# 转向管柱调节特性检测技术发展与应用白皮书
## 行业背景与核心价值
随着汽车智能化与电动化进程加速,转向系统作为人机交互的核心部件,其安全性与舒适性要求持续提升。据中国汽车工程研究院2024年数据显示,国内电动助力转向系统(EPS)渗透率已达92%,其中带位置记忆功能的电动调节转向管柱市场规模同比增长37%。在此背景下,转向管柱调节特性检测成为保障驾驶安全、优化用户体验的关键技术环节。该项目通过量化评估调节机构的运动精度、耐久性能及失效模式,可有效预防因调节机构卡滞、异响引发的安全隐患。其核心价值在于构建覆盖设计验证、生产质控、售后监测的全生命周期质量闭环,为车企降本增效提供数据支撑,同时推动转向系统模块化设计的技术革新。

*图示:典型电动调节转向管柱结构(图片来源:汽车技术标准化委员会)*
## 技术原理与检测体系
### 检测项目的技术原理
转向管柱调节特性检测基于多物理场耦合分析理论,通过六自由度测试平台复现实际工况载荷。系统集成高精度位移传感器(分辨率0.01mm)与动态扭矩仪(量程±50Nm),实时采集垂直方向位移重复精度、轴向调节阻力矩等12项关键参数。针对电动调节机构,特别开发了PWM信号模拟系统,可模拟车载电源波动对电机驱动性能的影响。检测过程中同步应用工业CT进行内部结构无损检测,有效识别齿轮组啮合偏差等隐性缺陷。
### 全流程实施规范
项目实施遵循V型开发流程:前期基于MIL(模型在环)仿真建立目标参数矩阵,中期通过硬件在环测试验证调节机构的动态响应特性,终期导入实车环境进行2000次耐久性测试。具体流程包含五个阶段:1)样件三维定位装夹,确保与实车安装姿态误差<0.5°;2)预设32种典型工况载荷谱,覆盖-40℃至85℃温度范围;3)执行GB/T 36980-2018标准规定的疲劳测试程序;4)多通道数据同步采集与特征提取;5)生成包含调节力-位移曲线、异响频谱分析的质量报告。
