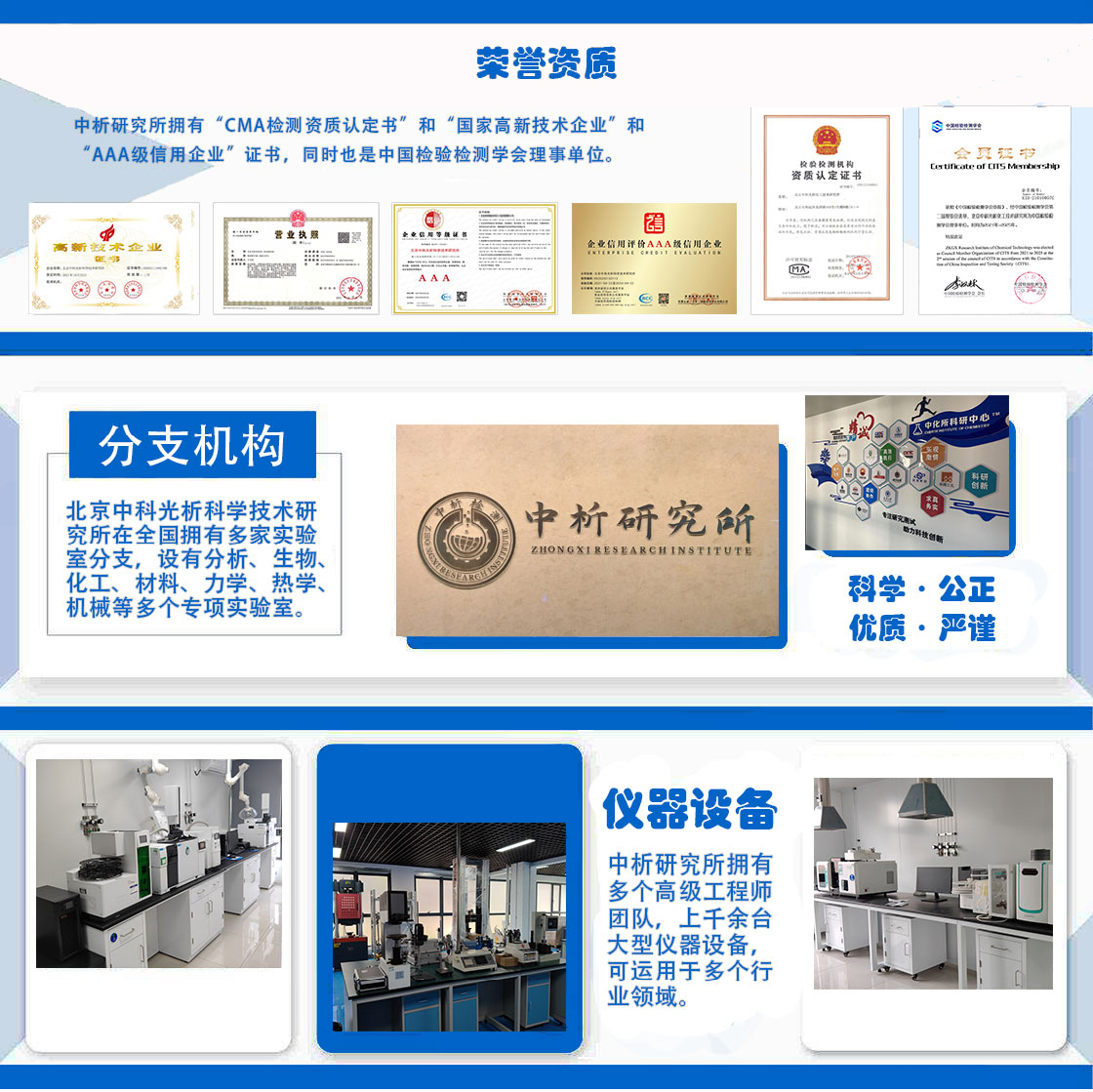
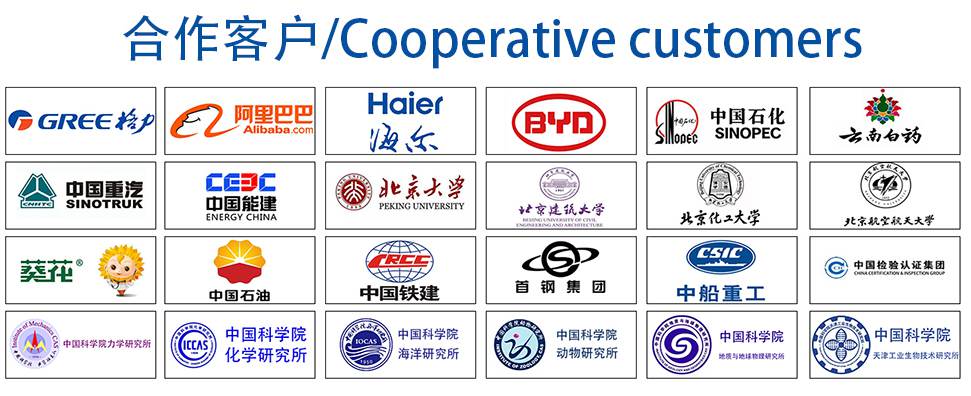
材料实验室
热门检测
265
222
201
209
204
207
219
211
222
223
209
209
213
211
203
201
216
206
213
209
推荐检测
联系电话
400-635-0567