工业用二次单体电池检测体系解析
随着新能源产业的快速发展,工业用二次单体电池(即可充电电池,如锂离子电池、镍氢电池等)在储能系统、电动车辆、工业设备等领域的应用日益广泛。这类电池的性能、安全性和使用寿命直接影响终端设备的运行效率与安全性。为保障电池在全生命周期内满足工业场景的严苛需求,建立系统化的检测体系已成为生产制造和质量控制的核心环节。
核心检测项目分类
1. 安全性能测试
包括过充/过放测试(模拟极端充放电条件)、短路测试(验证保护电路有效性)、热冲击试验(评估电池在温度骤变下的稳定性)以及针刺/挤压测试(模拟机械损伤下的安全表现)。测试依据国际标准IEC 62133-2及GB/T 31485执行,确保电池在滥用条件下不起火、不爆炸。
2. 电化学性能检测
覆盖容量测试(验证标称容量与实际输出的一致性)、内阻测量(监控电池老化程度)、倍率放电性能(评估高负荷场景下的输出能力)及自放电率分析(检测电池存放期的能量损耗)。此类数据通过充放电测试系统(如Arbin BT2000)采集,为电池匹配应用场景提供关键参数。
3. 环境适应性验证
通过高温存储(55-85℃)、低温循环(-20℃)、湿热老化(85%RH)等试验模拟实际工况,检测电池在极端温湿度条件下的容量保持率和结构完整性。尤其针对户外储能系统,需额外增加盐雾腐蚀、振动冲击等专项测试。
4. 循环寿命评估