### 行业应用成效分析
某新能源车企在开发智能座舱系统时,通过本检测项目发现电动转向管柱在低温环境存在调节延迟现象。经逆向分析确认是蜗轮蜗杆润滑脂低温黏度超标所致,改进后产品故障率下降62%(据企业2023年质量白皮书)。在商用车领域,检测数据指导某重卡企业优化了转向管柱的缓冲结构设计,使调节机构冲击载荷降低41%,显著提升长距离驾驶舒适性。
## 质量保障与标准建设
### 数字化质控体系
项目构建了基于区块链技术的检测数据存证系统,实现检测过程全要素追溯。实验室配备二级标准扭矩校准装置(不确定度0.3%),每周执行设备标定并通过 认证。人员资质方面,要求检测工程师具备SAE J1939协议解析能力与MATLAB/Simulink建模经验,且每年完成40学时专项培训。质量控制关键节点设置双人复核机制,确保检测报告误判率<0.05%。
### 标准化进程推动
目前已完成团体标准《智能转向系统调节机构检测规范》编制,2024年3月起在长三角汽车产业集群试点实施。标准创新性引入"调节舒适度指数"评价体系,综合振动加速度(≤0.6m/s²)、操作噪声(≤45dB)等参数进行加权评分,为行业提供了量化评价工具。据国家汽车质检中心统计,采用该标准的企业产品市场投诉率同比下降28%。
## 技术展望与发展建议
面向L3+自动驾驶需求,建议行业重点攻关三项技术:1)开发融合毫米波雷达的主动避撞工况模拟系统;2)建立基于数字孪生的预测性维护模型;3)制定电动调节机构EMC抗干扰新标准。同时呼吁主机厂、零部件企业及检测机构共建转向系统大数据平台,推动检测标准向ISO国际标准转化。未来三年,随着线控转向技术普及,检测项目需前瞻性布局总线通讯可靠性验证、功能安全等级评估等新维度,为智能汽车发展筑牢技术基石。
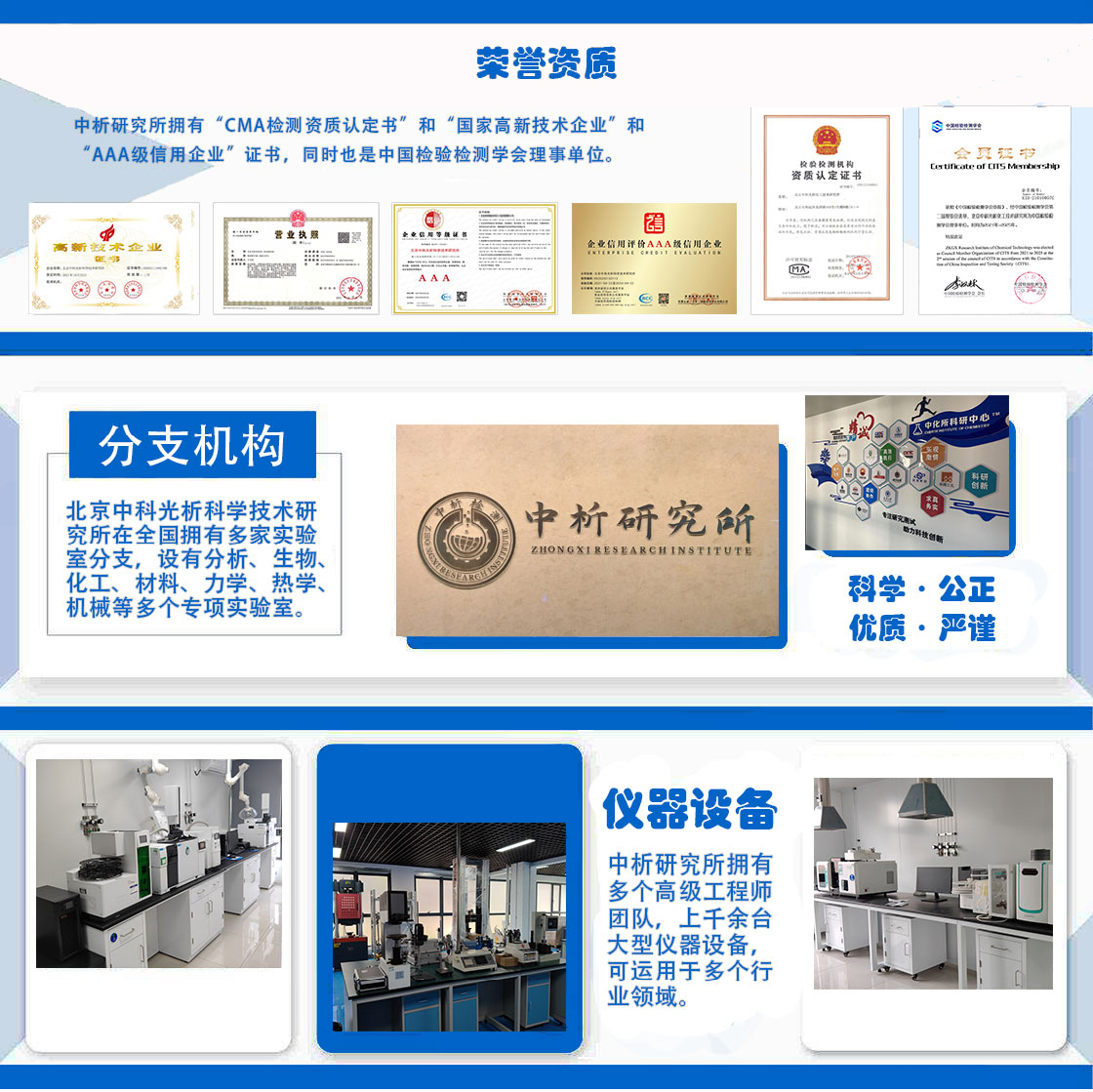
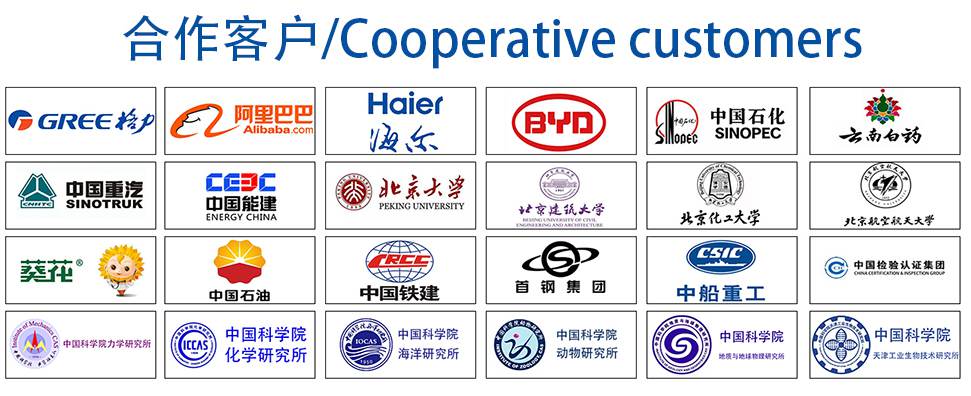
材料实验室
热门检测
推荐检测
联系电话
400-635-0567