采用加速老化试验(如1C倍率循环充放电)预测电池在标准循环次数(通常≥2000次)后的容量衰减曲线,结合容量保持率≥80%的行业门槛值判断电池经济使用寿命。该测试需持续监控电压平台变化及内阻增长趋势。
5. 结构及材料检测
利用CT扫描检测极片对齐度,SEM观察电极材料形貌,XRD分析晶体结构稳定性。同时对隔膜穿刺强度、电解液闪点等关键材料参数进行实验室验证,确保电池设计与生产工艺符合设计要求。
6. 一致性测试
针对批量生产的电池组,通过统计学方法(如CPK≥1.33)评估开路电压、容量、内阻等参数的离散程度。采用红外热成像技术监测电池组工作时的温度分布均匀性,预防因单体差异导致的系统失效。
检测标准与认证体系
工业用二次电池需满足UN38.3运输安全认证、UL 1973储能系统标准、GB/T 34013动力电池规范等强制性要求。部分高端应用场景还需通过ISO 12405-4电动商用车电池组测试或IEC 62619工业设备电池安全认证。
结语
工业用二次单体电池的检测体系是保障其可靠性的技术基石,贯穿研发验证、生产质控及服役监测全流程。随着固态电池、钠离子电池等新技术的发展,检测项目将持续迭代升级,推动建立更完善的电池全生命周期管理标准。
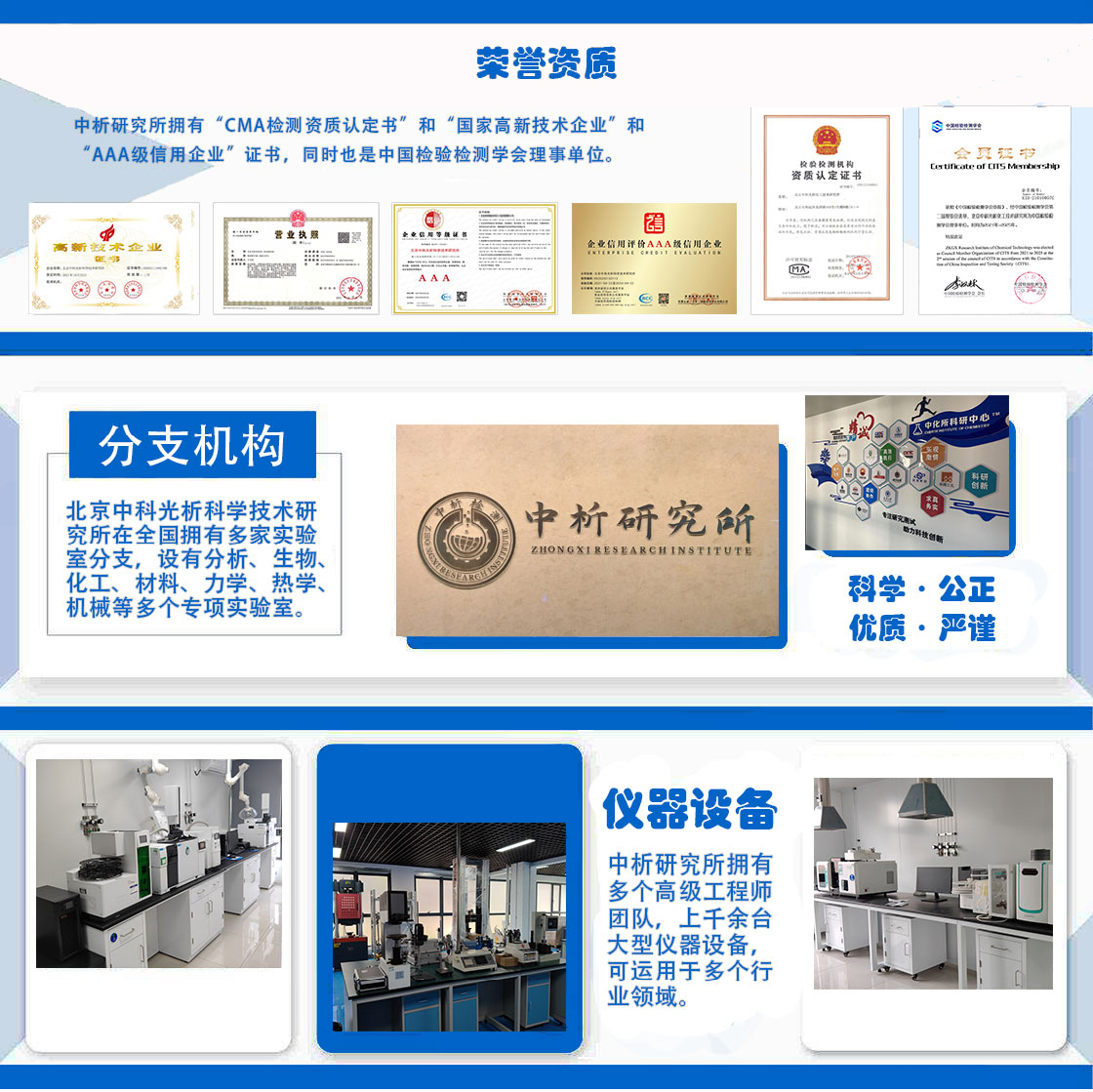
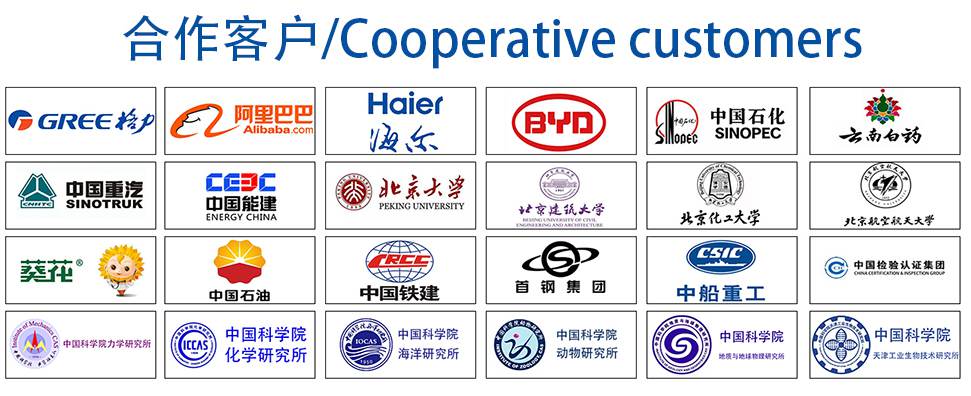